aluminium
Reading time:alumina production
Producing alumina through bauxite causticisation (Bayer process) generates asodium aluminate solution that contains bauxite ore impurities in suspension. This solution is clarified in scraped thickening tanks and a series of several washers is used in countercurrent mode to wash the bottom sludge (red mud); the washed sludge can be dewatered using vacuum belt filters (figure 57).

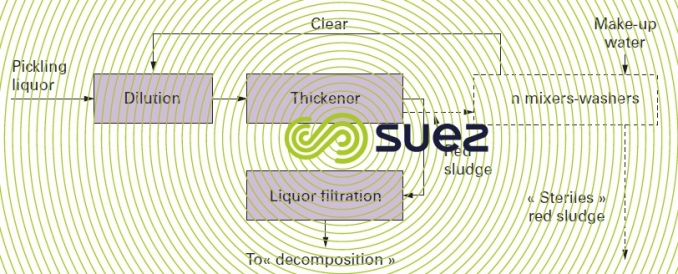

Generally this sludge will still be highly alkaline (1.5 to 6 kg of sodium hydroxide per ton of alumina produced) and will be lagooned on the plant’s site, with the supernatant then returned to the process.
Accordingly, the following will be the only effluents produced:
- cooling water and storm water; the latter may be contaminated by suspended solids (maximum of 0.03 kg per ton of Aℓ) and by soluble fluoride (maximum of 0.02 kg per ton of Aℓ). A treatment is then required to reduce fluoride by addition of lime and/or CaCℓ2 to precipitate calcium fluoride;
- condensates that are more or less heavily loaded with organic (volatile) matter. Also refer to the tables provided for the Gregory example under wastewater reuse for power plant make-up water
fluorinated water from alumina electrolysis
Gas produced by the electrolysis cells contains CO, HF, SO2, vaporised metals, dust, PAH. Therefore, the cells are closed and the alumina subjected to a dry purification treatment.
However, there are still systems that will use wet scrubbers for the gas contained beneath the roof. A sidestream system takes approximately 10% of the water from the main system for defluorination using lime and sedimentation in a Densadeg.
effluent from the manufacture of prebaked anodes
Current developments impacting this process have reduced the effluent to cooling water, the gas collected being treated through bag filters and/or electrostatic precipitation.
SSome plants still utilise wet scrubbers for gas treatment. In such cases, provisions must be made for tar removal by conditioned flotation using organic coagulants followed by fluoride removal by precipitating CaF2 with lime and/or CaCℓ2, and sedimentation in a Densadeg, for instance.
N.B. cathode frames and associated components (conductors, refractories, etc.) are recycled after separation via pyrometallurgical treatments.
Aluminium polishing by electrolysis does not create any effluent.
producing aluminium from recycled products
Aluminium foundries that utilise recycled metal (drinks cans, extrusion waste, casting off-cuts, recycled sections and even coarse dust generated by production processes) are equipped with melting furnaces that feed continuous casting or ingot mould systems.
In addition to the cooling water that is recycled in most cases, these units produce storm water that can be contaminated as it percolates through stocks of tailings, as well as water produced by continuous casting processes which contains emulsions that have to be “broken down” (see surface treatment (degreasing and metal coating)) and can then be combined with storm water for oil removal and clarification. Figure 58 illustrates the various treatment stages and pollutants.

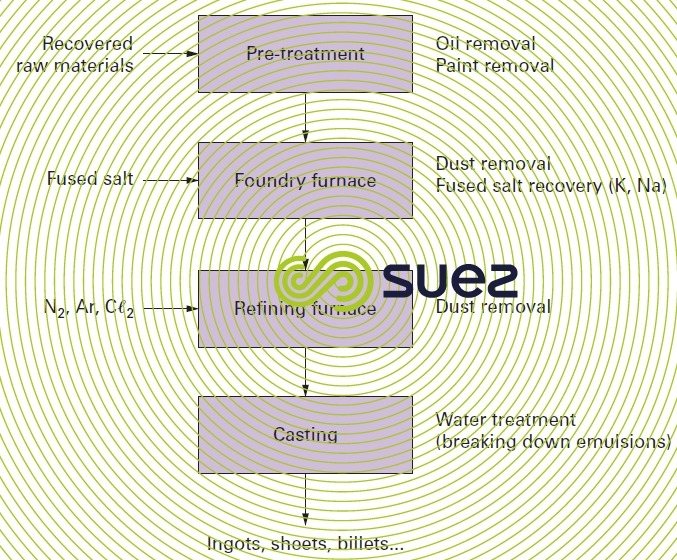

aluminium castings and hot rolling
Oils, dust and various contaminants concentrate in these systems have to be eliminated. The feed water must be softened or lightly mineralised; pH must be maintained within a non-corrosive range and the feed water must undergo oil and suspended solids removal before being recycled.
In hot rolling applications, effluent usually consists of a true emulsion and, consequently, system blowdown must be de-emulsified… (see surface treatment (degreasing and metal coating)).
Figure 59 illustrates the conventional layout of this type of system.

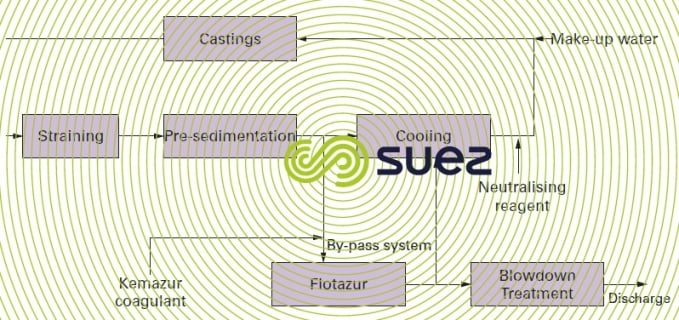

Bookmark tool
Click on the bookmark tool, highlight the last read paragraph to continue your reading later
