hydraulic piston press – the dehydris twist workshop
Reading time:general presentation of the piston press
The hydraulic piston press is an apparatus used to separate solids and liquids via pressure filtration.
It is different from the filter press owing to its dynamic pressing technology which permits it to obtain sludge with a high level of dryness without adding lime. Dryness values, which are higher than those obtained using a filter press, are close to those obtained by a standard dryness value test.
The other characteristic of the piston press lies in its automatic functioning, including during the emptying of dehydrated sludge.
principle of the piston press
The piston press is namely composed of a large dimension pressing chamber consisting in a cylinder (1) and a piston (2). The chamber is equipped with a cluster of flexible drainage elements (3) whose main function is to collect the filtrate resulting from sludge pressurisation performed by the piston connected to a hydraulic cylinder (4).
The piston press is batch operated with discontinuous feeding (or cycles). The cycle is composed of 3 successive phases: feeding, pressing and emptying.
The pressing chamber rotates around its main axis, guided by bearings (6) and driven by a gear motor (5).
On start-up, a pump fills the chamber with conditioned sludge via its inlet (7). During pressing, the filtrate is collected by the drainage elements and then fills the filtrate chamber (8) before being evacuated by piping (9). Dehydrated sludge is emptied by gravitational force, once the cylinder is opened.

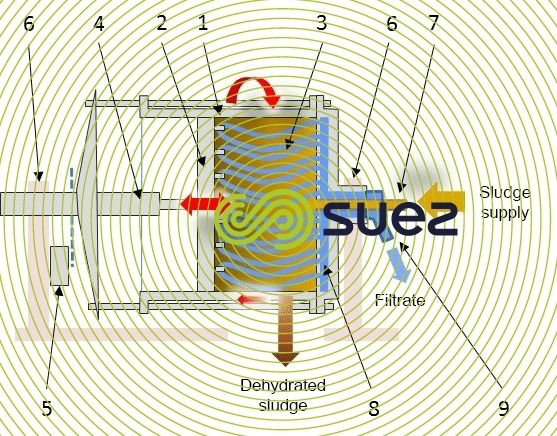


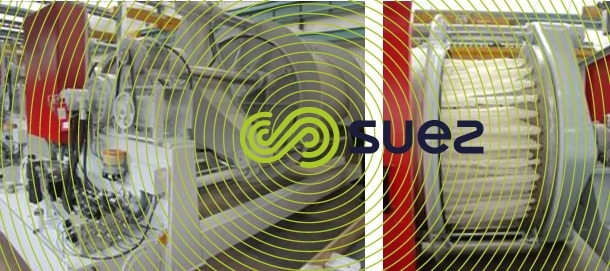


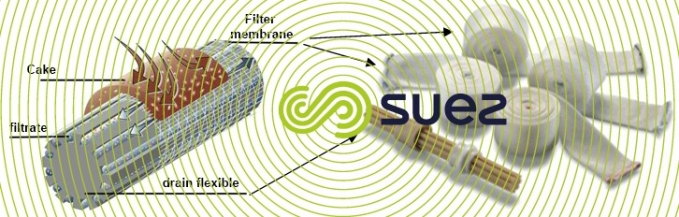

During the entire cycle, the pressing chamber rotates whilst the piston moves back and forth in the cylinder.
On start-up, conditioned sludge is fed via pumping sequences which are synchronised with the return stroke of the piston.
As soon as the chamber is full, the piston, via the hydraulic cylinder, applies a pressure to the sludge which is progressively increased during the pressing phase.
The drainage elements collect the filtrate and, driven by the rotation of the chamber and the translational motion of the piston, with depressurization of the sludge with every return stroke of the piston.
When pressing is completed, the cylinder casing slides along the machine axis to open a part of the pressing chamber and empty the dehydrated sludge.
The complete cycle takes approximately 2 hours. The duration depends on the characteristics of the sludge, its aptitude for filtration and the desired performances.
functioning of the piston press
Before being admitted into the hydraulic piston press, the concentrated sludge (25 to 100 g/l) is conditioned using one or several mineral reagents and / or polymer flocculation with the help of a dynamic mixer.
On start-up, the pressing chamber is closed. The cylinder-piston set begins to rotate before the piston begins to move back and forth in the cylinder.
feeding and pre-pressing (figure 48)
Before being admitted into the hydraulic piston press, the concentrated sludge (25 to 100 g/l) is conditioned using one or several mineral reagents and / or polymer flocculation with the help of a dynamic mixer.
On start-up, the pressing chamber is closed. The cylinder-piston set begins to rotate before the piston begins to move back and forth in the cylinder.

