a few specific technologies
Reading time:dryers without recirculation
Due to the difficulties in operating intensive recirculation dryers, dryers without recirculation are the preferred choice.
the innoplana® combined dryer: Evaporis™ LE (low energy)
This technology has recently been developed by SUEZ (photo 5 and figure 6). The Innodry is a mixed dryer where the first stage is a thin layer dryer and the second, a hot air belt dryer.
This process features two major innovations :
- between the two drying stages, the pre-dried product which is in a high viscosity phase, is easily extruded (agglomeration consistency) as strands of spaghetti in the extruder. Thus, the belt dryer pellet bed is very permeable and eliminates the need for a subsequent shaping unit ;
- The indirect method is used to condense the vapour emitted during the first drying stage and the vapour’s latent heat is recovered for use in heating the hot air loop acting as the second stage heat exchange fluid.
- With its patented energy recovery loop,Evaporis™ LE is highly efficient whilst reducing the dryer's energy consumption by a quarter compared to other drying technologies.
This range of dryers has currently been developed to provide an evaporating capacity of up to 6 t·h–1.

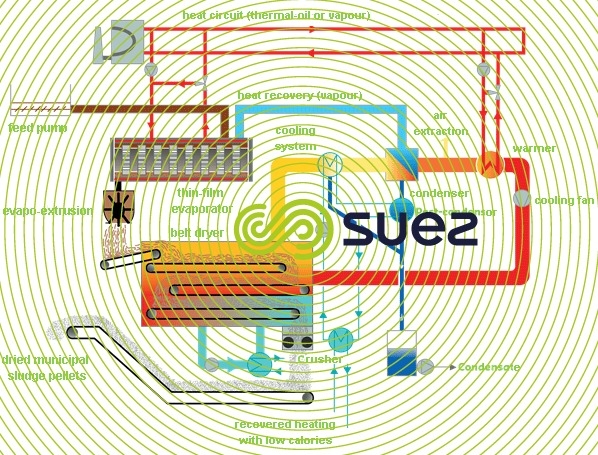

Evaporis™ LE has the following advantageous characteristics :
- The density of dried sludge is high thanks to the formation of sludge with an intermediate dry content level (density of dried sludge of around 500-600kg/m3 with a crusher).
- The temperature of dried sludge leaving the dryer is low because the last part of the belt dryer cools the dried sludge before its leaves (40 °C, even <5 °C) allowing to securely transport and store dried sludge.
- Evaporis™ LE is also a modular dryer thereby enabling the dryer to be sized according to the load to be treated.
- The dried sludge comes out of the Evaporis™ LE dryer in the form of granules (photo 6)

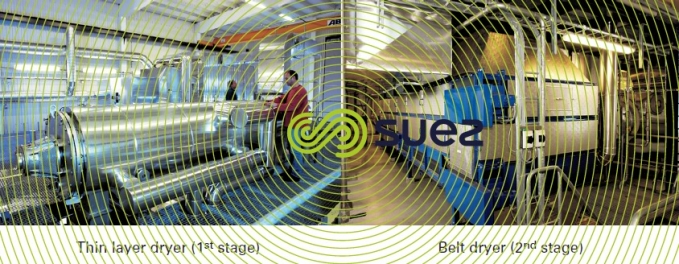


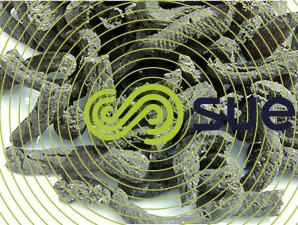

stc's direct low temperature belt dryer: the Evaporis™ LT (low temperature)
The belt dryer is based on a continued drying principle using hot air convection in a closed tunnel. The Evaporis™ LT dryer has the particularity of being comprised of a series of modules into which sludge is introduced and shaped by an extruder (module 0), located on the upper belt. Sludge then passes through the drying module(s) and then offloaded onto the lower belt (module R) where it again passes through drying module(s) before extraction in the form of dry granules.
Evaporis™ LT is also a modular dryer thereby enabling the dryer to be sized according to the load to be treated (figure 7 and figure 8).

