sludge recirculation settling tank – thickener : the densadeg
Reading time:This is an optimised flocculation settling tank with external sludge recirculation, based on the principle of the lamellar clarifier used in conjunction with an integrated thickener. This system (figure 20) takes the form of a flash mixer (1), a mechanical flocculator (2), hindered flocculator (3), a settling tank (4) (90% of floc settles and thickens without rising in the lamellar), a compartmented lamellar (5) topped by crenellated collection chutes, and a circuit used to return the thickened sludge to the unit’s inlet (6).

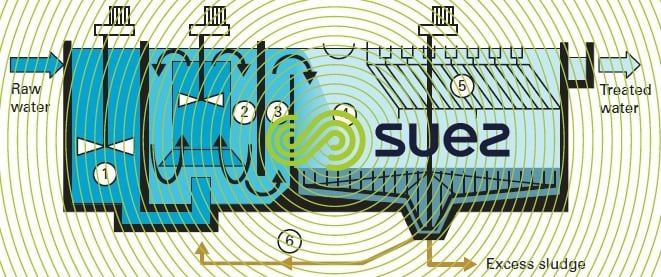

operating principle
sludge recirculation settling
Concentrated sludge is recycled at low flow rates via an eccentric rotor pump to prevent floc break-up; as discussed earlier, recirculated sludge multiplies contact surfaces and accelerates floc agglomeration phenomena. Flocculation is optimum in the Densadeg when the floc takes up approximately 10% of the space in the mechanical flocculator.
an optimized flocculation mechanism
The Densadeg flocculator with its two reactors in series (one vigorously agitated reactor and a low energy plug flow reactor) has already been described under flocculators application of this chapter.
a lamellar settling tank thickener
Three functions are carried out in this part of the Densadeg:
- most of the sludge undergoes hindered settling. This becomes feasible due to the size and, above all, the density of the floc, generating very high sedimentation rates;
- polishing takes place in the lamellar modules: the residual floc is held back in the lamellar modules that use the downstream distribution system whereby the floc is not subjected to any acceleration (unlike upstream distribution systems) and thus retain their integrity; additionally, the even speeds of passage prohibit any localised rising sludge and the settled water has the same quality over the entire collection area;
- thickening by means of a bottom scraper and a picket fence which, thanks to the density of the floc, create very rapid thickening (flow (kg · h–1 · m–2) far faster than velocities achieved with other, older solids contact clarifiers).
a double injection of polyelectrolyte
A major improvement was recently embodied into the Densadeg in the form of a double polymer injection system (patented). This system is divided between the flocculator tank and sludge recirculation.
For the same polymer consumption, we have found a host of consequences:
- floc is even denser and forms a sort of «self-ballast» that is more suited to high velocities;
- the concentration of sludge extracted rises. Most of the time, this concentration is twice as high and exceeds that of the static thickener. Thus, via this double injection system, the sludge concentration in a Densadeg processing lightly loaded surface water rose from an average of 25 g · L–1 to more than 50 g · L–1 (25 to 30 g · L–1 in a thickener);
- a more efficient use being made of the polymer, the fouling potential of clarified water dropped accordingly leading to, in the case of downstream filters, a noticeable extension of filtration cycle durations.
advantages of the Densadeg
The Densadeg is a tried and tested system; it has a number of advantages:
- it is rapid and, therefore, compact (table 3);
- it is flexible to use and not very sensitive to fluctuations in the quality and flow rate of raw water because the concentration in the flocculation zone primarily depends on thickened sludge recirculation and far less on the flocculated suspended solids contained in the incoming water;
- this system can be used to achieve very high levels of pollution reduction (in particular, the settled water has a very low turbidity) demonstrating the quality of the reactor and of the discharge lamellar and, in a number of IW applications, dispensing with the need to include filters (e.g. make-up water in a cooling circuit). In all cases where clarification is associated with a precipitation chemical reaction, excellent results have been achieved on treated water (removal of heavy metals, precipitation of CaCO3, CaSO4, 2H2O, Fe2 (PO4)3), virtually up to the theoretical equilibrium point (see industrial processes and effluent treatment);
- this system produces thoroughly thickened sludge (> 30 g · L–1) that can be dewatered without any intermediate thickener.
Table 3 provides magnitudes obtained for different applications:

