anapulse (sludge blanket digester)
Reading time:This granular sludge bed reactor is the most frequently used, and is suitable for effluents that lead to the formation of this type of sludge (see anaerobic bacterial cultures).
design
reactor (figure 2)
In this upflow type reactor, the effluent distributed over the base of the reactor passes through the sludge blanket. The sludge then moves on to a separation zone where the biogas is first removed from the three-phase mixture: granular sludge (often floated on the gas bubbles that adhere to the sludge) – treated water – biogas bubbles (rapid change in direction causing the bubbles to detach from the sludge and biogas collectors) (1); the sludge is then routed to a still settling zone (2) where the sludge settles and returns to the sludge blanket (3); the treated water is collected by a weir that may or may not be submerged (4). Different techniques are available: in particular, to facilitate water-sludge separation, the parallel plate or honeycomb technique (cross-current or counter current) are offered. It should be noted that the inlets of the small settling tanks are the most delicate zone where the outgoing sludge and the ingoing water (to be clarified) cross.

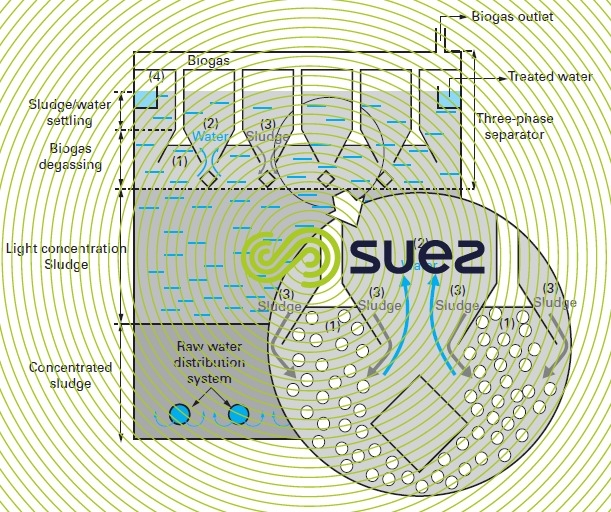

It should be noted that:
- the feed supply is often pulsed in order to ensure the even distribution of water over the entire reactor surface area, while using drilled pipes with orifices sufficiently large to avoid blockages;
- the bed is stirred by the pulsed feed supply and above all by the gas produced within the bed itself.
In order to be able to quickly increase the load to reach the rated speed, this equipment must be started with sufficient seeding; the formation of granules is a relatively long biological process.
Furthermore, in the case of low biogas production, stirring being low, the sludge-effluent contact is mediocre, which could imply apparently mediocre kinetics able to penalise the start-up and increase start-up time.
The reactor can be built of concrete or steel, adequately protected. It must be thermally insulated.

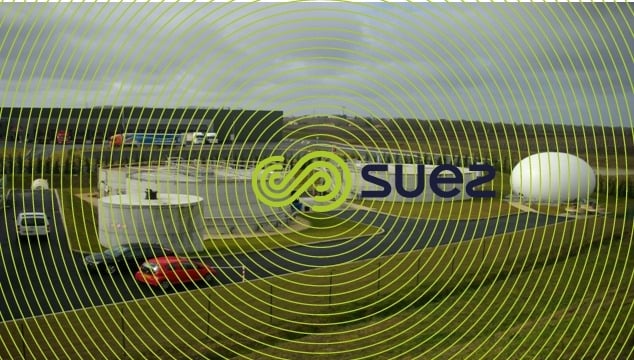

applications and performances
This process can be applied to dilute effluents (COD 1.5-10 g · L–1), easily degradable (breweries, soft drinks, sugar mills, starch plants, paper mills, yeast factory, etc.). It is generally not suitable for concentrated effluents containing readily settle able suspended solids (e.g. clay, calcium carbonate, fibres, etc.) as these solids can block the inlet devices or the three-phase separators and interfere with system hydraulics.
The COD loadings applied can vary from 6 to 15 kg · m–3 · d–1 according to the nature of the effluent. Given the short retention times (a few hours), preliminary acidification is often required. Depending on the nature of the effluent, the efficiency achieved can vary from 70 to 85% for COD and from 75 to 95% for BOD5.
Applications of this technique to the pre-treat UWWin warm countries using low salinity water (SO4= < 50 mg · L–1) have been considered. In these cases, it is possible to achieve 60 to 80% efficiency on BOD5 with a 6-8 hour contact time (temperature ³ 25°C) at minimum energy requirement. However, the discharge effluent, very septic and containing nitrogen in the form of NH4+, must undergo supplementary treatment either in a large polishing lagoon (~ 20 days) or in a Biofor C + N.
Bookmark tool
Click on the bookmark tool, highlight the last read paragraph to continue your reading later
