manganese removal
Reading time:natural states
Manganese is an element that is often found in the ground. Many manganese ores can be found, mainly oxides (pyrolusite, vernadite, etc.) and occasionally carbonates (rhodochrosite), silicates, sulphides, etc.
In natural water, manganese will usually be present in the soluble ionised form, Mn2+, and sometimes as MnOH+ (very basic pH). It can form compounds with the bicarbonates, sulphates and silicates present at the same time and also with some types of OM (humic and fulvic acids). Manganese will often be present in natural water in combination with iron and ammonium. However, there are cases where the manganese is present on its own.
physical-chemical removal of manganese
Figure 30 provides a stability diagram for the most common forms of manganese.

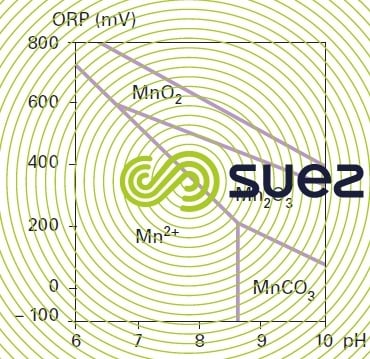

oxidation using oxygen
Manganese Mn2+ is very slowly oxidised by oxygen to form MnO2 according to the following kinetics:

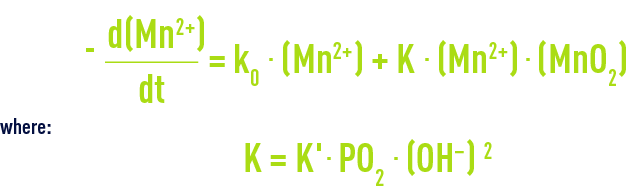
Oxidation using oxygen only reaches an appreciable rate when the pH rises above 9.5 (figure 31). Mn2+ oxidation using oxygen depends on temperature: oxidation will be 5 times faster when the temperature rises from 11°C to 22°C; however, at normal pH levels, contact times are not easily compatible with industrial operation.
The presence of manganese dioxide "catalyses" the reaction. This has been recorded in the case of some plants operating at a high pH where, after a certain time operating with other oxidants, sand is coated with a MnO2 deposit. However, this effect will not be enough to produce treated water that is completely manganese-freee.

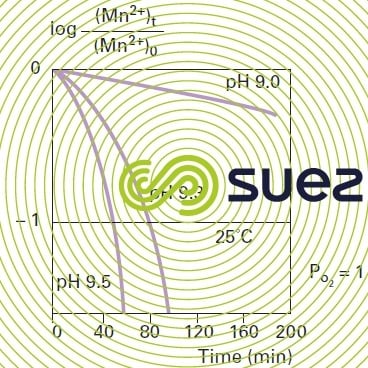

oxidation using MnO2
It has also been found that, at lower pH, MnO2 ceases to act as a catalyst but becomes an oxidant according to the following reaction :


In such cases, the MnO2 needs to be regenerated at regular intervals using permanganate :


The overall balance for reactions (1) and (2) will be :


