membrane processes
Reading time:The use of ultrafiltration membranes for the clarification of karstic water (see section clarification) has already been mentioned.
However, in order to satisfy increasingly stringent quality requirements, the water specialists will naturally utilise these membranes in more complex system designs.
nanofiltration
As already stated (see section membrane separation), reverse osmosis membranes, including their nanofiltration variant, are alone capable of eliminating all pollutants that might be present in surface water; consequently, they can be regarded as the water specialist’s “ultimate weapon” in terms of drinking water production.
Historically, these treatment processes were used for low mineralization water that is extremely heavily coloured. E.g; Eupen and La gileppe 110 000 m3/f in Beligum.

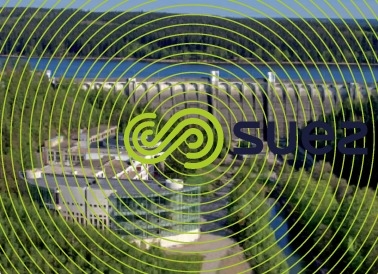

the cristal process
In this process (figure 12), the two techniques described above are combined, i.e:
- fixing dissolved contaminants on an insoluble adsorbent (PAC, resins);
- filtration through ultrafiltration membranes.
The ultrafiltration loop can be used as an adsorption reactor and the membrane to screen out the suspended solids present in the raw water, the adsorbant that has fixed the dissolved pollutants, and all unwanted germs: cysts, bacteria, viruses, thus enabling the water treated in this way to be distributed with a minimum of residual disinfectant.

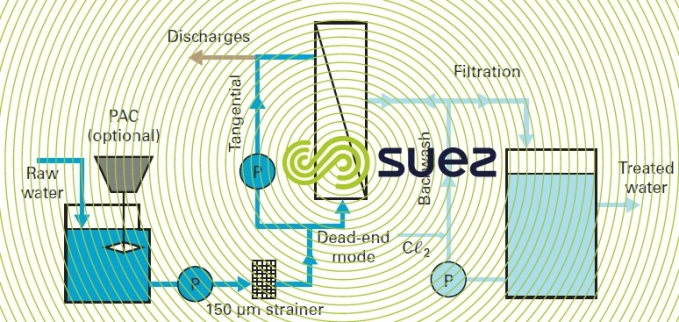

Among this type of plant, we can quote the following examples can be referenced:
- Koper (Slovenia): 34,500 m3·d–1;
- l’Apié (Cannes, France): 28,000 m3·d–1.
- Lausanne (Switzerland)(photo 11): this plant processes water from the Leman lake and was constructed in 1996 for treating 43,200 m3·d–1. Then, in view of the results achieved, a second phase was put in place in 2002 enabling the plant to produce a total of 70,000 m3·d–1 (the plant is only run with PAC in the event of accidental pollution).

