hollow fibre modules
Reading time:0.6 to 2 mm diameter hollow fibres are produced by extruding the membrane material through annular dies. They are termed «self-supporting» because their thickness/diameter ratio enables them to withstand internal or external pressures encountered during their utilisation. These fibres are then grouped into bundles containing several thousands of such fibres.
Comment: some are reinforced by a textile lattice sunk into the membrane material. These fibres are then grouped into bundles containing several thousands of such fibres.
The liquid to be treated flows either inside the fibres (internal skin) or outside (external skin).
The telling advantage for this type of geometry is the possibility of carrying out regular backwashes (at a frequency of 1 every 20 minutes up to once every 2 hours) as the fibres are used under conditions that are sufficiently below their limit compression or bursting pressures.
The most recent ultrafiltration membrane is a made from multichannel Inside/Out PolyEtherSulfone (PES).
Fibres are packed together in sevens, which makes the membrane more resistant than individual fibres. As described in chapter fundamental physical-chemical engineering processes applicable to water treatment, this module can be used in dead-end or tangential mode.

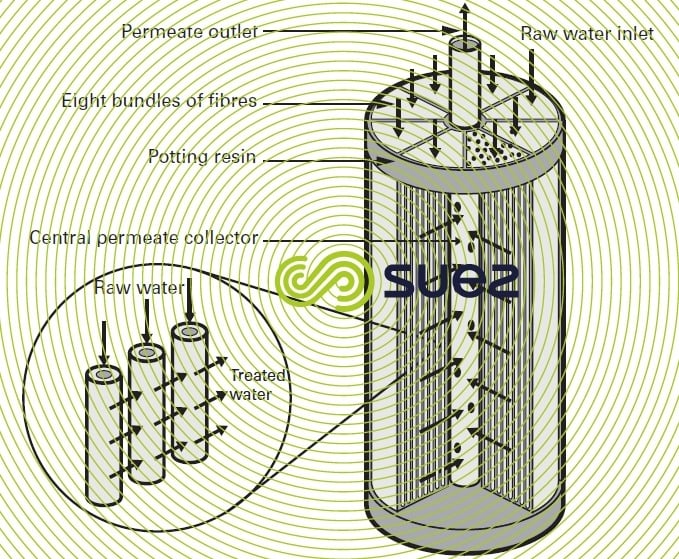

Having a similar geometry, there are also external skin hollow fibre modules where the fluid to be treated circulates outside the fibres and where the permeate is collected at one or other end of the fibres. These modules are also easily backwashed but are usually only used in dead-end mode.. External skin hollow fibres are mounted on a module or directly submerged in the water to be treated. Figure 4 shows an external skin UF module in a so-called submerged system where fibres do not have any external casing. These fibres are submerged direct in the water or in the suspension to be filtered, the filtrate being drawn up («sucked») through the fibre as a partial vacuum is created in the latter (0.2 to 0.6 bar, thus 20 000 to 60 000 Pa).

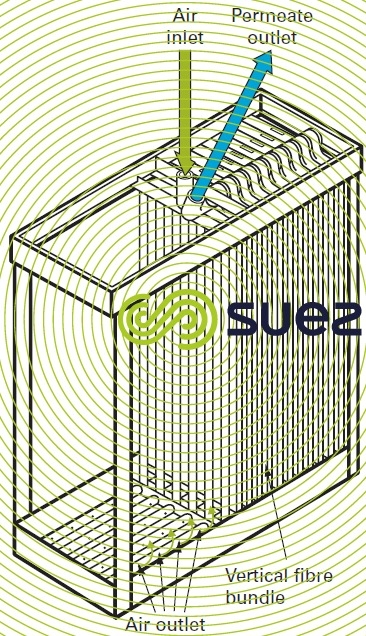

With a few exceptions (see ceramic modules) and a few flat membrane modules intended for use with membrane bioreactors, all clarification modules ( MF or UF ) are produced in these two forms, backwashable and low head losses often making operating pressures of less than 1 bar feasible.
It should be noted that all clarification modules have to be protected in order to prevent large particles from blocking either the meatus of internal skin hollow fibres or water circulation between external skin fibres. Therefore, safety micro-strainers (150 to 500 μ) must be installed at the inlet of any membrane clarification system.
Bookmark tool
Click on the bookmark tool, highlight the last read paragraph to continue your reading later