In practice, instead of ‘manganising’ sand, it is advisable to use a filtering medium made up of MnO2("green manganised sand", "polarite "…) that can be mixed in greater or lesser amounts with the sand and which will also require regeneration at regular intervals.
oxidation using chlorine
Chlorine does not provide better oxidation of manganese than oxygen at a pH < 9.5; however, these same filtration mixes can be used (pH ≥ 8) as catalysts when oxidising Mn2+ using chlorine, occasionally after sedimentation and an initial filtration in an acid medium for the purpose of removing OM (case of some soft and coloured surface water).
oxidation using chlorine dioxide
As already reviewed in the section oxidation and reduction, this is a relatively slow reaction and, in the presence of OM, produces chlorites; therefore, it is not recommended.
oxidation using potassium permanganate
Oxidation-reduction occurs between manganous manganese and permanganate according to reaction (3) above.
Therefore, it will be seen that KMnO4 consumption remains the same as when MnO2 oxidation regenerated by KMnO4 is included as an interim step; the advantage of the latter method is that it provides a "regulator" in cases where the Mn2+ concentration fluctuates, enabling us to dispense a constant amount of KMnO4 set to an average level ("continuous regeneration").
The theoretical proportion is 1.9 g of KmnO4 to 1 g of Mn. However, in practice, the amount of potassium permanganate used depends on water pH and composition. In effect, a proportion of the permanganate is involved in the oxidation of some reducing OM present in water. Additionally the amount injected must be very carefully controlled: any excess of KMnO4 will tint water pink, turning to yellow in the mains distribution system.
If the manganese is not complexed, optimum pH will be in the region of 7.2-7.3 for a contact time of less than 5 minutes. When the manganese is complexed with OM, the reaction time can be as long as 20 minutes. In such cases, pH can be adjusted higher than 8.5 in order to accelerate the reaction.
In actual fact, KmnO4 is the most widely used reagent in physical-chemical manganese removal. In groundwater applications, plant design will be the same as for simple iron removal (figures 22 and 23); whether the water contains manganese only or manganese and iron, the first step will be an aeration (gravity or pressurised) which is always essential to have an effect on easily oxidised substances (Fe2+ , H2S…) and to enrich the water with dissolved O2 (protecting the mains against corrosion and unpleasant odours); permanganate will then be injected, as in the case of any other reagent used, between aeration and filtration (the latter occurring at the same velocities, but using finer sand if the water only contains manganese: ES = 0.55 to 0.75 mm).
In soft, coloured surface water applications that contain high amounts of OM and that require total clarification using coagulation-flocculation and sedimentation (water from granite areas of primary massives, for instance), the relevant treatment system can be designed on the basis of the scheme shown in figure 32, constituting an alternative to the system referred to earlier using chlorine and a "manganised" filtration medium.

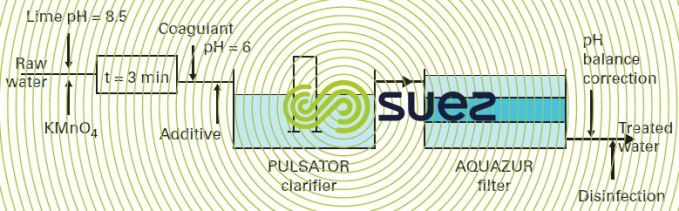

oxidation using ozone
Oxidising the manganous ion Mn2+ using ozone is a fast method. The following reaction applies:


to oxidise 1 g of Mn2+,0.9 g of ozone is required . The amount of ozone injected must be such that only Mn2+ is oxidised to produce MnO2 without leaving any excess (pink coloration, etc.), see section oxidation and disinfection using ozone).
The Jonchay DWTP (France) is based on this principle (figure 33).

