aeration systems
Reading time:effectiveness criteria and aeration system comparison
Aeration systems installed in an activated sludge tank have two purposes:
- providing aerobic micro-organisms with the oxygen they require, usually taken from the air;
- inducing sufficient mixing and homogenising to ensure thorough contact between the living medium, the polluting elements and the water that has been oxygenated in this way.
In the main, these systems comprise an appliance or a series of appliances set in a tank of a specific shape and capacity, performing both these functions at the same time.
In some cases, the aeration and mixing functions may be separate. Then, we have a dissociated aeration – mixing system where a mechanical mixer supplements the aerator to ensure that the tank contents are homogenous.
oxygenation capacity
To be more precise, a system’s oxygenation capacity should be established and verified under actual operating conditions, in the presence of activated sludge and with an incoming pollution flow. However, taking measurements under these conditions is a very delicate matter, especially because of the biological activity and of the representative nature of the measurement points. That is why a system’s efficiency is usually evaluated in terms of clean water (see EN 12255-15 standard). In this way, the margin for error is reduced by between ± 5 % and ± 10 % depending on tank configuration. Measurements are then compared against standard conditions, i.e.:
- in clean water;
- at a temperature of 20°C;
- at normal atmospheric pressure of 1013 mbar (pressure at zero altitude);
- with a constant 0 mg · L–1 dissolved oxygen content.
The most widely used measurement method is tank re-oxygenation. Oxygen is first removed from the clear water by an excess of sodium sulphite (Na2SO3) in the presence of cobalt (catalyst). The aeration system is then switched on and the oxygen concentration verified at regular intervals. .By operating with fixed rate aeration, the increase in O2 concentration obeys the following law (see pre-treatments).

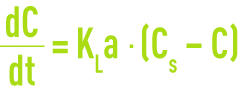
Where:
- C (mg · L–1): oxygen concentration;
- KLa (h-1): global transfer coefficient, characteristic of oxygen transfer from the gas (air) to the liquid (water) phase;
- Cs (mg · L–1): oxygen concentration in saturated water in test conditions
Several corrections have to be applied when transferring from test figures produced in clear water to those produced under standard conditions:

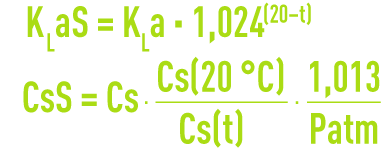
KLaS and CsS are the values for KLa and Cs under standard conditions.
Cs(20 °C) and Cs(T): values for oxygen saturation at an absolute pressure of 1 013 mbar, respectively at 20°C (Cs(20 °C) = 9.09 mg · L–1) and at the test water temperature (please refer to standard EN 25814).
Patm: atmospheric pressure under measurement conditions, in bar.
T = water temperature under measurement conditions expressed in °C.
Concentration measurements based on time are used to establish the overall coefficient KLa at t °C and then KLaS.
The Standard Oxygen Transfer Rate SOTR in kg · h–1 is an aerator’s main parameter. It establishes the amount of oxygen an aerator can provide to a liquid mass under standard conditions. This parameter can be deduced from measurements using the formula:


V in m3: liquid mass volume.
performance criteria
The standard aeration efficiency, SAE represents the quantity of oxygen transferred per unit of energy consumed:

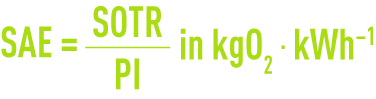
where PI = input of all aerator equipment under stabilised operating conditions expressed in kW (gross electricity output at the terminals of the motor(s)).
The SAE is particularly relevant when comparing aeration systems. It applies irrespective of the technology used and is directly linked to the aerator’s operating costs.
The standard oxygen transfer efficiency SOTE only applies to pressurised air systems. SOTE is the percentage oxygen mass actually dissolved compared to the oxygen mass injected into a pressurised air system. It can be calculated using an oxygen mass of 0.3 kg · Nm–3 of air:

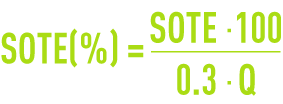
Q = the injected air flow expressed in Nm3 · h–1 (TPN condition, 0°C air temperature and 1
013 mbar atmospheric pressure).
For practical purposes, the frequent use of specific standard oxygen transfer efficiency SSOTE expressed in %· m–1, should be noted; this practice consists in comparing a diffuser’s efficiency against its submersion depth.
The aerator/tank pair is inseparable and any aeration system performance must include a comprehensive definition of this pair. In effect, it is well-known, for instance, that oxygenation performance can be enhanced under exceptional conditions: high specific output (per m³ of tank) for surface aerators, or multi-staged centrifugal turbo blowersor low air output per diffuser for fine bubble systems.
aerator comparison – transition from standard conditions to actual conditions
An aerator comparison carried out using clear water will not be representative of performances recorded under true operating conditions. In effect, oxygen transfer can be significantly affected by the nature of the wastewater, sludge quality, hydraulic and biological operating conditions.
Under normal operating conditions, it is customary to use a correction coefficient T that is applied to the criteria described above.
In general, all magnitudes measured or evaluated under true operating conditions are shown with an « ' ». In order to transfer from nominal conditions to actual operating conditions, we have to apply a correction coefficient T which is itself the product of three secondary coefficients Tp, Td, Tt. Thus:


Tp : pure water-liquor equivalence coefficient
Often denoted a in English language literature, this coefficient depends on the nature of the water and, more particularly, on its surfactant, grease, suspended solids content, i.e. the type of treatment, and on the aeration system used.

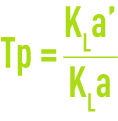
Td : oxygen deficit coefficient
It compares the oxygen deficit between real operating conditions and standard conditions.
The oxygen input is proportional to the oxygen deficit Cs' – Cx.
Cs': oxygen saturation under actual operating conditions influenced by:
- water salinity;
- temperature (see table 36 in characteristic constants of gases);
- atmospheric pressure.
Cx: oxygen content of the liquor, most frequently between 0.5 and 2 mg · L–1

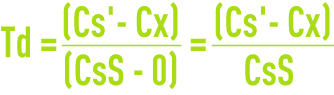
This simplified expression in fact uses the for the real conditions prevailing in the tank, conditions that are linked to water depth. In a perfectly agitated system, the saturation concentration is found to be higher than the figure quoted in the table and quoted at atmospheric pressure, and this results in adding a coefficient KH that depends on the water head:


where:
Patm: site atmospheric pressure (expressed in m H2O);
g: gravity acceleration;
H: diffuser immersion depth (m).
Under standard conditions, Cs is equal to 9.09 mg · L–1 and Cx is zero, therefore Td = 1.
Tt : transfer velocity coefficient
As the temperature rises, the gas liquid transfer velocity increases. The correction will be equal to Tt = 1.024T–20 where T is expressed in °C.
It should be noted that although coefficients Td and Tt are independent of the aeration system, this is far from being the case for the exchange coefficient Tp. Therefore, the performances of the various aeration devices will not vary in the same way when we transfer from standard to actual operating conditions. The precise definition of Tp requires delicate measurements, preferably carried out in a sufficiently large biological purification pilot unit supplied with the wastewater subject of the analysis.
Coefficient Tp is noticeably lower when air is diffused as «fine bubbles» than in systems where air is diffused as «coarse bubbles» or when surface aeration is carried out.
The above method for transferring from standard to actual operating conditions is perfectly acceptable providing that oxygen transfer efficiency is not too high (approximately 5 to 6 % · m–1) and that we have moderate water depths, usually 4-8 m. SUEZ uses a suitable computerised program that has been developed from a very significant number of oxygen test modelling.
comparison criteria
The first aerator comparison criterion is clearly based on aerator oxygenation performance in terms of hourly input or gross specific input.
However, it is advisable to include other criteria into the comparison, criteria that are difficult to quantify and can only be evaluated qualitatively:
- mixing, that needs to provide good homogenising and prevent the formation of deposits;
- flexibility of the specific input under different operating conditions;
- reliability of all units such as the reduction gear, blower, diffuser, pipeline…
For instance, it is pointless having an aerator with excellent oxygenation performances if this is to the detriment of proper hydraulic mixing or if it creates fouling, resulting in a drop in oxygenation capability or the formation of anaerobic deposits in the tank.
pressurised air aeration
Pressurised air aeration consists in injecting air into the liquid mass at depths varying from 1 m to 15 m or more, depending on the type of devices used.
The devices used are divided into three major groups, according to the size of bubble produced:
- coarse bubbles (Ø > 3 cm): vertical pipes, wide opening diffusers;
- medium bubbles (Ø 5 mm to 3 cm): there are many diffusers that will reduce the size of the bubbles delivered; valves, small openings …;
- fine bubbles (Ø < 5 mm): air is diffused through a porous medium or through finely perforated elastic membranes.
The comparative figures given below constitute the ranges usually encountered in plant under typical operating conditions.
oxygen transfer efficiency
The oxygen transfer efficiency in clean water for a given system varies according to the depth at which air is injected. The increased depth extends air bubble contact time and, consequently, transfer efficiency. Within the 3 to 8 m depth range, efficiency will be virtually proportional to depth however be careful with very high water levels as performance can be low. This allows us to establish an efficiency per metre of submersion. Depending on the mechanism used, this efficiency will vary as follows:
- Medium-coarse bubbles: 2 to 43.5 % · m–1;
- fine bubbles: 5 to 7 %·m–1;
These significant differences in clear water lessen under actual operating conditions (in fact, the Tp coefficient is lower for fine bubbles):
- coarse and medium bubbles: Tp varies from 0.95 to 0.8 (UWW);
- fine bubbles: Tp varies from 0.75 to 0.5 (UWW).
However, the final energy saving produced by fine bubbles is noticeable and usually justifies their use, despite higher installation costs.
The oxygen transfer efficiency for a given system is affected by a number of other factors:
- specific output. This trend is reversed for surface aerators. Power increase is mainly caused by an increased flow rate. However, a greater air flow rate will not only induce larger bubbles but also the possibility of greater bubble coalescence and, therefore, reduced efficiency;
- the hydraulics induced by diffuser layout (see also mixing). Oxygen transfer efficiency is optimised in a floor layout as the result of very good bubble distribution throughout the liquid mass and a maximum contact time (figure 1). The in-line arrangement or spiral flow with zones which do not have aerators, causes significant vertical convection movement of the water leading to a drop in oxygen transfer efficiency of approximately 25% because of the water’s rotating motion;
- tank cross section. In particular, trapezoid section ditches tend to be less efficient overall than their rectangular section alternatives.
stirring
In general, the greater the water depth, the more efficient the pressurised air mixing system. The entire mass will be properly homogenised because the entire liquid depth is involved.
- Floor layout (figure 1): this arrangement provides for efficient mixing because the aerator minimum flow rate/density couple is kept within acceptable limits. When this condition prevails, there is no danger of any deposits forming.
- In-line arrangement or spiral flow (figure 1 and photo 6): this arrangement is particularly effective because it uses the air lift effect to cause the entire liquid mass to rotate. The tank floor is subject to high sweeping velocities. This arrangement ensures satisfactory mixing for a reduced amount of air providing the liquid depth/distance to the top level of sludge remains within the 0.5 to 1.5 range.
- Aeration-mixing dissociation: in alternating aeration systems, the agitatorsare required to maintain mixed liquor in suspension during aeration shutdown period. The best agitators are slow, large diameter agitators. These devices are often included in oblong or circular closed loop tanks in order to reduce head losses. Thus, a 30 cm · s–1 minimum circulation velocity can be achieved with just 1.5 to 5 W · m–3 depending on tank sizes and geometry.

