paper mills and the paper pulp industries
Reading time:The manufacture of paper consists of two main operations: the production of pulp which is then transformed into paper or cardboard. Industrials can integrate both manufacturing processes.
paper pulp manufacture
unbleached pulp manufacturing processes
Paper pulp is manufactured from the cellulose fibers contained in wood. Several processes are used to destroy the wood and isolate the cellulose from the lignin:
- A chemical process, enabling pulp intended for fine paper production to be obtained (printing, writing). Lignin becomes soft under the effect of heat or chemicals:
- the kraft process, is still the process most used because it has the better resistance properties than the pulp obtained by a bisulphite process. Able to be used for all types of wood, the kraft process is based on the alkaline cooking of wood (NaOH, Na2S), dissolving 40 to 50% of the wood's dry content. Organic matter is found in the cooking liquid (black liquor) and in pulp wash water. Bleaching such pulp reduces the overall yield by around 10% and predominantly contributes to the colour of the effluent;
- the bisulphite process is based on the acidic cooking of wood (dissolving the lignin via Ca, Mg or NH4+ bisulphites). Such pulp is nearly always white. The entire pH range can be used and this explains why the process allows several types of paper pulp to be produced with varying qualities for a wide range of uses.

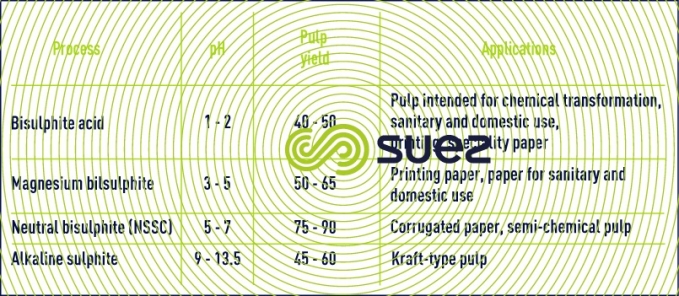

- Semi-chemical process, which creates the pulp essentially found in corrugated paper, as the presence of lignin in fibers makes it rigid.
- Mechanical process, used for manufacturing newspaper pulp. The main manufacturing processes are milling, fibers removal using pressure, thermomechanical pulp and chemical-thermomechanical pulp.

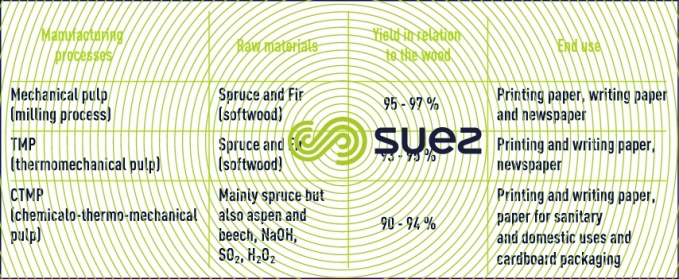

bleaching
For numerous applications unbleached pulp cannot be used (colour, impermeability, etc.). It must therefore be bleached.
Effluents from bleaching works contain compounds with organic chlorine links, measured as AOX. In the entire paper pulp plant, this operation discharges the highest amount of pollutants into the water. In general, it discharges between 20 to 40 m3 of wastewater per tonne of pulp.
bleaching pulp using ozone
To meet market demands, new, more environmentally bleaching technologies have emerged and are now based on delignification using oxygen with an ozone step and/or a peroxide step. The processes are known as Total Chlorine Free (TCF) processes, where gaseous chlorine is no used and Elementary Chlorine Free (ECF) where bleaching is performed using chlorinated derivatives such as chlorine dioxide, ozone or hydrogen peroxide.
These two techniques differ according to the level of organohalogenic compounds (AOX) they release into the water. ECF, which generates a significant quantity of AOX and dioxins, remains the most used process accounting for 60 to 80% of bleaching sequences worldwide.
The use of ozone as a bleaching agent has several advantages. It is a low temperature, powerful oxidant generating quick reactions, with the possibility of recycling filtrates in order to recover chemicals, as well as effective delignification of all types of chemical pulp.
It should be noted that it has already been demonstrated (on an industrial scale or large pilot) that ozone also allows:
- pulp from old paper following de-inking to be whitened;
- kaolin and calcium carbonate to be whitened: input loads in the composition of paper sheets;
- mechanical characteristics of fibres from thermomechanical processes to be improved (by removing a portion of the residual lignin)
With the knowledge that 15 to 250kg/j of ozone is required per generator for a modern pulp and paper plant (3 to 5 kg O3/ADt), paper pulp treatment has become a significant outlet for ozone (references in Sweden, Finland, South Africa, Brazil, the United States, Japan, etc.).
The economic optimum is achieved when the concentration of ozonated oxygen leaving the ozone unit is between 10 to 14% in weight. Today, this correctly achieved with very good energy consumption of around 12 kWh.kg-¹ O3.
Ozone is used:
- either with a high consistency pulp (30 to 40% DC). In this case slightly pressurised mixers are used. Compared to an ECF process the volume of wastewater and water consumption is reduced by 30% and the COD load to 40%;
- or an medium consistency pulp (10 to 12% DC). In this case ozone is at 12-13% and the mix is performed a pressure of 10-12 bars. This supposes that the compression is controlled without destroying ozone. In the optimised system, losses are less than 3%.

