copper
Reading time:At the mining site, the ore is normally pre-concentrated by flotation and chemical addition; blowdown and discharge from this process will normally be handled at the mine site (see mining industries), concentrates are then processed for metal to be extracted using one of two techniques.
pyrometallurgy
This process consumes little water, mainly for cooling and treating gases and fumes that contain high levels of SO2 which is generally linked to the production of sulphuric acid.
Copper is prepared by roasting, melting and casting. The metal bar obtained is placed at an electro-refining anode in order to obtain an extremely pure copper cathode (consuming approximately 250 kWh · t–1 Cu). This unit produces little in the way of discharge, mainly residues from the electrolysis, bottom and floor cleaning sludge.
hydrometallurgy
This treatment processes pre-concentrated ores in bulk by acid or acid/oxidising agent leaching. The solution is recovered either directly or after a cascade wash/clarification.
Most of the time, purification/concentration is carried out by selective precipitation of impurities. It is at this stage that recyclable impurities are recovered.
There are also instances of liquid-liquid extraction purification systems.
Production then takes place by electrowinning: the copper extracted is electrolysed using an inert anode (Pb or Ti) and a pure copper cathode. This process consumes 2,500 to 3,000 kWh · t–1 of copper produced.
The copper is deposited on the cathode and the gases produced at the anode (O2, Cℓ2) are recovered selectively and returned to the process.
This method produces an extremely pure copper that can then be rolled (hot or cold), drawn or even formed into tubes before being sold.
Wastewater treatment is extremely important in these factories. It includes:
- storm water falling on roofs, paved areas and the piles of tailings;
- acid gas wash water containing high levels of SO2;
- residual effluent produced by strong acid leaching;
- the factory’s industrial waste effluents (granulates, various pickling processes, electrolysis residues…).
They undergo several different types of treatment (figure 60); gas scrubbing products are processed by the plant, producing valuable sulphuric acid for use in lixiviation. Acid effluents are neutralised with lime to precipitate gypsum (which can be recycled if necessary) and then clarified in the conventional manner. Wastewater and storm water effluents are also neutralised using lime. Overflows from the acid treatment settling tanks are added, and all is then clarified once more at optimum pH in order to remove various heavy metals in a clarifier/sludge thickener such as the Densadeg.
A final filtration may be required to remove suspended solids and traces levels of metals by adding a polymer or precipitation agent.
It is quite possible to recycle this effluent (25 to 30%) for other applications in the plant which require lesser water quality; a more thorough tertiary treatment can be included for greater recycling efficiency.

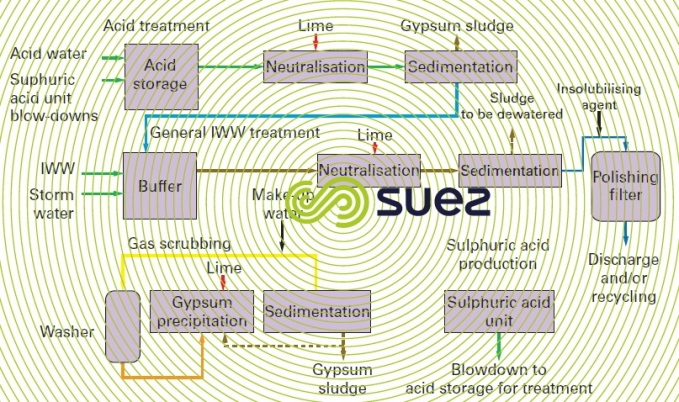

Bookmark tool
Click on the bookmark tool, highlight the last read paragraph to continue your reading later