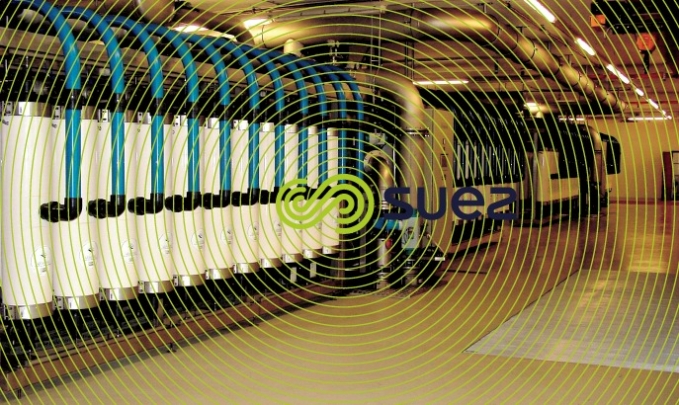

the extended cristal process
When intending to treat fairly contaminated surface water, it has been noted that adsorption treatments in particular, are subject to competition phenomena (see section polishing: removal of organic matter and micro-pollutants) that called for the inclusion of specific reactors.
This also applies to the use of the Cristal system; the PAC injected upstream of ultrafiltration must be used exclusively for fixing the final traces of micro-pollutants after most of the suspended solids or OM in solution have already been eliminated. Consequently, there exists a number of systems that range from the mere inclusion of a settling tank upstream from the membranes when the raw water is likely to have suspended solids peaks (e.g. Rivière Capot, Martinique, figure 13) to more complex plants such as Flers, Avranches, Vigneux or Angers (France) (see illustrations further on) where the range of raw water sources and the variable nature of the dissolved contamination they contain require the use of conventional clarification treatments followed by a final ultrafiltration stage. We then have what we call the "ExtendedCristal" process (fig. 14) that usually includes:
- a sludge blanket clarifier;
- a sand filter;
- a PAC contact reactor;
- an Ultrafiltration UF stage;
- theUFbackwash water is returned to the clarifier.
The characteristics of each stage together with the reagents used and operating conditions (pH, contact time) required are established on the basis of the assigned treatment objective, i.e :
- removal of suspended solids from the raw water ↔ clarifier;
- removal of humic acids ↔ coagulation under acid pH conditions and sludge contact;
- removal of residual dissolved contaminants ↔ specific adsorbant:
- adsorbant separation, final clarification and disinfection ↔ UF membrane.

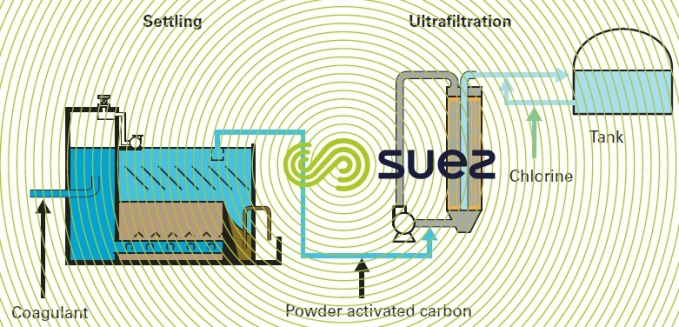


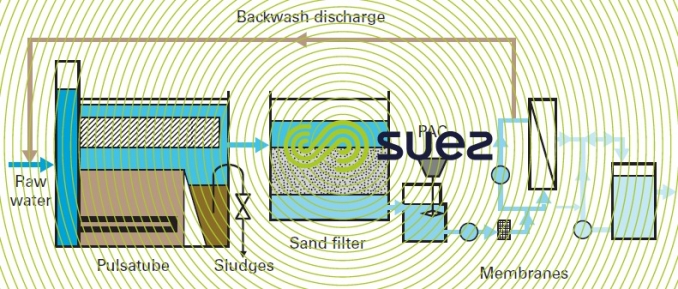

Another advantage inherent in the extended Cristal process is the fact that membrane backwash water containing PAC is recycled to the head of the main clarifier. In effect, activated carbon, that is not completely saturated upon its contact with water that has already been purified upstream from ultrafiltration, will be able to make full use of its capacity when it is put into contact with the dissolved organic matter found in a high concentration reactor (sludge blanket clarifier) for a suitable contact time. In this clarifier, the carbon is trapped and becomes concentrated in the sludge, thus considerably limiting the system’s water losses: the amounts are reduced from the 8 to 10% normally required for membrane backwashing to less than 2% (extracted from the clarifier).
In this case, a Pulsator or Pulsatube type clarifier will provide sufficient time without generating a potentially harmful adsorbant residence time: indeed, it is known that activated carbon, when it is close to its saturation point, can release micro-pollutants that had previously been fixed during an adsorbable OM peak (chromatographic effect).