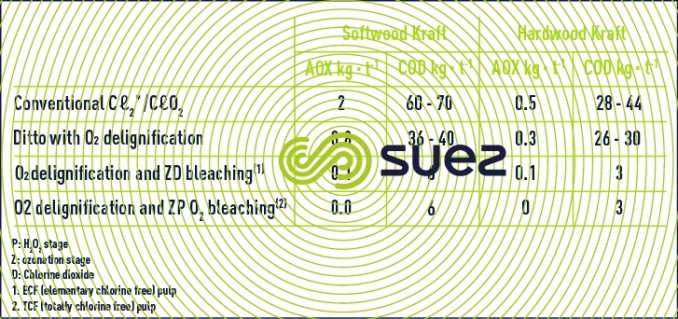

wastewater
Wastewater and residual detergents in the pulp and paper industry are the amongst the most dangerous types of industrial wastewater in regards to their quality and composition.
In a modern plant four types of effluent can be discerned:
- condensates from cooking and evaporation;
- washing and draining;
- preparation of wood (bark removal, cutting and pressing;
- bleaching
The resulting effluent has the following characteristics:
- very high flow rate: between 15 m3.t-1 and 150 m3.t-1 ;high insoluble pollution (fibers and fibrils, CaCO3, clays) characterised by a non-negligible suspended solids content which cannot be "settled" (around 10 to 30% of TSS):
- variable soluble pollution depending upon the process: BOD5 between 100 and 1000 mg/L; COD between 300 and 4,000 mg/L (biodegradabiity very dependent upon the wood's nature: pine, hardwood); colour: significant and resistant to biological processes.

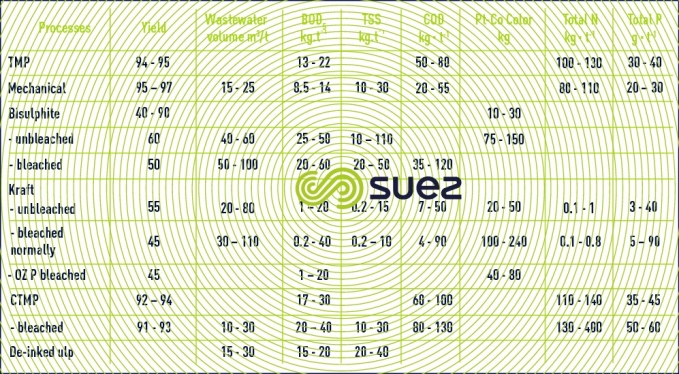

From previous effluent, black liquor, evaporation condensates can be treated separately from concentrated pollution sources. These can account for less than 10% of the discharge volumes, but contribute to 30 to 50% of the BOD5. Indeed, black liquor (cooking liquor from kraft paper manufacture) is highly concentrated and is generally treated separately (evaporation, incineration and reagent recovery). These condensates have the following characteristics (table 57).

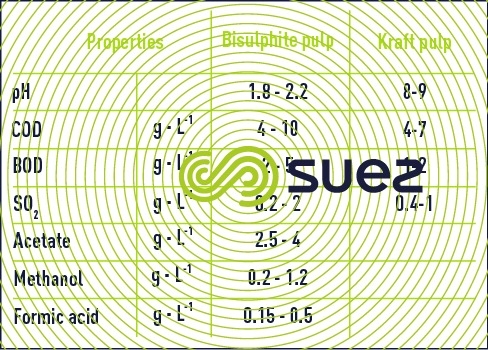

paper and cardboard manufacture
Manufacture: paper is manufactured from new pulp, from old paper regardless of whether or not it has been de-inked, or from rags.
The use of these primary materials, separated or mixed, ensure the production of paper ranging from fine paper to packaging paper and corrugated cardboard.
According to the target qualities, different additives and coating chemicals may be added:
- mineral loads: kaolin, CaCO3, talc, TiO2
- organics (starch, latex)
- dyes, aluminium sulphate, retention agents.
De-inking can be performed two ways:
- counter-current washing with a high water flow rate;
- by mechanical flotation, at lower flow rates but with more reagents (soda, sodium silicate, fatty acids, anionic detergents) and with an enormous amount of suspended solids discharged.
When old paper is used, certain specific waste such as staples, plastic, ribbons are also present in the water to be treated.
Effluent is therefore characterised by a varying load in fibers and additives, which generally are not very soluble.
Most modern machines are equipped with two internal circuits:
- a primary circuit called 'short' enabling dripped water to be immediately reused, rich in fibers
- a secondarycircuit which receives water from suction, pressing and rinsing tanks and into which fibers recovery equipment is installed (pulp trap).
The machine's outer or tertiary circuit receives excess water from the secondary circuit and auxiliary water.
The general treatment process is located on this circuit and from which the recycling of water or sludge into the manufacturing stage may be organised, depending upon the quality of paper manufactured. Recycling can concern up to 100% of the sludge and 50 to 100% of water for a plant using old paper. The recycling rate which may be implemented relies on great skill in paper-making and water treatment.
This effluent's COD is in general two to three times higher than the BOD5.
When old paper is used in manufacturing, the concentration level of dissolved organic pollution is particularly high.
Table 58 gives the pollution characteristics for "tertiary" circuits.

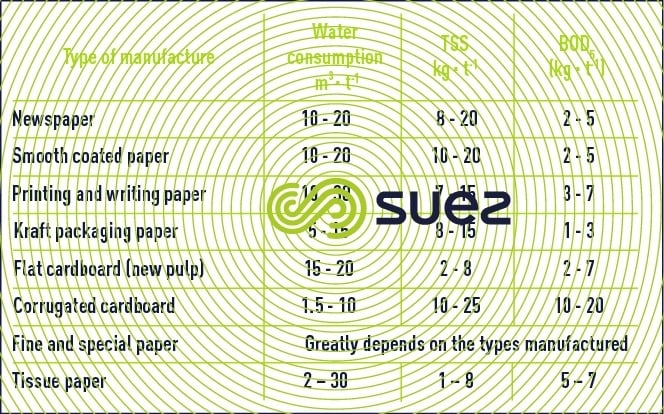

Bookmark tool
Click on the bookmark tool, highlight the last read paragraph to continue your reading later
