high pressure condensates
Reading time:treatment
The definition of condensate treatment depends on :
- condensate quality;
- standards imposed by constructors;
- operator requirements.
There are several possible solutions; they combine filtration and demineralisation. Therefore, their main components are: filters, ion exchangers, either alone or in combination.
Comment: in some cases, ion exchangers can be replaced to good advantage by electro-deionization.
filtration through disposable cartridges or backwashable components
These filters screen out suspended impurities, in particular metal oxides that are larger than the filter’s nominal filtration threshold, usually by a few micrometers (5 to 20).
demineralisation at very high filtration rates (8-120 m·h–1) direct through a cation-anion mixed bed (photo 3)
The mixed bed is not protected by upstream treatment units and must alone eliminate the various pollutants, i.e. not only dissolved salts (accidental penetration of raw water into the condenser) but also suspended solids (corrosion products, mainly iron oxides, or even Cu, Ni, Zn, metal cation) and, occasionally, very slight traces of hydrocarbons. Their efficiency varies: 50 to 90% depending on particle size and on operating conditions.
Ion exchangers must be particularly robust if they are to withstand head losses generated by both high velocities and fouling: macroporous resins and «tough gels» are the most widely used (see chapter fundamental physical-chemical engineering processes applicable to water treatment).

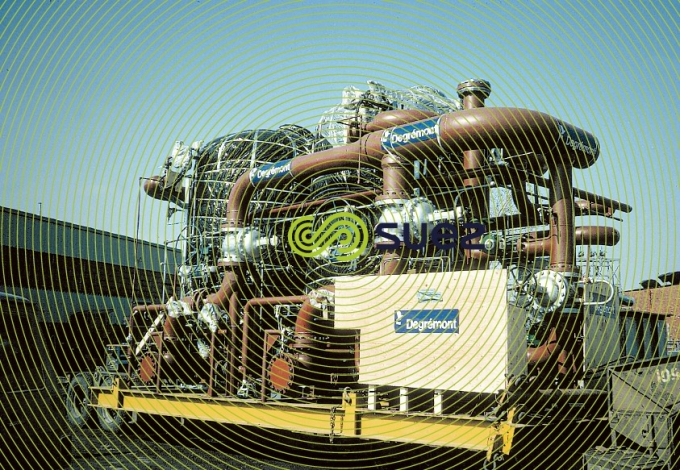

In most cases, these resins are washed and regenerated in a system that is external to the treatment columns; resin is transferred by being carried away in water (figure 7). This prevents any possibility of accidental penetration of acid or sodium hydroxide into the boiler during regeneration.

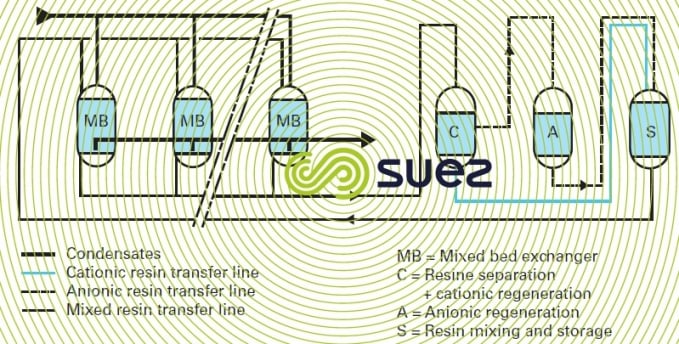

Constructors of pressurized water nuclear reactors impose very stringent requirements in terms of sodium levels in circuit water (e.g. Na < 0.2 ppb). When the cationic and anionic resins in a mixed bed are not completely separated before regeneration, the cations that are «trapped» in the anionic resin (separation is never perfect) will go through as Na during regeneration and release this ion during the mixed bed’s working cycle, thus preventing target qualities from being achieved.
Salinity being very low, the cycles are very long. Secondary pollution, even at minimum levels, will accumulate in sufficient quantities without affecting resin grading after transfer into the external regeneration column.
Consequently, processes have been submitted either for reducing ionic leaks caused by «cross-contamination» (poorly regenerated resins as the result of poor separation before regeneration) or for enhancing their separation. These processes make use of :
- large quantities of additional reagents (ammonia, lime-Calex process, sodium hydroxide); numerous and relatively complex resin transfers;
- the triobed system with an inert resin separating cationic and anionic resins during the regeneration phase .. this being the process normally used by SUEZ (photo 4).

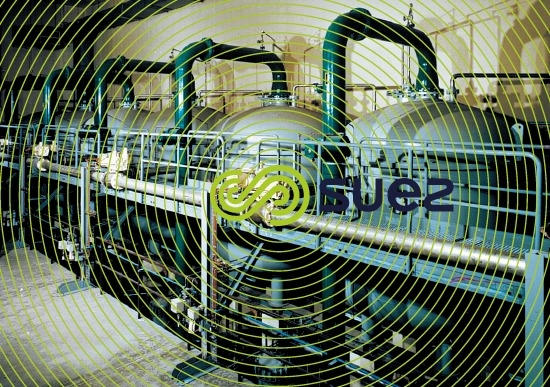

very high speed demineralization comprising a cation exchanger followed by a mixed bed
When condensed water is conditioned using large quantities of volatile cations (ammonia, morpholine or cyclohexylamine) and incoming salinity caused by raw water leaks is negligible, the mixed bed will become unbalanced. In effect, many more cations have to be screened out than anions other than OH–.
It can then be advantageous to place an ion exchanger in front of the mixer bed to eliminate NH4+ ions or amines and to considerably extend the operating cycle. The cation exchanger simultaneously applies a filtering effect on corrosion products, suspended solids and, if applicable, any traces of oil thus ensuring that the mixed bed only operates in demineralization mode and, therefore, with very long cycles.
In order to reduce the investment and overall dimensions generated by this scheme, SUEZ has included a mixed bed topped with a CF layer within the treatment column (figure 8).

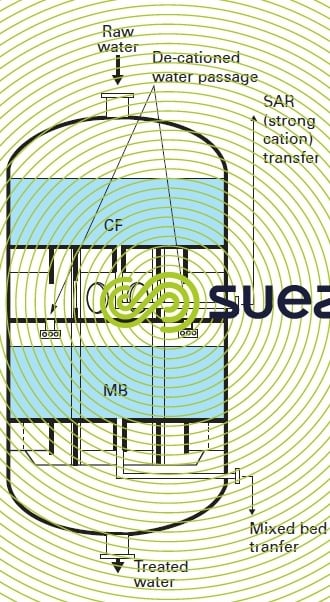

filtration and demineralisation combined in one single appliance by using micro-resins on precoat filters
Representing less of an investment, this device satisfactorily resolves fine filtration and demineralization requirements but is very expensive to run because of the cost of powdered resins and, therefore, is often replaced although it have not been extensively used.
conditioning
Chemical conditioning of HP condensates can be carried out using ammonia, morpholine or cyclohexylamine.
Bookmark tool
Click on the bookmark tool, highlight the last read paragraph to continue your reading later