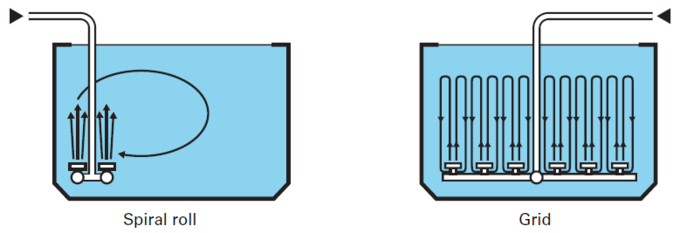
For activated sludge from UWW and depending on whether or not primary sedimentation is used, the requisite mixing power is provided for minimum aeration rates ranging from 2 to 6 Nm3 · h–1 of air per m² of tank liquid surface area, depending on water depth and diffuser density.
flexible membrane fine bubble diffuser
In this diffuser which can be tubular (photo 2) or disc (photo 3) shaped, air in the form of fine bubbles is diffused through a thin, deformable elastic membrane perforated by many slots. These slots open under the effect of air pressure but close as soon as that pressure disappears, preventing any sludge from flowing back into the diffuser and the system. This essential aspect makes this aerator ideal for dissociated aeration-mixing systems. The original perforation system produces a good oxygen transfer efficiency of 20 to 25% under 4 m of water and under standard conditions; this efficiency can rise above 30% at low flow rates.