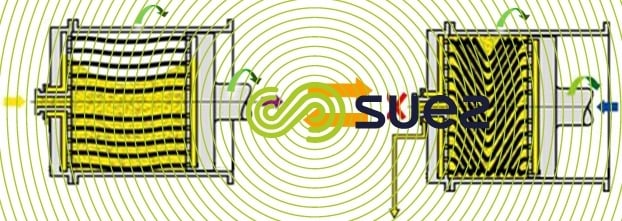

The feeding phase is controlled by instrumentation (determination of the quantity of dry matter admitted and measure of the filtrate flow rate) as well as by automation parameters.
pressing and de-structuring (figure 49)
This phase is characterized by a series of back and forth movements by the piston and with a progressive increase in the pressure applied to sludge. The drainage elements driven by the various movements result in sludge de-structuring. This loosening of sludge permits free water to be released and extracted during the subsequent pressing sequence.

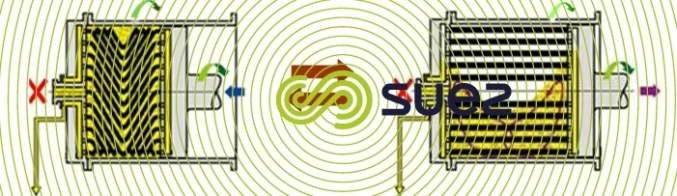

When the piston reaches its maximum extension, or the filtrate flow is at its minimum for several cycles of the piston, the pressing phase stops.
emptying phase (figure 50)
As soon as pressing is completed, the emptying of the press begins with the progressive opening of the cylinder whilst the cylinder / piston set continues to rotate. The pressing chamber is progressively emptied with the movements of the piston and the drainage elements which release the dehydrated sludge.

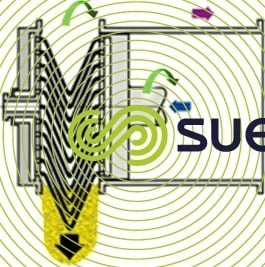

Dehydrated sludge is collected in a hopper and an auger screw installed under the cylinder. The press is emptied over a fixed duration, the pressing chamber is then closed and a new cycle can begin.
The following diagram illustrates the progression of the piston press operating cycle.

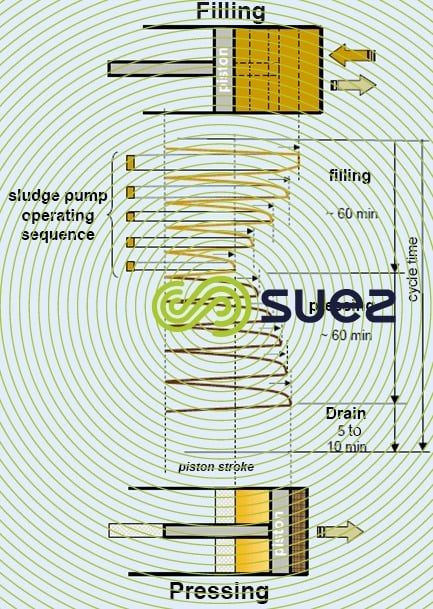

weekly washing and de-scaling
The inside part of the pressing chamber is automatically washed using water once per week.
The de-scaling of drain membranes using an acidic solution followed by rinsing can be necessary in the event of sludge being conditioned using lime. Its frequency depends on the characteristics of the sludge and the rate of liming applied.
dehydrisTM twist unit
DehydrisTM Twist (photo 30) is SUEZ advanced dewatering unit which uses a hydraulic plug flow press made by Bücher Unipektin.

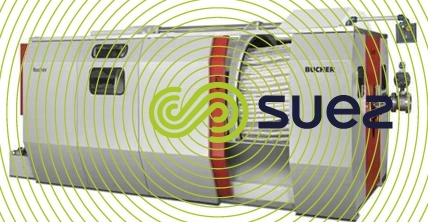

The unit is fitted with one or several plug flow presses which are available in 4 sizes.
Treatment capacity varies from around 200 kg of DM per cycle for a small-sized press (operating volume of 3,3 m3) up to 1600Kg of DM for the largest model (operating volume of 12 m3).

