material properties
Reading time:The nature of granular materials used in water treatment is very diverse (sand, anthracite, expanded clay, activated carbon, limestone, resins …).
preparing the sample
For all granular materials, we need to remember that the sample collected must be representative of the product supplied. Similarly, the test outlet provided by the analyst must also be representative of the sample.
filtering matter granulometry
We must refer to the recommendations made in the French standard NF X 45.401 in order to perform granulometry analyses under the best possible conditions.
According to the NFISO 2591-1 standard, the amount of sample used must be appropriate to the screens used.
This material must be screened successively through NFISO 565 standardised screen (table 7) and the mass held back in each screen recorded.
From these results, calculate the mass of material that has passed through each screen (total material that is or is not held back by all screens having a mesh smaller than the one used) and express this mass as a percentage of the mass of material used for the analysis.
Plot the curve that represents these percentages according to the mesh size of each screen (figure 24).

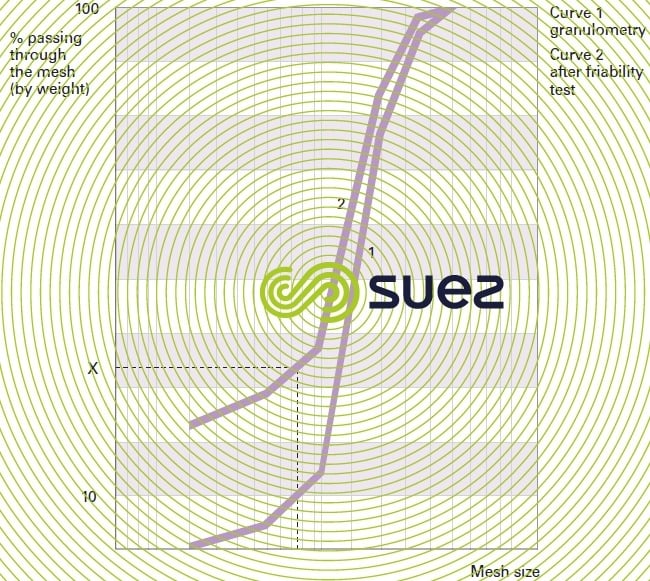

Use a logarithmic abscissa graph for this purpose.
effective size ( ES )
This is the size applicable to 10% of the mass that passes through the screen.
uniformity coefficient ( UC )
Read the size that applies to 60% of the weight passing through the screen off the graph.
The uniformity coefficient is the following ratio:


Comments. Table 7 shows the control screen equivalence between English and American standards.
In the case of materials that have very special forms, a kurtosis is often established.
Ideally, it would be below 1.5. However, coefficients of up to 1.8 are permissible depending on the material under consideration.

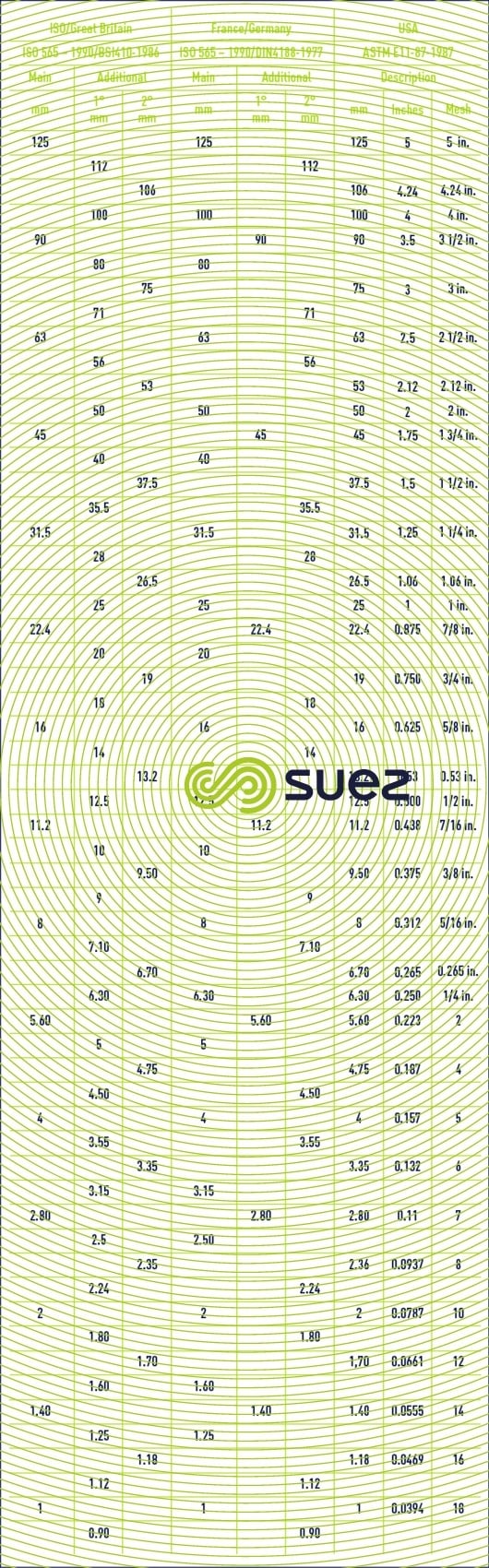

flakiness index
We need to refer to the recommendations published in the NF P 18-561 standard in order to carry out analyses under the best possible conditions (choice of apparatus, sample preparation, test procedure …).
The kurtosis determines the proportion of flat elements in the sample analysed; it is the weighted sum of the kurtoses applicable to the different categories of granules.
Therefore, we must first determine the categories of granules constituting the sample, i.e. we must undertake a granulometric analysis.
Each class of granules is then sieved by hand using parallel slot screens where the gap between the bars is established according to the category of granules (please refer to the equivalence table in the standard).
The kurtosis for each category of granule refers to the proportion of the sample that passes through the parallel slot screen; this proportion is expressed as a percentage:

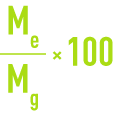
where
Mg = mass of each category of granules (en g),
Me = mass (in g) of the elements in each category of granules that passes through the parallel slot screen defined in the standard’s equivalence table.
Therefore, the sample’s kurtosis A will be:

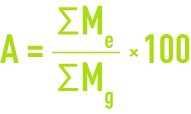
friability
A material's friability is evaluated by assessing the amount of material that is still usable after crushing, i.e. retaining the same effective size as the original sample.
operating method
It is compulsory for friability measurements to be carried out on the same 50 mL sample of filter material in the form of three successive measurements. With the first measurement, the granulometry of the material tested is established. Then, all the material is collected from each screen and placed in a metal cylinder having a 40 mm internal diameter and a 100 mm useful depth. This cylinder is mounted radially on a 34 cm diameter wheel. 10 x 12 mm Ø steel balls are also placed in the cylinder. This wheel rotates at 25 rpm round a central shaft. After 15 minutes of operation (i.e. 375 revolutions and, therefore, 750 strokes), the material’s granulometry curve can be plotted. All the material is then collected again and put back into the metal cylinder with the 18 steel balls. After a further 15 minutes (or a total of 750 revolutions and, therefore, 1 500 strokes), a new granulometry curve is plotted for the material.
calculating friability (figure 24)
After crushing, X represents the percentage of the material that has an effective size that is smaller than the initial «effective size»; the fraction measuring more will be equal to (100 - X)% and represents 90% of the material that remains usable after crushing.
Therefore, we can use:

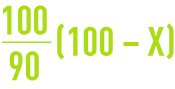
expressed as a %, the loss is:

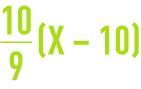
In this instance, this refers to sand that must be rejected if we take into consideration the figures in table 8 which provides the customary limits for the main materials.

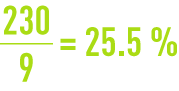
In this instance, this refers to sand that must be rejected if we take into consideration the figures in table 8 which provides the customary limits for the main materials.

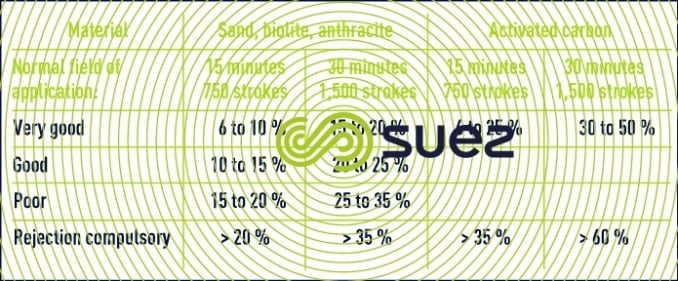

acid loss (see NF X 45.401)
This is the loss of weight after a 24-hour exposure to a 20 % solution of HCℓ. The acid loss for a sand should be less than 2 %.
density
When undertaking these measures, it is recommended to first check the calibration of the test tube graduations.
bulk density in air
Weigh out 100 g of material and pour it into a graduated test tube.
If V (mL) is the volume read from the test tube, the bulk density of the uncompressed material is as follows:

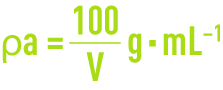
The material density can also be measured after compaction in a test tube (bulk density of the compacted material).
true density
- non porous material
Weigh 50 g of material and place in a 250 mL test tube containing 100 mL of water. If V (mL) is the volume read from the test tub, the true density is given by:

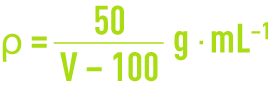
- porous material
Weigh 50 g of material and place in a 250 mL test tube filled with 100 mL of water. The test tube should have a threaded neck connected to a vacuum pump. Initiate a vacuum and maintain a negative pressure of 0.8 bar for 15 minutes.
After “breaking” the vacuum, if V (mL) is the volume read from the test tube, the true density is calculated as follows:

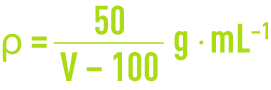
humidity
This measurement applies to both granular and powdered materials (e.g. PAC).
Precisely weight 50g of filter material (or 5g of powder material). P1 is this weight. Place the sample in an oven at 120°C for 4 hours. After allowing to cool in a desiccator, weigh the material again.
If P2 is the final weight, the percentage humidity H is expressed as follows:

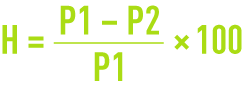
as a % of weight.
Bookmark tool
Click on the bookmark tool, highlight the last read paragraph to continue your reading later