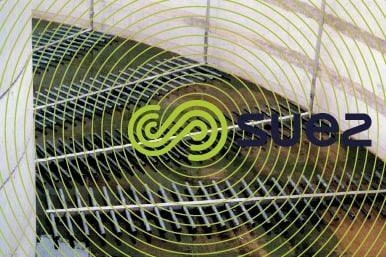


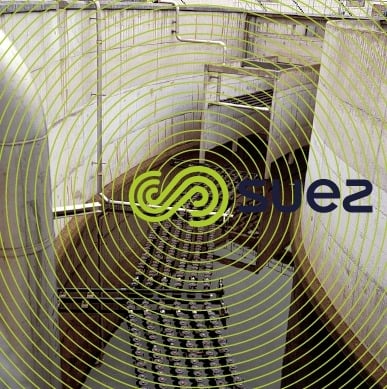

Their SAE range from 2.5 to 4 kgO2 · kWh–1 in clear water and their AAE from approximately 1.6 to 2.4 kgO2 · kWh–1 under true operating conditions.
The Flexazurs are mounted on floor networks that are designed to be fixed or to be raised, constructed of plastics or stainless steel. They can be installed in tanks up to 11 m deep. Depending on their utilisation, their classic service life is between 6 and 10 years.
The following constitute the main advantages of flexible membrane, fine bubble diffuser:
- excellent oxygen transfer efficiency;
- aeration can be shut down without the need for any special precautions;
- diffusers maintenance without the need to shut down the aeration tank if retractable ramps are fitted ;
- support structures constructed of corrosion-proof materials;
- diffuser, or even the membrane alone, easily replaceable.
Before these diffusers became available, porous or ceramic type discs were used especially for continued aeration. If machines had to be shut down, sludge clogged up this type of diffuser making it unfit for use in intermittent operations.
Vibrair diffuser

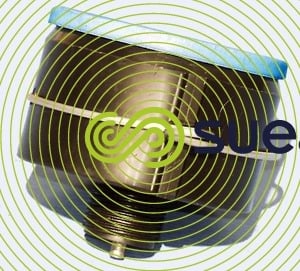

Vibrairs are medium bubble diffusers, designed for difficult service conditions: sludge containing large amounts of fibrers, hydrocarbons, grease … that would rapidly foul fine bubble aerators.
The Vibrair (photo 4) has a moulded polyethylene casing supporting a vibrating valve. Because it moves unceasingly, the valve does not become blocked. This original mechanism produces a low air flow and, therefore, many air injection points into the liquid mass, encouraging oxygen transfer and mixing.
The Vibrair is installed on a floor mounted network as illustrated by photo 5.

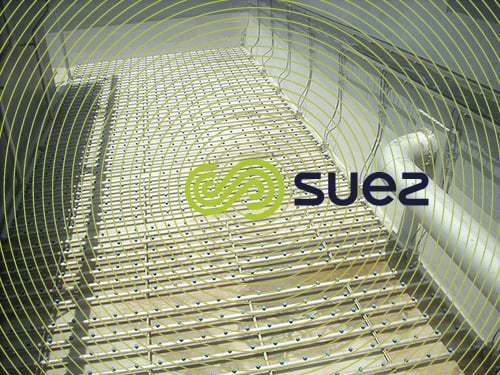

The unit flow rates are 2 to 10 Nm3 · h–1, with a head loss of approximately 20 mbar.
Vibrair oxygen transfer efficiency is 2 to 3.6%%.m-1 for an SAE of 1.6 to 2.1 kgO2 · kWh–1 and an AAE of 1.4 to 1.7 kgO2 · kWh–1 in sludge.
Despite having a lower efficiency than fine bubble aerators, the Vibrair does have certain advantages over the former:
- head loss does not change;
- sturdy, it provides many years of service (> 10 years);
- used in industrial wastewater treatment: aeration tank but also air-mixed buffer tank …
Oxazur diffuseur

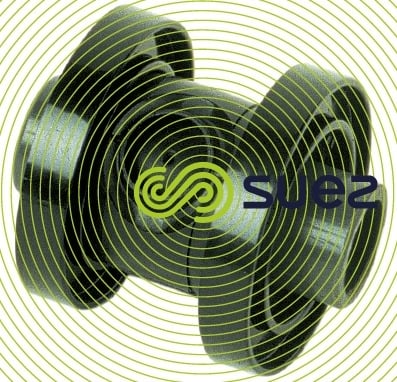

Oxazurs are medium bubble air diffusers, particularly suited to floor layouts and developed for reactors with attached growth on granular beds (photo 6).
Air is diffused through an opening that has a diameter of approximately 1 mm. This opening is pierced through a moulded elastic membrane made of a special elastomer and housed in a polypropylene casing. This membrane will distort and its diameter can be multiplied by 2 under the effect of a water current, thus making it possible to check at regular intervals that the blowing opening is not fouled by a bacterial film.
The air flow per diffuser is approximately 1 to 2 Nm3 · h–1, with a head loss of approximately 50 mbar. When there is very good air distribution through the granular matter, an Oxazur system will have a 15 to 25% nominal oxygen transfer efficiency at a 4 m submerged depth.
Bookmark tool
Click on the bookmark tool, highlight the last read paragraph to continue your reading later
