drying unit energy consumption
Reading time:In a drying unit, the heat balance is a simple matter. This balance is used to establish the energy required to evaporate water and to raise the temperature of the dry solids. The drying unit's total energy will in fact be the figure obtained via the balance and provide by the overall efficiency of the boiler responsible for heating the heat exchange fluid.
To overcome differences in the boiler's yield, it is preferable discuss the thermal consumption at the dryer terminals.
The cost of energy expenditure can account for up to 50% of a dryer's total operating costs.
More specifically, the following constitutes an example of a Naratherm dryer heat balance (table 6) :

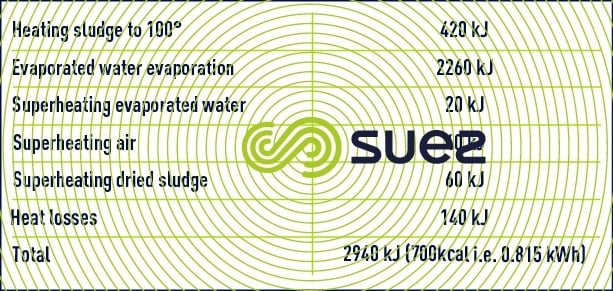

It can be seen that 80% of the energy is used to evaporate water. Theoretically, this also means that all this energy can be recovered when the sludge has been condensed; unfortunately, this occurs at low temperatures and is, therefore, of little use – except with the Evaporis™ LE.
Overall, a drying unit’s thermal energy consumption at the dryer's terminals is around :
- for indirect dryers 2,700-3 060 kJ · kg–1 evaporated H2O (750-850 kWh t–1evaporated H2O) ;
- for direct dryers 2,880-3 250 kJ · kg–1 evaporated H2O (800-900 kWh t–1evaporated H2O) ;
- for combined dryers (excl. Evaporis™ LE) 3 060-3 430 kJ · kg–1 evaporated H2O (850-950 kWh t–1 evaporated H2O).
A thermal dryer's real consumption is often higher due to the start-up phase which can last several hours and which can occur frequently depending on operating conditions.
In regards to the drying unit's electricity consumption, this varies according to the dryer and to the peripheral equipment in place, often varying from one site to another (presence or absence of a pellet-making unit, type of dried sludge conveying systems and the length of conveying, etc.).
the Evaporis™ LE dryer :
Through its partial recovery of latent heat from the evaporation of water between the 1st and 2nd levels, the Evaporis™ LE enables very high performances to be achieved, at around 2,230 to 2,600 kJ · kg–1 evaporated. H2O at the dryers terminals (between 620 and 720 kWh t–1 evaporated H2O ).

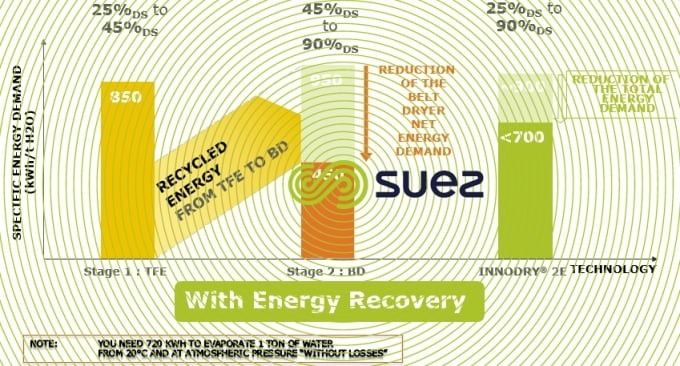

In the above example, without energy recovery, thermal consumption at the dryers terminals would be in the order of 900 kWh t-1 evaporated H2O, whilst for the same consumption the value is 700 kWh t-1 evaporated H2O for an Evaporis™ LE dryer, i.e. an energy saving of 20%.
the Evaporis™ LT dryer :
By operating at a low temperature, as is the case of the Evaporis™ LT dryer, it is possible to recover any available low calories coming from other thermal equipment. For example, flue gas from a cement kiln is released at a temperature of around 200°C. Via a flue gas/water exchanger recovering the calories from this flue gas, it is possible to heat the water required for warming the air which circulates inside a closed loop in the Evaporis™ LT dryer. Of course, the dryer is dependent on the operation of the cement kiln but the thermal energy consumed by the dryer is free of charge, which is far from being insignificant in terms of the operating balance sheet.
Bookmark tool
Click on the bookmark tool, highlight the last read paragraph to continue your reading later