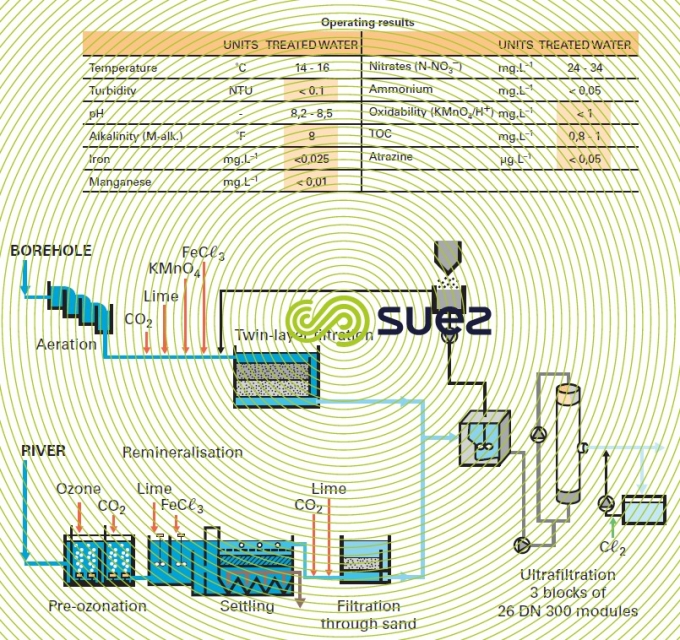

Given that many drinking water production plants already include a clarification stage (e.g. Lorient, Vigneux - France), the extended Cristal process is ideal for supplementing an existing system.

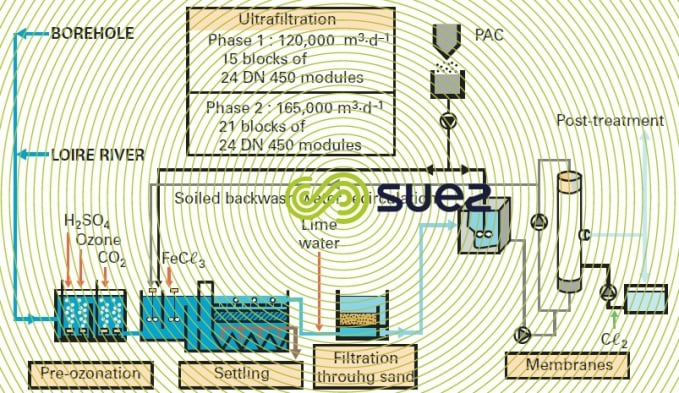


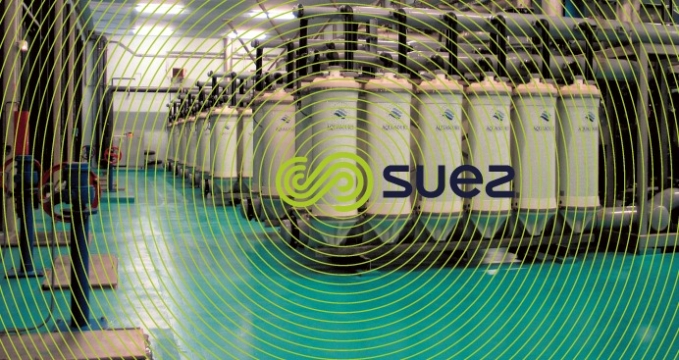


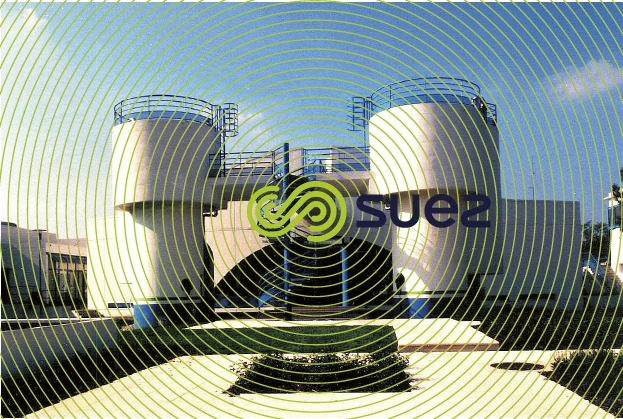

other cases involving the use of membranes in drinking water treatment
There are other ways of including membranes in conventional systems (e.g. Cristal process following dissolved air flotation) or a combination of membrane processes (e.g. MF or UF followed by NF or RO ). Overall, membranes have constituted a technological turning point in the treatment of continental water, having emerged at precisely the right moment to satisfy new health requirements and increasingly stringent quality standards.
Bookmark tool
Click on the bookmark tool, highlight the last read paragraph to continue your reading later
