setting up
Reading time:Pre-treatment: there is no longer any need (save in exceptional cases involving certain industrial sludges) to carry out bar screening/straining or grit removal in order to protect the centrifuges. In effect, bar screens that have recently been installed on plant inlets (often 3 to 10 mm) and high performance grit removal units (90 to 95 % of grit over 200 mm removed from raw water) afford perfectly adequate means of protection. With most sewage sludge, screw longevity of 15 000 hours is now quite common due to the important progress achieved in the field of anti-abrasion coatings.
Infeed: the machine must be supplied with a constant flow rate (progessive cavity pump or lobe pump) if we want to produce a regular recovery rate.
Protection against noise: the noise level of a machine running under nominal conditions will frequently be between 85 and 90 dB(A) and, consequently, incompatible with prolonged operator or maintenance technician presence. Therefore, either the room has to be acoustically insulated and the operating personnel provided with a noise protective headsets or the machine must be hooded to that the noise level falls about ten dB(A).
Vibration phenomena: all rotating machines create vibrations, quite weak under stabilised operating conditions, but occasionally high in temporary operating conditions such as starting up and stopping. Therefore, the centrifuge must be isolated: flexible seal on the machine intake, flexible seal on the centrate discharge, flexible seal on the cake delivery hopper and powerful shock absorbers under the frame. In stable operating conditions, 5 mm · s–1 vibrations are regarded as normal. They must not exceed 15-20 mm · s–1 because they can cause serious damage above this level.
Liquid discharge during start-up and shutdown (figure 30): as the liquid ring diameter is usually smaller than that of the cone discharge (in the case of the high pressure centrifuge), it is impossible to prevent liquid discharging on the sediment side when starting or shutdown flushing. A slide valve then has to be inserted on the cake discharge to send the liquid towards the general centrate pipe; its working will depend on the value of the torque applied.
A simpler solution could be st up with a sloping screw, with an opening downwards, positioned immediately below the machine's sediment casing (figure 37).

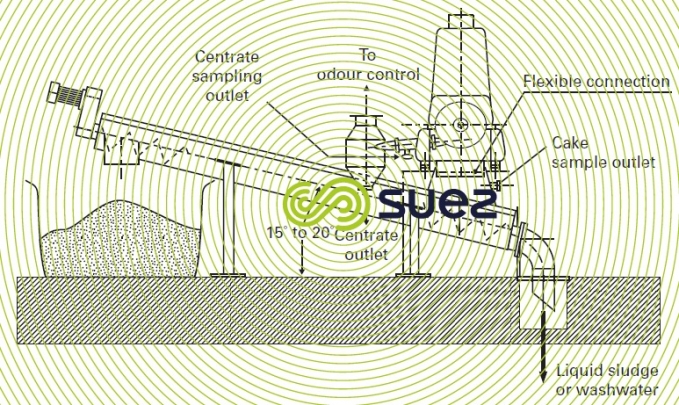

Power consumption: the following average consumption levels were recorded for pre-thickened sludge (table 19):

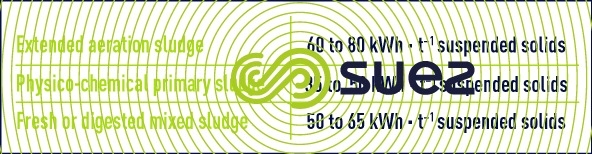

Odour collection: a degassing outlet must be installed in the centrate discharge casing and routed to the plant’s odour control facility. The sediment outlet must be closed. A centrifugation unit will only require minor ventilation compared with other dewatering units.
Maintenance and overhaul: maintenance and overhaul operations must be carried out by qualified worker. If mechanical damage happen to the screw or on the rotor, rebalancing will be required after repairing.
Operation: sludge is not visible while it is being processed and, therefore, we need to interpret any unsatisfactory result and react accordingly (table 20); the first objectives consist in maintaining:
- clarified centrate;
- acceptable dry solids contents while avoiding excessive amounts of polymer.

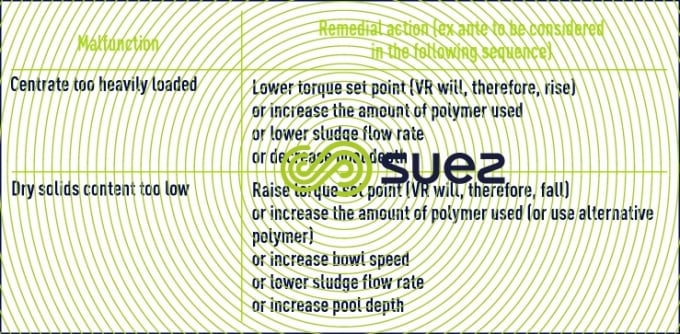

Bookmark tool
Click on the bookmark tool, highlight the last read paragraph to continue your reading later
