pilot tests
Reading time:Even when dealing with well-known and proven technologies, it is always recommended to conduct pilot testing (a small scale system, often only a few m3 · h–1, reproducing the process elements of a full-scale industrial application). One should proceed with pilot testing under the following scenarios:
- to demonstrate the performance of a technology for a specific water (local demonstration test);
- seeking optimum treatment performance by varying a few design parameters (velocity, contact time, loading…). This approach is valid when using representative amounts of reagents along with actual fluctuations of the water quality.
It is quite obvious that if the process at stage n is stretched the best quality water will not obtained at stages n + 1 or n + 2 and this will require compensation. Therefore, the target optimum cannot be cost-effective considering investment and operating costs and allowing for the safety margins that typically apply to a plant design that is required to operate for 10, 20 or even 40 years!
The advantages of this type of pilot study are as follows:
- incorporate the water actual variability according to season, rainfall, manufacturing, human activities (tourism…) resulting in test periods that can last as long as a year;
- highlight the treatment strain and the interactions of one stage with the subsequent stages (e.g. phosphorus concentration after a physical-chemical stage but before a biological stage, output surges caused by periodic filter washes…). In this case the impact of upstream processes should be simulated, which can lead to complex pilot studies (figure 27 provides a process diagram on a pilot unit that pretreats a difficult sea water prior to reverse osmosis);
- best define transient operating condition(s) such the impact of a temporary overload on the performance of a biological system that is usually fed based on average or low loading (e.g. ski-ing weekend in a tourist area…).
Note that the size of a pilot unit and therefore the flow capacity and operating duration can only be decided once the parameters that need to be studied have been clearly defined. For example problems with insufficient length of filtration cycles can be simulated on a 50 mm diameter filter column; however quality problems with the filter effluent can only be studied with a column having a diameter of at least 200 mm. Finally, studying problems related to the media washing cycles (velocity, duration of the various steps involved, amount of wash water) requires a filter column with an area of at least 2 m2. Returning to the pilot study illustrated in figure 27 it is required to have a flotation unit of at least 0.8 m2 to optimise the rise rate of a Rictor type flotation unit (20 to 30 m3 · h–1), whereas a much smaller 200 mm diameter column is sufficient for the downstream filter steps. With respect to the double-pass reverse osmosis the pilot system is provided with the required recycling capabilities enabling the simulation of:
- either the 1st pass and the 1st stage of the second pass;
- or the 1st pass and the 2nd stage of the second pass (see the different types of layout (desalination system)).
It should be noted that this type of pilot test requires the presence of one project supervisor and two or three assistants (excluding complex analysis). Such pilot system is designed to operate 24 hours a day, which implies the implementation of a reliable automation or the attendance of one or two individuals working in shifts.

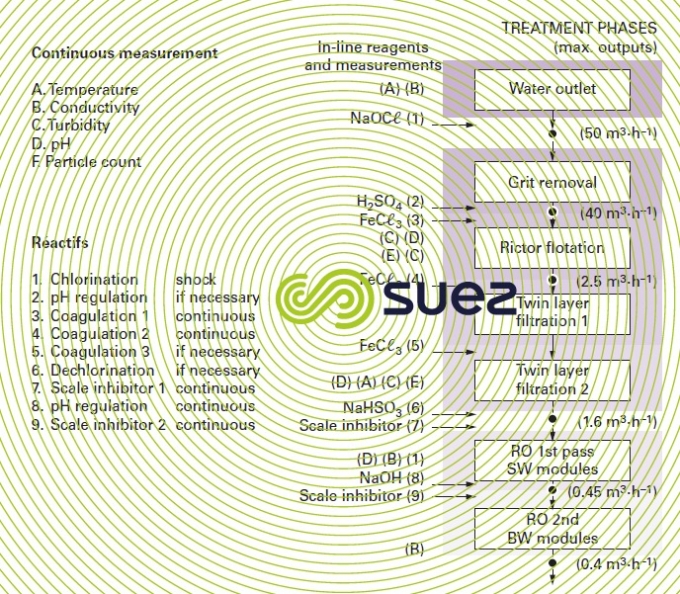

Bookmark tool
Click on the bookmark tool, highlight the last read paragraph to continue your reading later