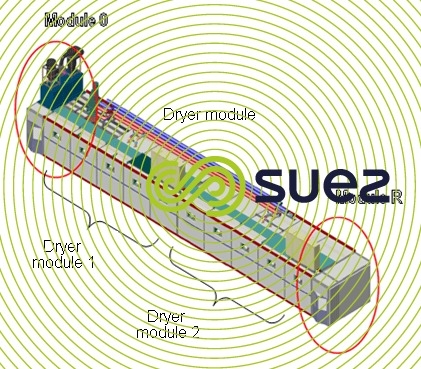


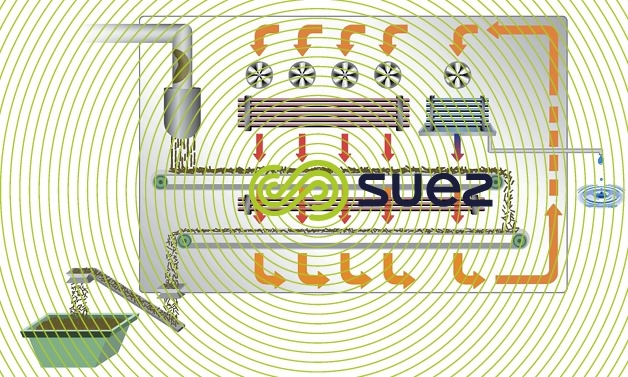

The dry content of sludge must be adequate enough to ensure that the sludge's shape following extrusion is maintained.
Evaporis™ LT has the following advantageous characteristics :
- Use of low temperature heat (<90°C): cogeneration flue gas, heat from cogeneration motor, hot water system, etc,…
- Use of an industrial heat pump in the absence of residual low energy.
- A combination can also be used (heat pump and boiler for hot water production).
- Dried sludge leaves the Evaporis™ LT dryer in the form of granules.
Currently, the range of these dryers is being developed with an evaporating capacity of up to 8 t·h–1 per unit.
Vomm combined dryer (figure 9)
This dryer is comprised of a thin layer dryer combined with direct hot-air drying. Dewatered sludge enters a cylinder heated by a double-casing inside which heat transfer oil circulates. To decrease the size of the drum. Vomm combines this with direct air drying: hot air circulates in a drum which also has the effect of pushing the sludge through the dryer. Retention time is 2 to 5 minutes.
At the outlet, all the sludge is collected by the hot air current and sent to a separation cyclone followed by a bag filter to recover the dried sludge.

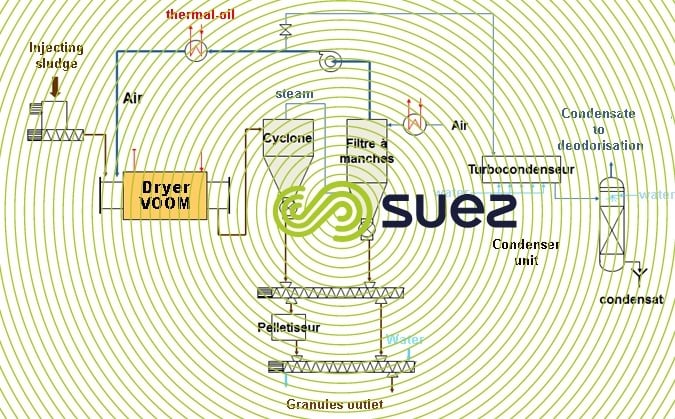

Dried sludge leaves combined dryers, such as the Vomm, in a powder form (photo 7). Pelletisation is not compulsory in this type of dryer, but it is often carried out.

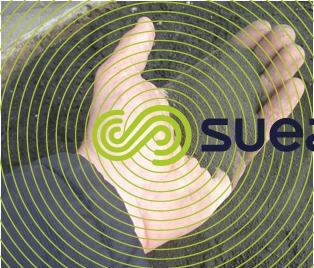

the mass dryer (Andritz Gouda, Komline-Sanderson) (photo 8)
This dryer is comprised of a double-skinned trough. Two parallel shafts are positioned in the trough with each shaft having a large number of specific geometric blades. Heat exchange fluid runs though the entire unit (double-skinned trough, shafts and hollow blades). This is either dry saturated steam under a pressure of between 5 and 10 bars, or thermal oil at temperature of between 160°C to 200°C.
The shafts slowly turn in opposite directions, which kneads the sludge making it uniform.