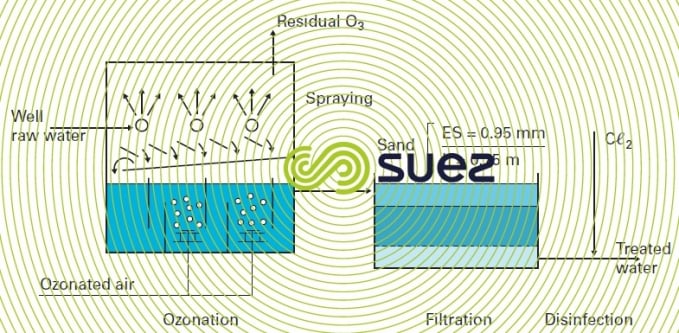

When manganese is complexed with OM and requires comprehensive clarification using coagulation-flocculation-sedimentation, ozone cannot be used as a pre-oxidising reagent for oxidising manganese. In effect, ozone will only oxidise manganese after having destroyed the organo-manganous compound, resulting on the one hand in excessive and not very cost-effective ozone consumption and, on the other, in colloid stabilisation (and therefore problematic coagulation and flocculation). In this case, there are two ways in which manganese can be removed: either using KmnO4 before sedimentation as detailed in figure 32, or by ozonation of the settled water, with the MnO2 precipitate formed being screened out by the filters.
biological removal of manganese – the Mangazur process
principle
As in the case of iron, many bacteria (see section iron and manganese cycle) to biologically oxidise manganese in an aerobic environment.
With some bacteria, oxidation of the Mn2+ will occur indirectly: this oxidation is caused by an increased pH linked to the growth of these bacteria, ensuring that Mn2+ will be oxidised by the oxygen at an appreciable rate. For other bacteria, oxidation is caused by the action of an intracellular enzyme. Finally, for others, dissolved manganese will begin to be adsorbed on the surface of the cell membrane. It will then be oxidised via enzymes. The manganese will then be concentrated in a sheath that surrounds the cell or group of cells.
In order to grow, these bacteria require a relatively basic environement (pH > 7.5), where the EH must be higher than 400 mV (equivalent to water close to dissolved O2 saturation); please refer to figure 28 and biological manganese removal domain (2). On the other hand, should the redox potential decrease significantly, some of these bacteria will solubilise (MnO2, Mn2+ passage) the manganese that they had previously accumulated.
Similarly, in the presence of easily assimilated OM, bacteria bound with carbon can compete for dissolved oxygen consumption with those bound with Mn; this may result in a drop on EH and a release of Mn2+, for instance during shutdown periods.
advantages of biological manganese removal
reagents
No reagents required under normal operating conditions. However, it may be advisable to use an oxidant, usually potassium permanganate, when starting up.
aeration
Contact time will be brief with most types of water. This is the time required to raise the redox potential. Aeration can be undertaken in-line (pressurised) or by cascade (gravity).
filtration rate
As in the case of biological iron removal, the solid nature of the biological floc allows for the use of high filtration rates which can, in some cases, reach 30-40 m · h–1, through filtering media of a higher effective size (ES = 1.35 mm) than those used for physical-chemical manganese removal.
retention capacity
Retention capacity is 5 to 10 times higher than in physical-chemical treatment operations.
backwash
The backwash can be carried out using raw water (or non-chlorinated treated water).
sludge
Sludge is easily thickened and dewatered.
utilisation
The process and the biological reactor-filter in which it takes place are both called Mangazur. The pressurised plant is the most frequently adopted solution (except in high throughput cases) as in the case of Sorgues (Rhône-Ventoux, France, water board) described by figure 34.

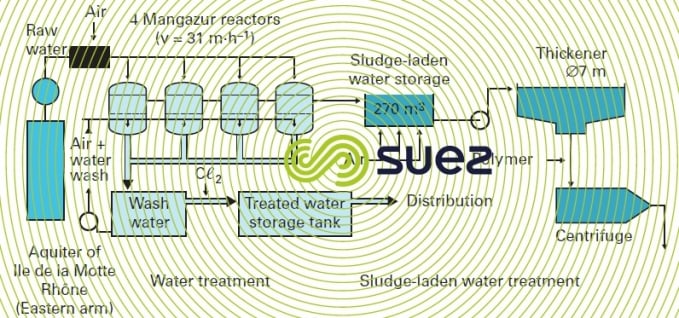

Another example, constructed in Canada, is shown in photo 20.

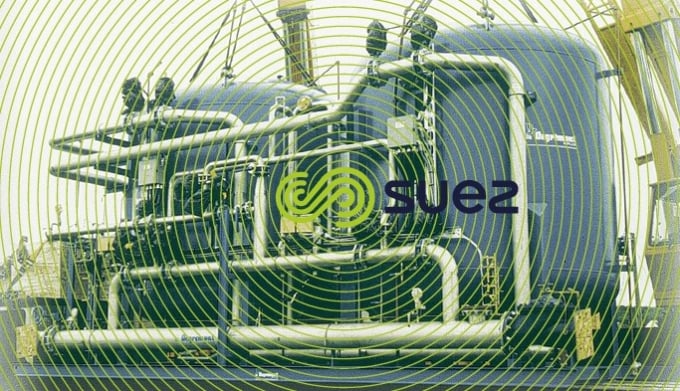

Bacteria involved in biological manganese removal grow far more slowly than iron oxidising bacteria. Therefore, the plant takes far longer to start up and may require 1 to 3 months of natural seeding (in fact, that is why the feasibility of this type of process was noticed late when analysing existing plant operation).
This period can be shortened by using sand that has been previously colonised by bacteria from a similar plant.
water containing iron and manganese
When water contains both iron and manganese, there is a need to satisfy different Redox potential conditions in order to oxidise both of these elements biologically (figure 28). Additionally, manganese removal can only commence when the iron has been completely removed. In very rare cases, these elements can be seen to be removed simultaneously by the same filter but only when the raw water properties are very favourable and in exchange for a restricted velocity; this applies to the Poncey gravity plant near Dijon, France (photo 21) that processes a nominal flow rate of 3,000 m3·h–1 using controlled aeration and filtration over a single, six sand filter stage, at an average rate of 15 m · h–1 and a peak rate of 19 m · h–1, based on the following raw water properties:
- Iron = 0.2 to 1 mg · L–1;
- Manganese = 0.2 to 0.5 mg · L–1;
- pH = 7 to 7.2;
- NH4 =Traces amounts to 0.1 mg · L–1.