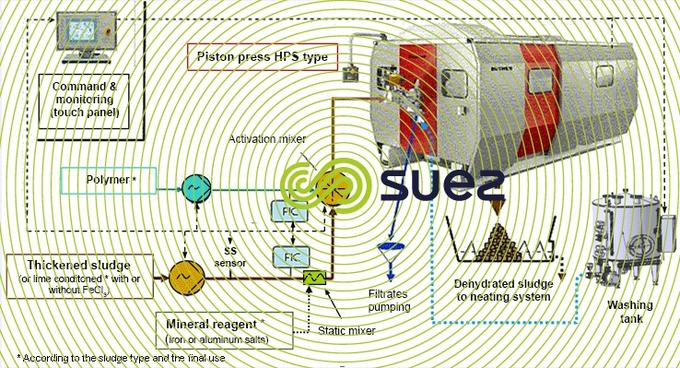

The unit includes all the peripheral equipment necessary for plug flow press operation:
- a sludge conditioning unit using polymers with or without mineral reagents, with an active mixer incorporated (conditioning using lime is also possible)
- a device to handle dewatered sludge, generally comprised of a screw
- a drain washing and de-scaling system
From sludge feeding stage to the handling of dewatered sludge, the unit is entirely automatic. Generally, the unit's operational availability is 8000 hours/year.
To compensate for occasional surges, two operating modes are possible with one focusing on maximal dry content at nominal flow rate and the other operating at a higher flow rate with lower dry content.
Electricity consumption (plug flow press + sludge pump) is around 45 to 90kWh/tDM, and is a function of the sludge's ability to be filtered and the results required.
DehydrisTM Twist can be used for residual urban or industrial sludge, sludge resulting from drinking water production and from seawater treatment.
sizing
Sizing is related to the following information:
- The type of sludge and quantity of DM/SS to be dewatered.
- The final dry content required
- The unit's operation (hours per day, days per week, weeks per year)
Following the determination of the number of cycles in accordance with the unit's operating time and the load per cycle, the press' overall operating volume is calculated using the weight of the loads (between 70 and 110 kg DM/cycle * m3 of press operating volume for residual urban sludge).
The number and operating unit volume of plug flow presses can then be calculated knowing that 4 sizes of plug flow presses are available with operating volumes of 3.3, 6, 7.5 or 12 m3.
results achieves
The results achieved in terms of sludge type and conditioning are summarised in the tables below:

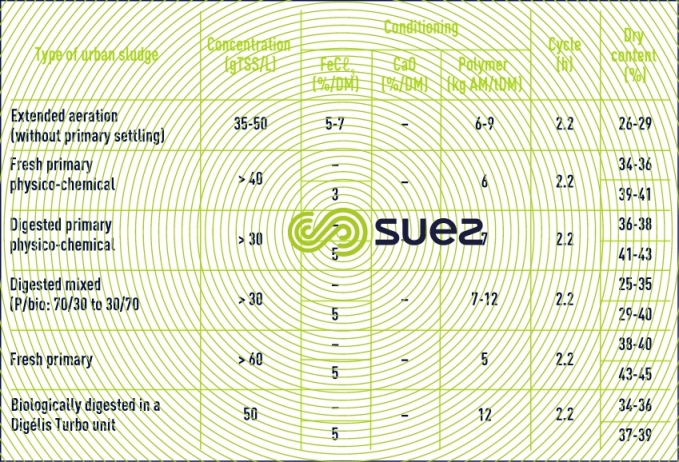


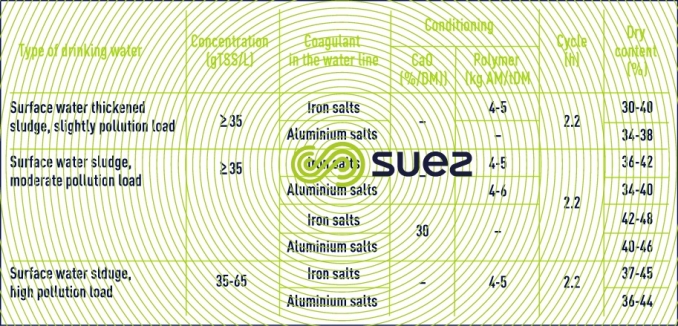


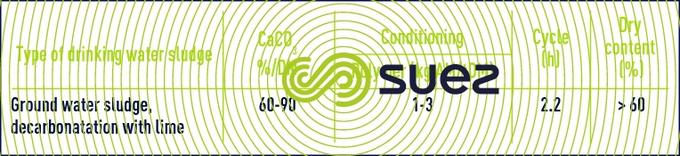


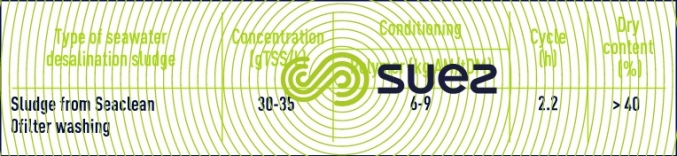

In operations,
- the high results obtained from the plug flow press with different types of conditioning, widens the choice of solutions for the final destination of sludge
- where urban wastewater sludge is incinerated, the dry content obtained when combining DigelisTM Turbo and DehydrisTM Twist units increases the self-heating properties of sludge, resulting in OPEX savings.
- the unit's flexible operation allows occasional surges in load to be alleviated by a flow rate which may be 30 to 50% higher than the nominal value, at the expense of dry content values.
Bookmark tool
Click on the bookmark tool, highlight the last read paragraph to continue your reading later