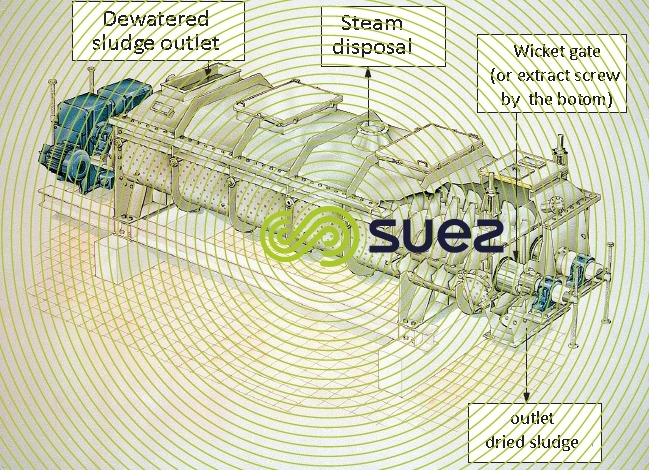

This dryer works during the sludge's high viscosity phase and takes advantage of its breakdown to form and mix together the granules and finer particles produced. Depending upon the final destination of the dried sludge, it may shaped into pellets afterwards (pelletisation).
In its steam version, this dryer is made from tungsten carbide coated stainless steel. In its thermal oil version, the trough is in stainless steel along with the wear plates, but the blades are made from high manganese content steel.
A standardised range of dryers exists ranging from an exchange surface area of between 3 to 300 m2. Being an indirect dryer, the specific evaporating capacity that can be expected ranges from 12 to 20 kg H2O·h–1·m–2 depending on the sludge's origin. Primary sludge is ranked in the lower part of the range and biological sludge in the upper part of the range.
the thin layer dryer (figure 10)
This is a cylindrical dryer with a twin skin outer casing within which the heat exchange fluid circulates. This fluid is usually thermal oil. Therefore, this is an indirect dryer without intensive recirculation. The horizontal cylinder houses a rotor equipped on the circunference with longitudinal bars that are in turn equipped with more or less tilted scrapers. The space separating the scraper from the inner cylinder casing defines the thickness of the thin layer (a few millimetres).
The rotor rotates more or less fast depending on the machine’s constructor (between 80 and 450 rpm); the higher the speed, the more carefully the system has to be constructed (abrasion, vibration…).
On its own, this dryer cannot produce a high dry solids content; drying has to be supplemented by a second stage which, depending on the constructor concerned, will be indirect (Buss) or direct (Innoplana, Vomm).
This type of dryer (excluding Innoplana) normally has to be followed by a specific dry product shaping stage. (Thermylis 2S, see product file).

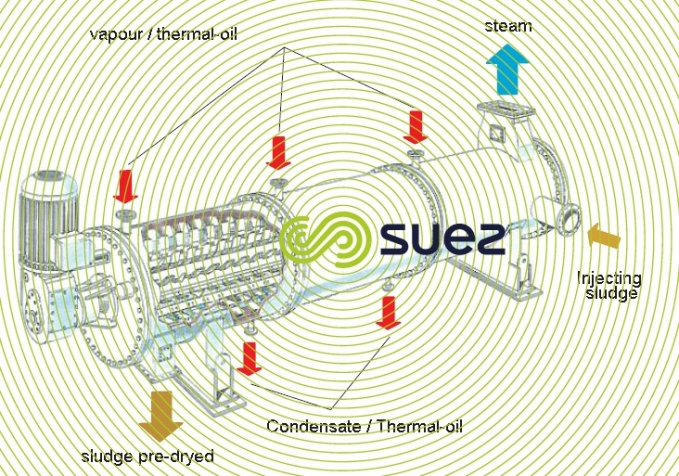

intensive recirculation dryers
the drum dryer
This dryer is a single or multi-pass dryer. This drum comes after a combustion chamber where the air in the thermal loop is heated and O2 depleted by the presence of combustion products and by the vapour generated as the sludge water evaporates (figure 11).
This dryer technology can only work correctly if the sludge entering the dryer is pre-granulated and has a dry content higher than 65% DM. Therefore, intensive recirculation of a portion of dried sludge with raw sludge is necessary in a specific mixer/granulating machine. In terms of operation this is a difficult stage.

