textile industries
Reading time:Water constitutes the main vector for the removal of impurities, for applying dyes and finishing agents as well as for generating steam. The textile industry's main concern is the quantity of effluent generated and the high chemical load it contains. The most significant environmental impacts are caused by (in order): salts, detergents and organic acids.
End effluent, where various streams coming from the different processes are mixed together, has characteristics which result from a combination of the following complex factors:
- the types of fibres used;
- the types of articles treated;
- the techniques deployed;
- the types of chemicals and auxiliary products used for the process.
The resulting releases are even more difficult to streamline and compare according to production, likely to vary during the year (seasonal changes, changes in trends) as well as on a daily basis in accordance with the manufacturing schedule.
washing and combing of wool
Raw wool is a product which has many impurities (250 to 600 kg per tonne). These can be broken down as follows:
- 25 to 30 % of fats (wool grease and fatty acids)
- 10 to 15 % of earth and sand
- 40 to 60 % or organic salts and wool grease.
Global COD is estimated at around 150 to 500 g/kg of raw wool. The washing process and the effectiveness of the grease and impurities collection systems are closely related to COD content.

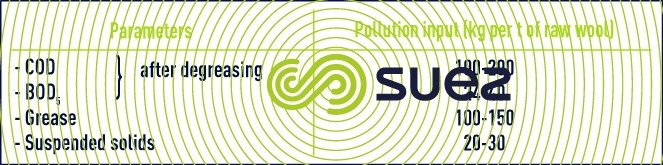

Scouring of wool results in the discharge of effluent which is highly loaded in organic matter and containing varying quantities of micropollutants coming from the pesticides used on sheep.
Veterinary medicine residues present in wool are potentially harmful to the environment: ectoparasiticides are the most commonly found. Concentration levels of ectoparasiticides ranges from 2 to 15 mg/kg of raw wool. After a wool washing process, 96% of pesticides present in the textile are removed (4% are still retained by the fiber after washing).
pretreatments before textile finishing operations (tableau 51)
Impurities present in raw wool, preparation chemicals, spinning lubricants, sizing substances, are usually removed from the fibre during pretreatment and may lead to the discharge of organic substances which difficult to biodegrade (e.g. mineral oils and hazardous compounds such as PAH ).

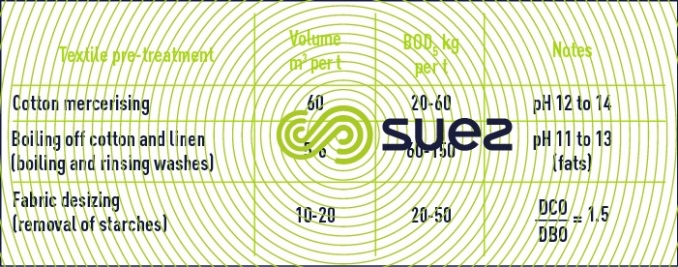

Mercerisation is the cause of high quantities of alkaline in discharged wastewater. However rinsing water from this operation may be recycled but only after having been concentrated by evaporation.
Desizing cotton fabrics can account for 70% of the total COD load in the final effluent. Emission values in the order of 95g of COD/kg of fabric are frequently found with concentrations in COD often above 20g COD/L.
textile dry-filling
This activity is usually generates considerable pollution and involves the following operations: bleaching, dyeing, printing and sizing.
The volumes discharged will vary depending on the dry-filling combinations and we can only provide rough values in this instance:
- acrylic fibres 35 m3·t–1;
- wool 70 m3·t–1;
- cotton 100 m3·t–1;
- towelling 200 m3·t–1;
In fact, pollution loading is dependent on:
- fibre type: natural or synthetic; more or less charged
- dyeing (open width, padder, autoclave) continuous, batch, semi-continuous and printing processes; dyes don't represent a signifiant charge, but they can interrupt the photosynthesis and therefore affect the aquatic life if the color is intense
- products used according to their water solubility (table 52).

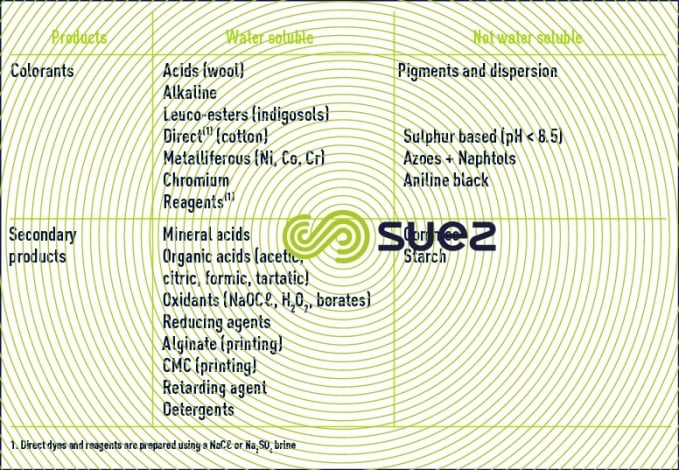

Mixed with pre-treatment effluents, discharges are more dilute and can be characterised by the following typical values:
- pH 4 to 12, usually alkaline; 4.5 knitted woollens; 11 cotton;
- COD: 250 to 1,500 mg·L–1 or 50 to 150 kg·t–1;
- BOD5: 80 to 700 mg·L–1, with a COD/BOD5 varying between 2.2 and 5;
- colour: 500 to 2 000 units Pt·Co·L–1;
- Suspended solids: 30 to 400 mg·L–1 (not very abundant, fibre, staple, down), but occasionally reaching 1,000 mg·L–1 (case of cotton);
- Cr(VI) 1 to 4 mg·L–1 and S2–: 0 to 50 mg·L–1;
- rising temperatures as volume reduction targets achieved.
Jeans washed with pumice (1 kg per kg) can cause massive discharges of suspended solids.
industrial laundries
Depending upon their size, laundries can discharge highly polluted effluent, very often constituted of cleaning products which are deployed on site.
The volume of wastewater in modern and counter-current washing units is around 2 mᶟ per 100 kg of laundry and corresponds to 1.5 kg to 2 kg of BOD5.
Bleaching can be carried out using:
- sodium hypochlorite (bleach), causing secondary reactions which form organohalogenic compounds usually measured in AOX
- chlorite where the quantity of AOX is caused by the chlorine or hypochlorite
- hydrogen peroxide. In this case, the complexing agents (stabilisers) are responsible for the pollution
Bookmark tool
Click on the bookmark tool, highlight the last read paragraph to continue your reading later
