safety and drying units
Reading time:Sludge drying units must be subject to appropriate safety measures because they are the source of a number of risks, more specifically in the event of certain malfunctions. Without being exhaustive, the following constitute risks associated with drying plants :
- risks linked to the self-heating properties of dried sludge;
- risks linked to the pyrolysis gas production (CO, CH4…), either in connection with self-heating phenomena, or with certain heat type malfunctions that generate direct pyrolysis;
- risks linked to explosions; these can be of different types and create a cumulative effect:
- explosion caused by the O2 and dust concentration in the air;
- self-combustion caused by CO and O2 levels;
- risks linked to sparking phenomena (static electricity).
- risk of operatives burning themselves on the thermal equipment;
- as thermal equipment is often in a vertical position, risks of operatives falling
- risk of bacteriological infection by operatives during handling of dewatered and/or dried sludge.
On these grounds, all sludge drying plant must undergo a hazard and risk analysis (ATEX and HAZOP) together with a regulation-based classification appraisal. These studies have to be carried out by specialists.
Safety parameters must be incorporated from the outset into drying unit projects and engineering; they must also be included in the functional analysis and interact with regulating and automated control systems. Operating personnel must be trained in these risks and measures. This work has not been designed as an in-depth statement. However, we do feel the need to emphasise the most important issues.
self-heating and dried sludge
Self-heating is the result of dried sludge exothermic oxidation reactions where the energy is not sufficiently dissipated because the dried sludge does not provide sufficient conductivity in the space concerned. This can be seen as a pile of dried sludge that is thought to be stable but whose temperature changes. Beyond a certain threshold, we have the start of pyrolisis.
The presence of iron in the environment plays a key role in the start-up of the self-heating process. The form in which iron is present in the end product plays a key role in the stability of dried sludge. This is the 'match' which can start a chemical and thermal chain reaction.
Studies carried out at the Bern plant in Switzerland in a thesis by Martine Poffet on the "Thermal runaway of the dried sewage sludge in the storage tanks: from molecular origins to technical measures of smouldering fire prevention" in 2008, indicate that the initial reaction in self-heating is the oxidation of Iron 2 into iron 3.
The reaction's pathway (as described in the thesis by Martin Poffet) is described below :
- Up to a temperature of 75°C: oxidation of amorphous Fe2+ - start of catalytic oxidation
- From 80°C: oxidation of crystallised Fe2+ such as, for example, vivianite (Fe3(PO4)2, 8H2O)
- Above 120°C: self-catalytic oxidation of organic matter, then its combustion (thermal reaction).
- Smouldering phase
Amounts of iron in primary sludge before digestion (most of the time in the form of ferric chloride) allow sulphurs produced during anaerobic digestion to be complexed into iron sulphide (FexSy).
The reactions taking place with FexSy are extremely exothermic and act as aggravating factors in the selfheating of dried sludge.
Biological reactions from aerobic-type oxidation may also be at the origin of a temperature increase in stored organic material. These biological reactions bacterial or mycelial populations working and which require water to break down organic matter. For example, thermophile anaerobic digestion: it is these bacterial populations which, by breaking down organic matter, generate a temperature of between 50 to 60°C. If these biological reactions do not reach temperatures higher than 70°C, then other chemical reactions will take over in order to generate selfheating temperatures in organic matter.
The level of self-heating varies according to the sludge's characteristics.
Thus, some types of sludge are more at risk than others. This is the case, for example, of primary sludge, digested or not, and mixed digested sludge. The aggravating factors are :
- Iron and sulphur content
- The temperature of dried sludge when entering storage
- The volume stored
The presence of industrial effluent in the network can also have an influence on the reactivity of a sludge to selfheat.
Therefore, it is not the dryer's technology which is responsible for the sludge's self-heating nature, but the characteristics of the sludge itself.
the consequences on the storage of sludge
Self-heating temperatures are experimentally determined in a thermostatic drying cabinet with volumes (cubes) of calibrated dried sludge. The critical self-heating temperature (Figure 23) is thereby determined according to the volume.

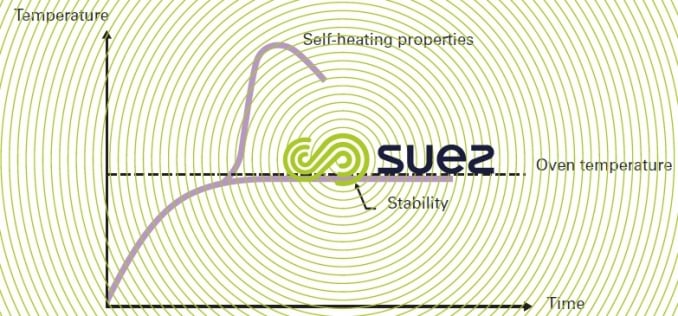

Experimental findings for the different sludge types and particle sizes are used to plot characteristic curves that will serve as the basis for dried product storage system design (figure 24). We strongly advise against designing a thermal drying system without referring to the characteristic curve for the sludge to be treated.

