zinc and lead
Reading time:roasted “zinc sulphide” effluents
This hydro-metallurgical process accounts for approximately 80% of the world output of zinc.
Sulphurated, oxidised, carbonated and silicated ores are screened and then dissolved in sulphuric acid. They are refined using electrolysis.
After recovering any selenium, mercury and, above all, cadmium, effluent is routed to a two-stage neutralisation employing lime; this process takes place in a structure that also receives acid liquors and wash waters. Solids contact clarification with desaturation is then required to precipitate fluorides and calcium sulphates. The supernatant is then sent to the plant’s general wastewater treatment system.
We need to be aware of a “pyrometallurgical” method that only “consumes” cooling water.
general effluents
In plants where a major part of the process is carried out by acid leaching, most effluent is pre-treated directly in the units. Final effluent is diluted but of substantial volume. This effluent is treated by neutralisation and sedimentation in one single stage with the use of a Densadeg (photo 40) that will very efficiently reduce heavy metals to effluent concentrations (typically, Pb < 0.2 Zn < 0.5 Cd < 0.25 mg) in the Densadeg effluent.

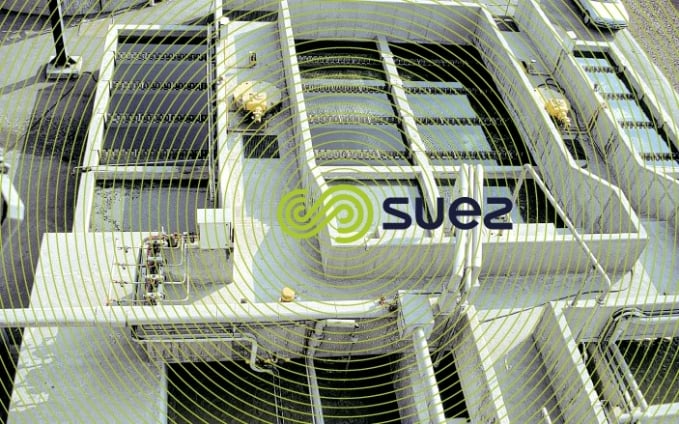

Recycling of these effluents without any other treatment is viable for various wash applications or processes that will tolerate water that has a fairly high salt content; more complete recycling can be possible if membrane treatment is applied.
the lead metallurgy workshop
Here again, we have two production methods: a pyrometallurgical method that consumes little water and where gas containing SO2 is scrubbed; and a hydrometallurgical method characterised by leaching sulphur ores (PbS) before refining using electrolysis.
Acid effluents, hydro-washer blowdown and alkaline dechloridation wastewaters are clarified as they are produced; the sludge is recovered for recycling to the screening unit and the overflow is then routed to the plant’s general wastewater treatment system.
lead produced by recycling car batteries
This constitutes a major proportion of output.
On average, these batteries have the following composition (table 44):

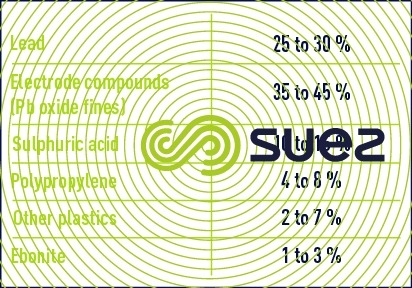

They are drained of their acid, broken up and sorted. The lead is then processed using various processes before being melted and refined.
The waste streams are:
- extremely acidic and contain high levels of sulphates in the case of those produced from battery drainage and floor washing;
- very alkaline and in very small quantities are the “Pb compound” drips before the compound is sent for lead recycling; these drips have high levels of sulphates and COD.
This effluent is neutralised using lime and sludge recycling to precipitate the calcium sulphate before being clarified in a typical sedimentation unit or a Densadeg, depending on the case. It may be necessary to add calcium chloride with the lime in order to achieve adequate gypsum precipitation because pre-neutralisation using sodium carbonate is common practice in this industry.
(please refer to chemical precipitations).
If this effluent is not too saline, it could be recycled subject to undergoing reverse osmosis.
Bookmark tool
Click on the bookmark tool, highlight the last read paragraph to continue your reading later
