degremont® range
Reading time:There are two available filter belt types (Superpress LP and HP) available for use with the major sludge groups (organic, mineral...) that will withstand more or less pressure. Another version of these same filters that incorporates pre-thickening using GDE or GDD, is available, and a simplified version, the GD Press, is use for small plants.
the superpress LP and HP filters
According to the objective set and to the quality of the sludge to be dewatered, several filters are available.
superpress LP
This version is suitable for dewatering sludge produced by WWTP and by agri-food industries that does not usually withstand high pressures.
Figure 26 provides a schematic diagram of the Superpress principle in its basic version without GDE or GDD.

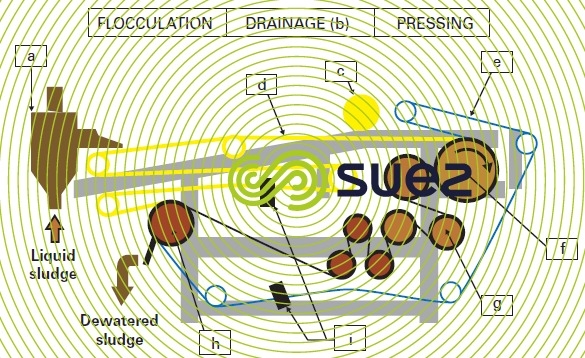

The sludge and the flocculant are fed into a mixer (a) fiited with a variable speed stirrer. The flocculated sludge is flowed onto a filtering belt in the drainage roller (b).The sludge is evenly distributed over the entire width of the filter.
In this drainage zone, the sludge layer raked and then formed into an even and homogenous blanket by a roller (c) designated the draining roller. This roller is used to:
- insert an even sludge layer into the pressing zone (between 10 to 40 mm variable thickness depending on the positioning preset by the operator);
- and, above all, to carry out first-stage sludge compacting in order to reduce lateral squeezing out at the start of the pressing zone.
The sludge is then sandwiched between the lower belt (d) and the upper belt (e), undergoing a first moderate pressing round a large diameter perforated drum (f).Both belts are continuously driven and then pass between a series of decreasing diameter return rollers (g) that apply a gradually increasing pressure to the sludge. The number of windings is selected so that dewatering is virtually completed before the sludge reaches the final roller.
At the outlet, both belts separate after the drive roller (h). The cake is removed by two scrapers blades for discharge by a conveyor belt, transfer screw or force-feed pump.
A pneumatically controlled, angular travel roller automatically centres each of the belts. Both (large mesh) belts are washed continuously by pressurised water (4-6 bar) sprayers within closed compartments (i).
Simple adjustments are required to adapt filter operation to sludge properties:
- adjustable pressure pneumatic cylinders are used to adjust belt tension (filtration pressure);
- belt drive speed can be modulated between 1 and 5 m · min–1;
- flocculation energy can be adjusted by altering the speed of the flocculator agitator;
- sludge layer depth can be adjusted at the pressing zone feed.
The Superpress filter frame has been designed to ensure:
- a good overview of the drainage zone;
- easy access to mechanical devices;
- potential belt widths ranging from 1 to 3 m.
Available options:
- GDE or GDD thickener screen incorporated into the drainage zone see;
- pre-drained sludge is possible to discharge as very thickened sludge with the GDE/GDD LP Superpress couple;
- six additional pressing rollers;
- self-cleaning belt wash sprayers;
- set of operation assistance sensors;
- integral enclosures (photos 19 and 20).
superpress HP
This version differs from the preceding version through the higher pressure applied to the sludge. Therefore, the overall design has been adjusted accordingly (especially the reinforced frame); this version has also been designed for processing aggressive sludge (reinforced anti-corrosion treatment).
GDE or GDD + superpress (figure 27)
By incorporating a GDD or a GDE (see dynamic thickening) onto a Superpress, high dry solids contents is obtained at the inlet of the dewatering module, irrespective of sludge dilution (> 2 g DS · L–1), thus very noticeably increasing the throughput treated without compromising the mass flow rate.
Table 13 illustrates the benefits of incorporating additional pre-draining, by GDE or by GDD, upstream from the Superpress drainage zone.

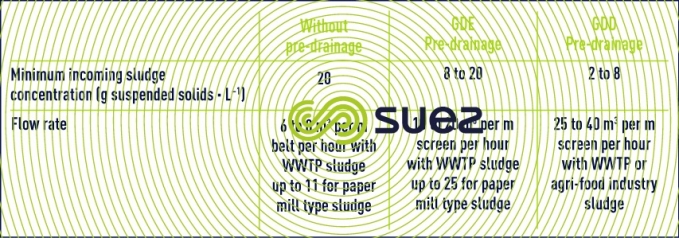

GDE or GDD/Superpress appliances have further advantages:
- GDE/Superpress: sludge is extracted direct from the recirculation of an activated sludge system. This approach allows us to eliminate static thickener silos and to process unfermented sludge, producing better dry solids content:
- the GDD/Superpress unit makes for even more reliable operation of the dewatering system: extracting sludge from the aeration tank overcomes any danger of anaerobiosis (no release of phosphorus) and ensures a constant infeed concentration and sludge flocculation steadliness (can operate unmanned, optimised reagent consumption);
- in either case, a mechanism allows sludge to be removed direct from the pre-drainage outlet (for periodic thickened sludge spreading for instance).

