corrosion inhibitors
Reading time:Corrosion inhibitors are chemical products which, when added to water or to any other process fluid, slow down the rate of corrosion. They are normally classified as: anodic, cathodic, film-forming and oxygen-absorbing agents depending on their mode of action. The effectiveness of most corrosion inhibitors is significantly affected by the water’s chemical properties and by physical conditions such as temperature and flow velocity.
anodic inhibitors
Anodic inhibitors form a protective film over anodic surfaces by blocking the electrochemical reaction that causes the metal to dissolve :

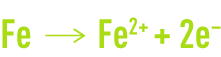
The anodic inhibitors for iron are classified as "oxidising" and "non-oxidising" products depending on whether or not they accelerate the reaction whereby ferrous iron is oxidised to become ferric iron :

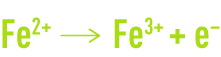
As described earlier, rapid formation of Fe3+ is essential to the formation of stable anodic passivation layers. The oxidising effectiveness of anodic inhibitors is separate from the water’s dissolved oxygen concentration at its surface whereas non-oxidising anodic inhibitors are dependant on the right concentration of oxygen. When the reaction rate is sufficiently fast, anodic inhibition is produced through the formation of an effective layer of γ-FeOOH.
Non-oxidising inhibitors act in conjunction with oxygen by catalysing Fe2+ oxidation using oxygen or by improving the physical impermeability of the γ-FeOOH layer or by a combination of both processes.
Examples of oxidizing anodic inhibitors :
- chromates (CrO42–);
- nitrites (NO2–).
Examples of non-oxidising anodic inhibitors :
- phosphates (PO43–);
- benzoates (C7H5O2–);
- molybdates (MoO42–).
cathodic inhibitors
The cathodic reduction of oxygen causes hydroxide ions (OH-) to be produced. Cathodic inhibitors are soluble at average water pH but will form a protective layer over cathodic surfaces by producing an insoluble compound that is not an electricity conductor, at high pH values.
Examples of cathodic inhibitors :
- zinc ions (Zn2+);
- polyphosphates (in conjunction with Ca2+);
- phosphonates (in conjunction with Ca2+).
Cathodic inhibitors are normally used to reinforce the action of other types of inhibitor.
combined anodic/cathodic inhibitors
Commercial formulations used in water treatment include both anodic and cathodic inhibitors for two reasons :
- the combination of these two types of inhibitor reduces the overall amount required compared with the use of one single inhibitor;
- circuits that are exclusively treated with anodic inhibitors are sensitive to pitting corrosion when the treatment is interrupted, under-dosed or wrong for any other reason.
This combined usage became established during the 1950’s when the use of zinc-chromates began to catch on. Zinc is a purely cathodic inhibitor whereas chromates work as anodic inhibitors. When chromates were being used on their own, amounts of 400-600 mg · L–1 of chromate ions were needed to properly inhibit steel. The use of zinc (~ 5 mg · L–1 of Zn2+) with chromates enabled the amount of chromate used to be limited to 20-30 mg · L–1.
Other examples of combined inhibitors :
- phosphates – zinc;
- phosphonates – zinc;
- phosphates – polyphosphates;
- phosphates – phosphonates.
oxygen absorbers
The anodic and cathodic inhibitors described above work well in the presence of dissolved oxygen concentrations created through normal air/water contact. In high temperature or sealed systems such as boiler circuits or domestic central heating systems, effectiveness drops to very low values as the result of the reduction of the oxygen dissolved in the water. Chemical products used for this purpose tend to be reducing agents designated "oxygen absorbers".
Examples of some of the more common oxygen absorbers :
- sulphites;
- elementary hydrogen gas;
- hydrazine or carbohydrazine;
- organic reducing agents (erythorbate, hydroquinone, gallate).
In addition to the role they play in reducing oxygen concentrations, some oxygen absorbers promote the formation of a protective magnetite film. For instance, hydrazine and carbohydrazine encourage passivation by producing hydrogen peroxide.
organic inhibitors
The action of these inhibitors is linked to the formation of a monomolecular film between the metal and the water. These products are often "film-forming" surfactants with hydrophobic and hydrophilic groups. The hydrophilic extremity attaches itself to the surface of the metal while the hydrophobic extremity forms a barrier between the water and the surface of the metal.
The film-forming amines are routinely used as corrosion inhibitors in vapor condensate circuits. These fatty amines have 4 to 18 carbon atoms and are disposed parallel to each other and, perpendicular in relation to the walls, creating a continuous and impermeable film. The amount used is between 2 and 20 mg·L–1. In condensate return circuit protection, these film-forming amines are recommended when large quantities of CO2 are released, i.e. when the consumption of neutralising amines becomes prohibitive.
protection for non-ferrous metals: copper and aluminium
A large number of cooling circuits contain copper or copper alloys. As stated earlier, copper is more noble than iron. In pure, de-ionised water, it can be found in a state of immunity. However, in practice, copper alloys are predisposed to corrode because of the presence of powerful oxidising agents such as elementary chlorine or of aggressive pollutants such as ammonia.
Corrosion in copper alloy is harmful not only because of the damage it causes to the components affected but also because of the effects of dissolved copper (Cu2+) in cooling water. This copper can be reduced to copper metal on the surface of other ferrous metals, creating conditions that favour galvanic corrosion.
The most commonly used inhibitors for copper alloys are azole derivatives :
- mercaptobenzothiazol;
- benzotriazol and its derivatives;
- benzimidizol and its derivatives;
- zinc (Zn2+).
Mercaptobenzothiazol has largely been replaced by benzotriazol derivatives on grounds of chemical stability and toxicity problems. All copper inhibitors are affected in some way by halogen biocides but triazols to a lesser extent.
Aluminium is particularly sensitive to electrolytic corrosion. The most common inhibitors are silicates, phosphates, organo-azoles and molybdates.
the use of inhibitors in industrial circuits
Corrosion inhibition is just one of the aspects of water treatment in industrial circuits; corrosion inhibition is always linked to the fight against scaling and to the prevention of microbiological growth. In practice, the use of corrosion inhibitors must be compatible with all other water treatments, circuit characteristics and operating parameters (see chapter using ion exchangers and treatment and conditioning of industrial water).
Bookmark tool
Click on the bookmark tool, highlight the last read paragraph to continue your reading later