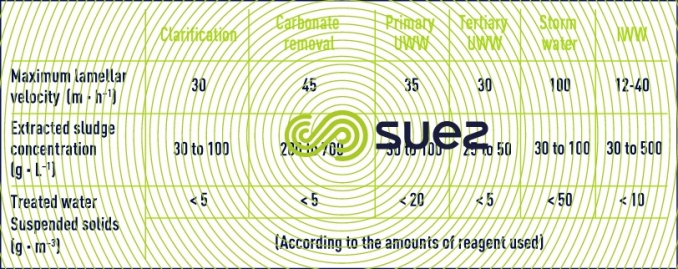

Comment: As already emphasized, in all cases, extracted sludge concentration is close to its ultimate limit (as measured in the test tube) and will even go beyond this limit when the double polymer injection method is used.
the different Densadeg (2D30, 4D30, 2D100)
The Densadeg range comprises different units depending on the application concerned and on treatment objectives:
- for a very high clarification performance solution: the Densadeg 2D or 2D30 (settling-densification). With over 200 already installed, the Densadeg 2D is the basic unit used for all types of water, maximising the removal of suspended solids and turbidity;
- for a very high velocity solution: the Densadeg 2D100 or 2D TGV on the other hand, is the unit that maximises sedimentation rate. Particularly dedicated to the primary settlement of storm water overflowing from combined systems or separate systems, the Densadeg 2D TGV is used in high speed settling of water (up to 100 m · h–1) but incurs high polymer consumption and produces a lower quality of clarified water (removing approximately 85% of suspended solids).
In UWW applications, as in the case of the Sedipac, we have endeavoured to produce a system that includes all the pre-treatment and primary physical-chemical treatment functions within a very compact solution: the Densadeg 4D30. Indeed, within one single unit, this system carries out grit removal, grease removal, high speed primary sedimentation and densification of the resulting sludge. In some cases, extrapolations at higher velocities are feasible with this unit (up to 100 m · h–1); however, this assumes that the geometry of the appliances has to be adjusted and larger amounts of reagents used ... (see 2D100).
areas of utilisation
Table 4 summarises the main applications of these units depending on treatment objectives. Treatment lines detailed in drinking water treatment, treating municipal wastewater, treatment and conditioning of industrial water and industrial processes and effluent treatment illustrate the numerous application options available.

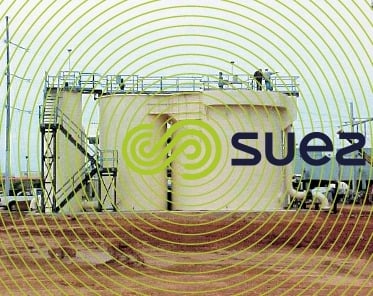


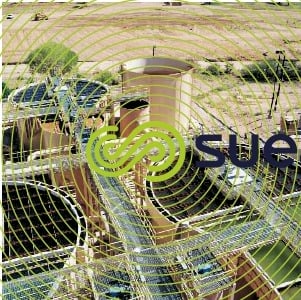


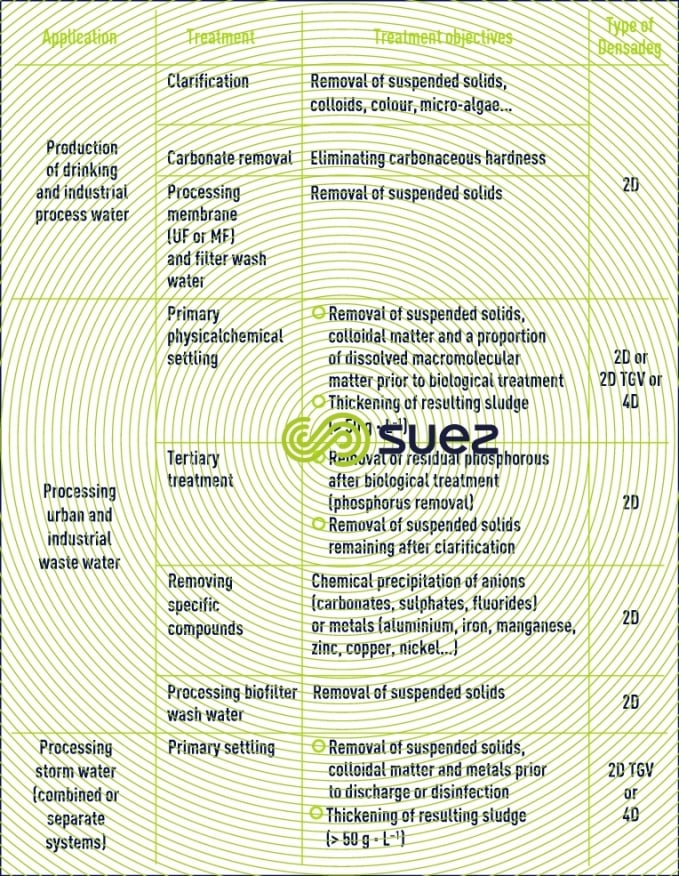

Bookmark tool
Click on the bookmark tool, highlight the last read paragraph to continue your reading later
