heat treatment
Reading time:Bringing sludge up to the right temperature (180 to 200 °C) for 30 to 60 minutes results in an irreversible change to its physical structure, significantly reducing its specific resistance, especially when it contains a high proportion of organic matter.
As sludge is heated, the colloidal gels are destroyed, particles hydrophilic effect declines sharply and particle density becomes significantly higher. We also witness two simultaneous phenomena:
- the solubilisation of some suspended solids;
- the precipitation of some substances in solution.
Cellulose is slightly degraded and fats remain relatively stable.
Depending on the type of sludge, heating will render soluble 20 to 40 % of OM and, therefore, result in the production of interstitial liquor containing 3,000 to 6,000 mg · L–1 of BOD5 (COD/BOD5 ratio in the region of 2.5). The highest figures are obtained when heating fresh sludge. This solubilisation increases with temperature and with heating time.
Nitrogen is present in the liquid phase in relatively high amounts (0.5 to 1.5 g·L-1 as NH4+); phosphorus, however, together with metals, remains precipitated in the sludge.
advantages of heat treatment
On larger plants, selecting this type of conditioning can become attractive because:
- it improves sludge structure, making it possible to carry out filtration without adding reagents. Temperature has an overriding effect on filtration capacity; heating time of over half an hour will be enough;
- filter cake very high dry solids content (usually more than 50 % DM which is far higher than that produced by chemical conditioning);
- dewatered, sterilised sludge production without any added reagent; this sludge can easily be disposed of in soil;
- optimum biogas utilisation; the combination of anaerobic digestion and heat treatment still constitutes one of the most attractive process for large plants (> 1 million inhabitants);
- performance stability (not very susceptible to fluctuating concentrations);
- major and rapid thickening after heating.
restrictions on use
However, heat treatment effectiveness is occasionally subject to the following constraints:
- «liquor» has to be recycled to the plant inlet: there is a BOD5 overload of approximately 10 to 25 % - this pollution is mostly soluble, rich in nitrogen and containing a fraction of hard COD (through the aerobic or anaerobic process), that can even be inhibiting (anaerobiosis);
- odour emission: heated sludge gives off a lot of odours; these odours must absolutely not be released into the atmosphere (need to cover structures over, for ventilation and odour control) and final cooling for heated sludge must be provided;
- heat exchange surface areas need to be cleaned at regular intervals: in particular, prohibiting the process from being used on sludge that have a high calcium level.
setting up sludge heating
Figure 14 provides the most frequently used operating schemes. In all cases, the aim is to recover as many calories as possible from the heated sludge to the sludge that is to be heated so that the external heat required only represents a warming up for 40 °C. This recovery is achieved by concentric tubular exchangers with counter current low. A separate reactor is always useful to ensure a minimum heating time and a well checked temperature.
Heat is supplied:
- either direct with live steam inside the reactor (Cotherma system);
- or through indirect heat exchange with a non-vaporisable heat exchange fluid such as oil: this is the Cothermol system.

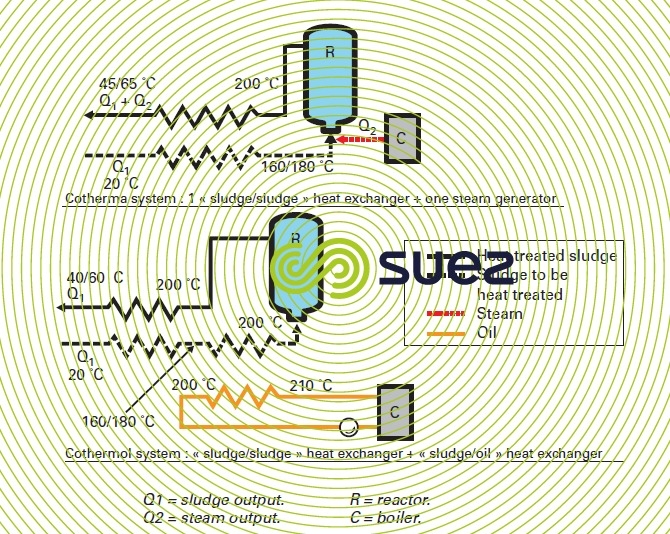

Providing that operation is well monitored and that there is an adequate exchange surface area, energy consumptions will fall within the following limits:
- direct live steam injection: 60 to 90 kWh · m–3 of sludge;
- indirect injection via a heat exchange fluid: 40 to 70 kWh · m–3 of sludge.
Experience has shown that this process is extremely efficient and reliable when used:
- in large WWTP (reactor capacity greater than 30m³);
- on digested sludge

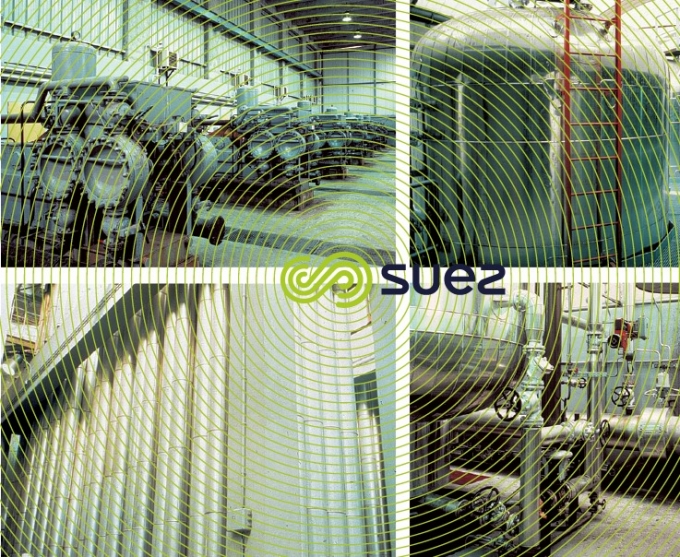

Table 6 summarises the different treatment options (discussed in chemical conditioning and heat treatment) upstream from several dewatering technologies.

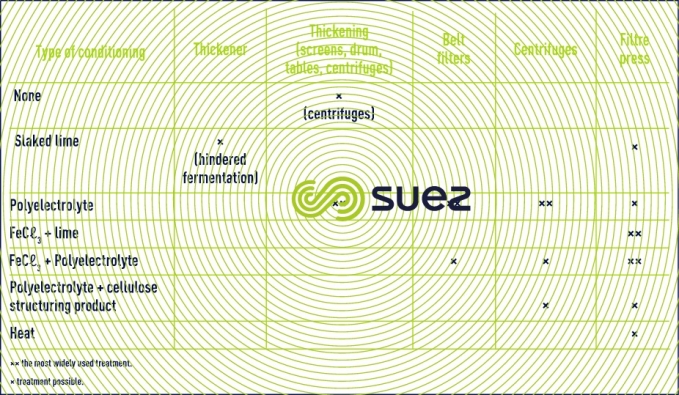

Bookmark tool
Click on the bookmark tool, highlight the last read paragraph to continue your reading later