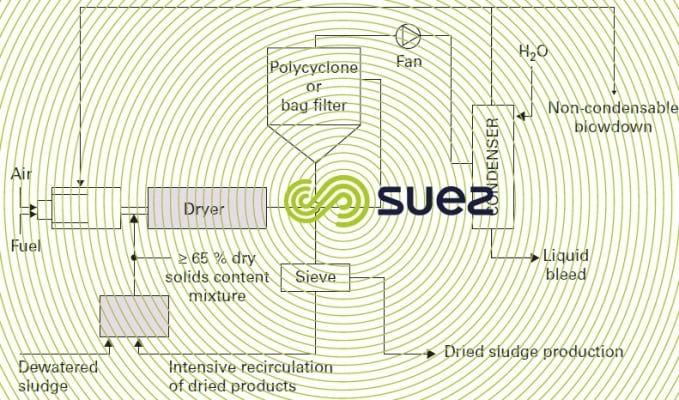

This type of dryer has an extensive range of capacities (5 to 15 t·h–1 of water evaporated). Refer also to the El Trebal Mapocho wastewater treatment plant (Chile) .
Abrasion in the dryer must be managed. A large quantity of fines is produced. To recover this fraction, a pellet-making machine is often used.

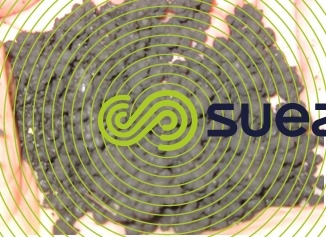


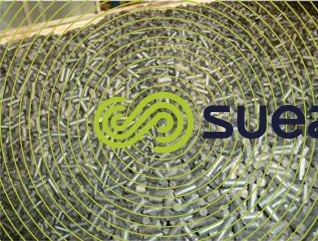

horizontal disc dryer (figure 12)
The dryer has a cylindrical stator, the outer casing of which is double-walled, inside which either a heat exchange fluid, thermal oil or saturated dry steam circulate. It also includes a tubular rotor along which hollow discs are attached. The heat exchange fluid circulates inside the double-walled stator, the shaft and rotor discs. The blades and the counter-blades arranged on the discs and the stator ensure that the sludge moves forward during drying. The rotor's low rotational speed protects the dryer from any abrasion.
This type of dryer does not allow high dry content levels to be achieved except when sludge is intensively recirculated with raw sludge in a specific mixer (difficult operation).
A range of dryers complying to a normative standard exist, with exchange surface areas of between 25 to 500 m2. As for all indirect drying, the evaporation capacity is directly related to the type of sludge to be treated (heat transfer ratios are not identical for biological and less fibrous primary sludge). The specific evaporating capacity which can be expected ranges from 7 to 15 kg H20 h–1·m–2 depending on the origin of the sludge.
Primary sludge is found in the lower part of the range and biological sludge in the upper part of the range.

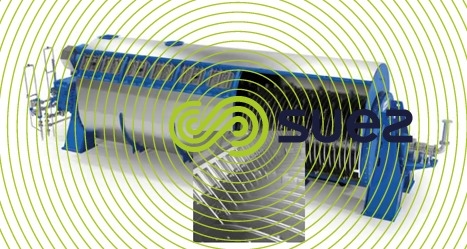

This dryer technology can be used for pre-drying dewatered sludge prior to incineration (Thermylis 2S, see Product file).
Bookmark tool
Click on the bookmark tool, highlight the last read paragraph to continue your reading later