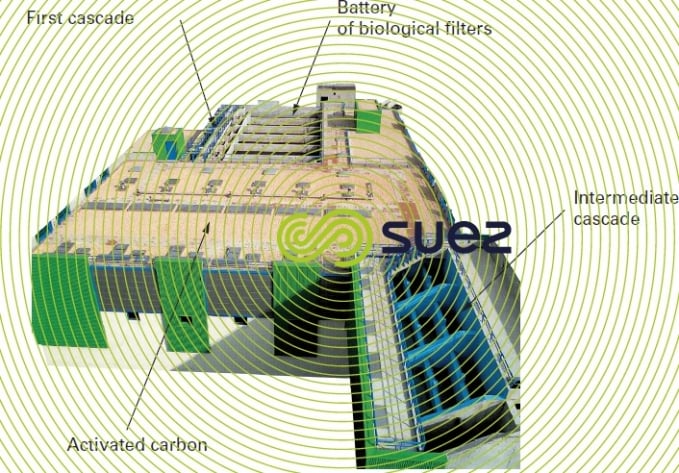

This solution could only be implemented after an extended trial campaign on a pilot plant (over 6 months). In most other cases, the following scheme is applied, based on two successive filtration stages:
- first aeration stage, set for biological iron removal;
- first filtration stage (biological iron removal);
- second aeration stage and/or raising of the pH (depending on the raw water properties and first stage settings);
- second filtration stage (biological manganese removal).
Depending on local conditions, the plant may comprise:
- two pressurised stages (please refer to photo 21 for an example);
- two gravity stages (large plants), vertically offset to allow the water to flow from the first to the second stage;
- a combined solution like the one for the Mommenhein (France) plant, outlined in figure 35: biological iron removal is carried out under pressure whereas biological manganese removal takes place by gravity: permanganate was injected into the cascade when the plant started up during the seeding process; seeding then occured very quickly, allowing the second stage filtration cycles to be extended from an average of 24 hours (during operation in physicalchemical mode) to 1-2 weeks (operation in biological mode).
Despite the frequent need to resort to 2-stage filtration when water contains both Fe and Mn, the biological solution is, generally, more cost-effective than the physical-chemical alternative and always easier to use. On the other hand, although biological iron removal has been thoroughly mastered (a good analysis will result in a secure project), because of the high pH and especially the EH requirements, biological manganese removal is subject to interference (NH4, H2S, OM, low pHS water…): consequently, it is often advisable to carry out preliminary pilot trials.

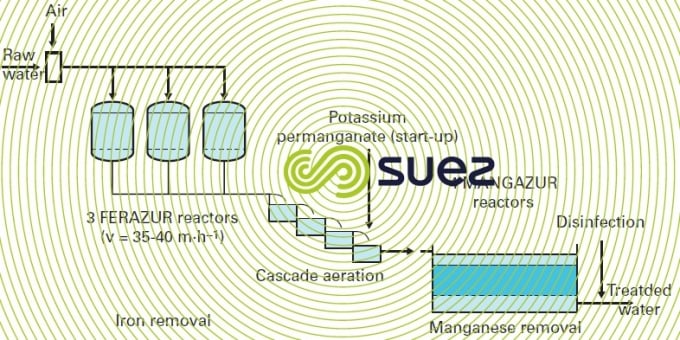


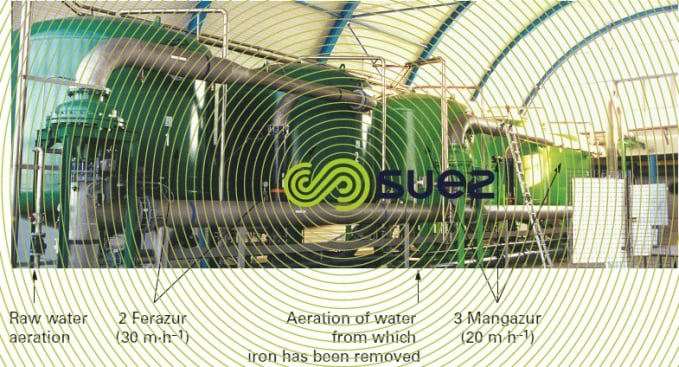

Bookmark tool
Click on the bookmark tool, highlight the last read paragraph to continue your reading later