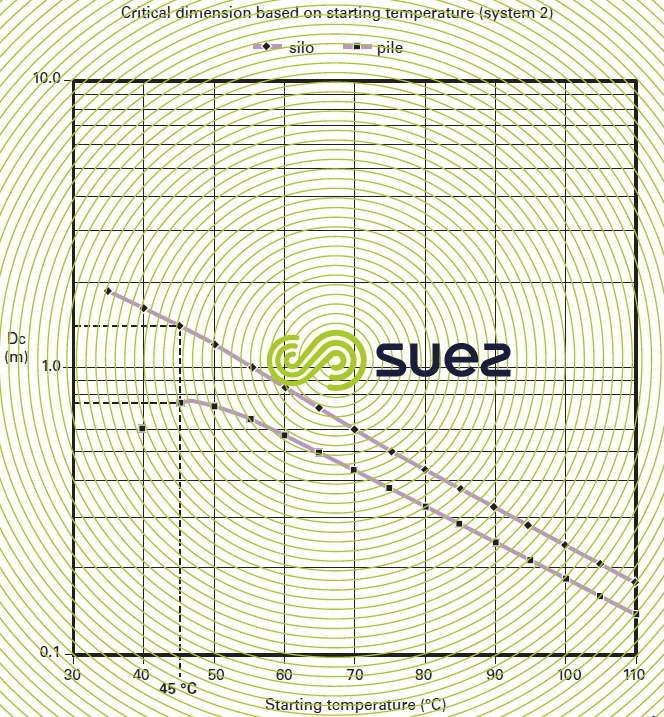

All short or long-term buffer storage design must comply to the regulations established using the sludge's selfheating characteristic charts. In addition, all storage silos must be equipped with explosion vents, wires equipped with temperature sensors in order to obtain a comprehensive map of the inside of the silos and an inerting system (N2 or CO2) activated in relation to the CO content in the silo's head vapours or to the temperatures measured in the wires. The CO detectors positioned in the silos's head vapours are also indicators of pyrolysis.
It is also possible to carry out silo transfers. This allows dried sludge to be transferred from one silo to another and also to gain in storage time because dried sludge is transferred as soon as the threshold temperature has been reached. Silo transfer allows the sludge's temperature to be lowered in the storage vessels during transfer and sends the sludge to cooler containers. Transfer also lowers sludge temperature through the supply of air from the pneumatic silo transfer, thereby re-oxygenating the sludge.
the consequences on the transportation of sludge
The United Nations has published a guide on the Transport of Dangerous Goods (TDG). This regulation is of interest because the same tests (UN tests) implemented for the classification and transport of dangerous goods and for the labelling of products can be implemented here.
Dried sludge is there concerned by Class 4, Division 4.2 (spontaneously flammable material), with the N4 test on self-heating substances. Substances or mixtures are classified as self-heating according to the result of the tests in accordance with the N4 method (known as the UN N4 test) described in the recommendations on the transport of dangerous goods, the United Nations' test manual and criteria, third part, sub-section 33.3.1.6.
The UN N4 test provides information on the sludge's aptitude to self heat through oxidation in air at temperatures of 100°C, 120°C and 140°C in a cube-shaped, sheet steel cage measuring 25mm or 100mm, placed inside a furnace.
The test is positive when the sludge sample's temperature exceeds that of the furnace's by more than 60°C.
The test therefore provides information on the risks of the sludge to self-heat during storage and also enables the sludge examined to be classified with a view to its transportation.
A sludge classified as 4.2 must also be attributed to a Packaging Group :
- Packaging Group II: high danger of self-heating
- Packaging Group III: low danger of self-heating
Packaging is mechanically tested (falls, stacking, etc.), tested for its impermeability, and subjected to pressure tests, conducted by accredited laboratories.
A sludge classified as 4.2 must therefore be transported in suitable packaging. The transportation vehicle must be in compliance with the ADR regulations (European Agreement on the Road Transportation of Dangerous Goods): specific labelling, type of vehicle, driver training, etc. This therefore requires that the manager in charge of sludge removal from the plant takes measures, which could be costly.
main properties of dust created by dried sludge
Table 7 details the dust properties to be taken into consideration when rendering a drying unit safe. This table also provides typical values. These properties must be known when this type of system is being designe (measurements if there is sludge, or else by analogy).

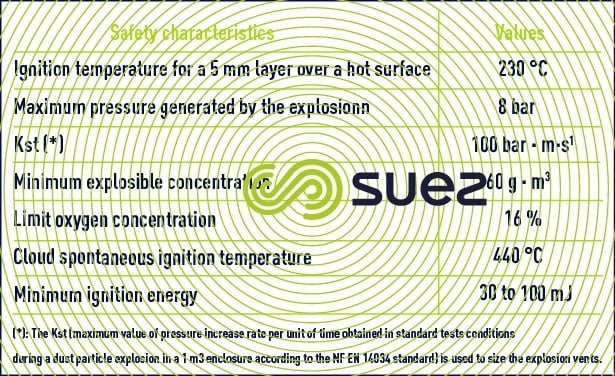

consequences for engineering
Besides the numerous regulations to be taken into account when designing dried sludge storage vessels, other dryer unit equipment is also subject to important safety measures :
- The indirect dryer steam loop as well as the heat exchange fluid loops of direct dryers must be equipped with an O2 measuring device and it is recommended that an CO one also be included;
- Depending upon the nature and the design of the handling machinery and risk of sparking coming from these, the necessary explosion proof dampers should be suitably installed (e.g. making safe bucket conveyors);
- According to the type of equipment and risk of explosion, suitable fireproof shutters should be installed in order to that an initial explosion does not cause a second, larger explosion (e.g. protection of bag filters).
All these measures obviously have a cost (in terms of investment and operation). They are however essential and unavoidable in a drying unit's design.
Bookmark tool
Click on the bookmark tool, highlight the last read paragraph to continue your reading later