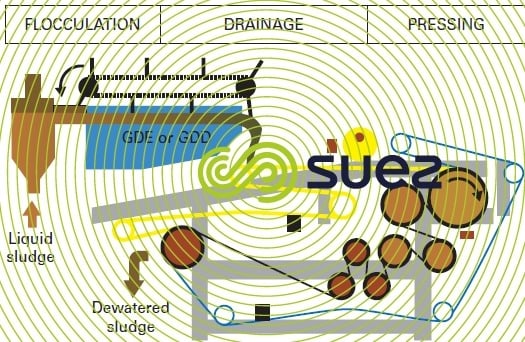

the superpress range (table 14)

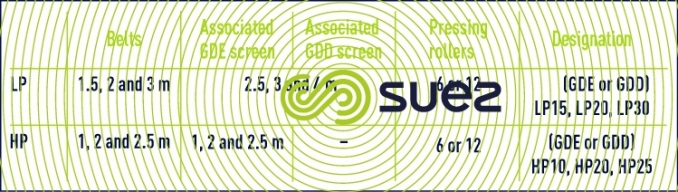

superpress performances
Table 15 provides approximate performance magnitudes for the different Superpresses used with various sludge.




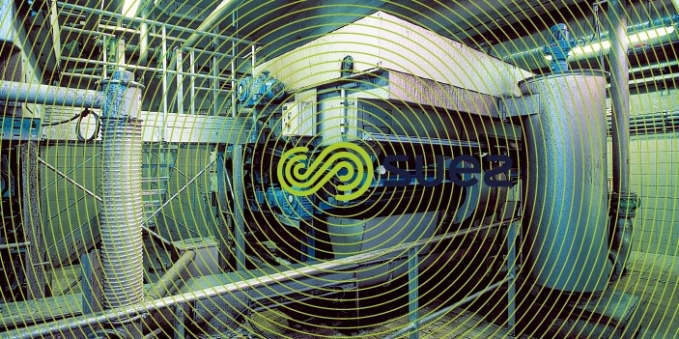


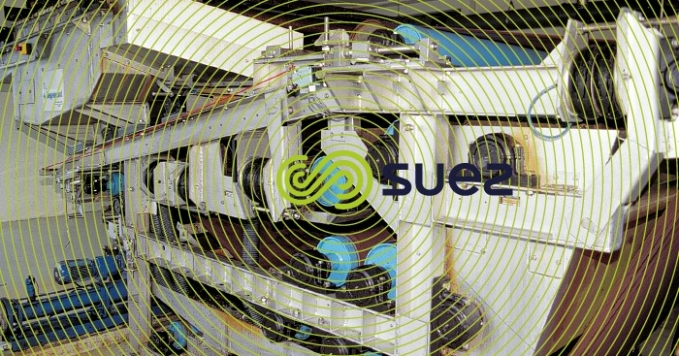

the GDPress: a belt filter for the smaller plants
This is a compact unit comprising a thickening module (GDE or GDD) and a simplified perforated drum + only five-roller pressing module (figure 28) only. These robust machines are wholly constructed of stainless steel and require very little operating and/or maintenance time. In particular, as is the case with all Superpress filters, they can be programmed to shut down (or for remote starting) without any need for supervision.



908D and 912D type machines can therefore be fed direct from aeration tanks, thus making a sludge storage tank or thickener superfluous.

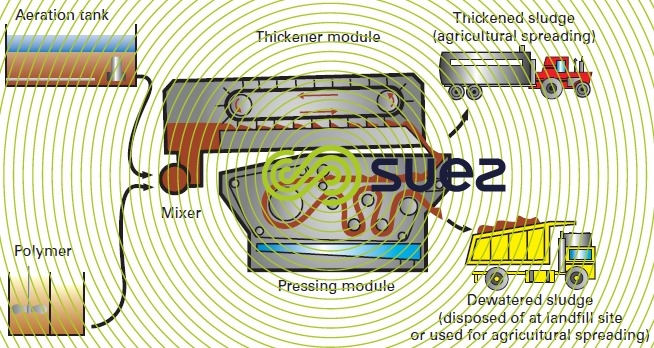

Bookmark tool
Click on the bookmark tool, highlight the last read paragraph to continue your reading later
