chemical causes
Reading time:These are linked to the composition of the cements and to the corrosive nature of the water with which they come into contact.
Cement composition is primarily based on silica, lime, alumina forming various silicates and, to a lesser extent, iron, magnesia and alkali. This composition defines a medium that is usually very alkaline and that comprises a high reserve of solubilisable salts.
When cement, and particularly Portland cement, goes off, it releases large quantities of lime in the form of Ca(OH)2, and tricalcium aluminate, «C3A», is formed.
Table 9 indicates the levels of the main constituents found in various cements.



Chemical deterioration caused by :
- aggressive nature of "free" CO2;
- corrosion by strong acid;
- action of ammonium;
- action of sulphates;
- corrosion by strong alkalinity;
- bacterial corrosion with the formation of H2S.
carbonic attack: soft water
Carbon dioxide will attack structures in the presence of fresh water or as soon as the CO2 content rises above 15 mg · L–1.
However, this remains a superficial attack and will not jeopardise structural longevity. In effect, the bicarbonates produced by the action of the CO2 on the concrete’s lime (Portlandite) will in turn combine with the lime to produce calcium carbonate which will increase the compactness of the concrete and slow down deterioration.
In order to avoid any deterioration of the surface layers, we recommend not using CPA cements but rather blended Portland cements (CPJ) or CLCs or even blast furnace Portland cements (CHF or CLK). Other recommendations :
- increasing steel coating thickness;
- use a 2 to 3 cm thick cement mortar rendering;
- ban abrasive cleaning systems such as pressurised cleaners.
strong acid attack
This attack will be all the more severe as the calcium salts formed become more soluble. Rising corrosivity will be found in the presence of the following acids: phosphoric, sulphuric, nitric, hydrochloric. Organic acids are equally harmful, especially in dairy farm or fruit juice production effluents.
When faced with moderate levels of acidity, corrosion resistance can be enhanced by reducing the water/cement ratio and/or using aluminous cements (which are also much more difficult to use). This comment applies to pH upper than 2 and subject to certain precautions.
However, as a rule, there is often the danger of structures cracking if total protection can only be guaranteed by the use of the right coating. Additionally, a number of legislations on the discharge of wastewater recommend maintaining the pH of water circulating in contact with walls at figures of between 4.5 (or 5.5) and 9.5.
action of ammonium
The presence of ammonium in wastewater can contribute to the destruction of concrete in two ways :
- by developing nitrifying and, therefore, acidifying biological reactions that can only occur in aerobic environments, such as cooling towers ;
- by releasing ammonia that has been displaced by the lime that increases its solubility and causes the cement to deteriorate.
Magnesium salts can generate the same process (forming Brucite: MgO, H2O). Therefore, we need to avoid excessively high concentrations of NH4 and of Mg, especially when sulphates are also present.
action of sulphates
This action is complex :
- sulphating of free lime in the cement to produce gypsum;
- conversion of tricalcic aluminates to form highly expansive Ettringite (factor 2 to 2.5) :


In the presence of magnesium oxide, the decomposition of the cement’s alkaline silicates can also be added to the two previous mechanisms.
The AFNOR FD P 18-011standard defines the aggressivity categories for saline water with regard to conventional concretes (table 10) together with the principle behind protection measures.
In the case of very highly aggressive water (XA3), we recommend using a coating whereas, in the case of highly aggressive water, the use of a blast furnace cement with a high hydraulicity index can be considered providing, however, that no other water chemical parameters need to be taken into account.
Examples :
- blast furnace Portland cement 85 (CLK) with 80% granulated clinker;
- blast furnace Portland cement 35 to 80 (CHF) with 60-75% clinker.
There are also various low «C3A» content cements for use in the presence of seawater.

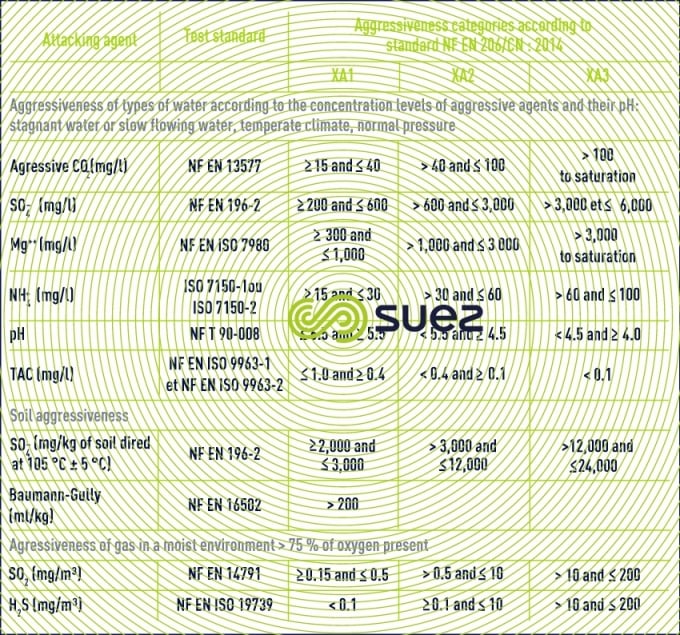

attack by strong bases (NaOH, KOH, Na2CO3)
This type of attack is damaging to all cements because of the danger of solubilisation of some constituents of the amine base; in the absence of any coatings, we recommend not allowing water with a pH in excess of 12 to come into contact with the cements.
bacterial corrosion with the formation of H2S
This corrosion occurs in urban wastewater transfers. We have already described the principle behind the corrosion mechanism in an anaerobic medium. However, whereas in cooling circuits, this process follows on from and amplifies previous chemical corrosion, in the case of sluice or extremely dirty water, it is usually caused by the anaerobic fermentation of deposited matter and comprises two stages :
- formation and release of H2S;
- oxidisation of H2S in the presence of air and formation of H2SO4.
As soon as the pH drops below 6, these reactions will accelerate and take place all the faster as water becomes hotter.
In the sewers, the attack occurs above the water/air interface because of water condensation and degassing. Adding an oxidant (H2O2), a precipitating agent (Fe2+) or nitrate will more or less totally prevent this H2S from forming.
Bookmark tool
Click on the bookmark tool, highlight the last read paragraph to continue your reading later
