sludge produced
Reading time:All the precipitation reactions described in the foregoing produce sludge that can be divided into two major categories:
- granular sludge formed by crystals measuring from a few µm to a few tens of µm: CaCO3, CaSO4 2H2O, CaF2, Ca3(PO4)2…;
- metal hydroxide sludge to which can be added precipitates containing silica (amorphous).
The former will retain little water and, therefore, present major static thickening possibilities (several hundred kg · m–2 · h–1) when it is pure; for instance, carbonate removal sludge containing over 95% of CaCO3:
- will thicken up to approximately 200-400 g · L–1;
- will dewater on a belt filter up to more than 50% dry solids content and, in this case, care has to be taken due to the possibility of pipe blockages if the system is stopped (e.g. intermittent extraction of this sludge, scraper mechanism shut down…).
On the other hand, if this same granular sludge contains a certain proportion of hydroxides (Fe(OH)3, Aℓ(OH)3, Mg(OH)2 …), to which can be added any silicates that have precipitated, their suitability for thickening and dewatering decreases sharply: in the above example, limit thickening will occur in the region of 60-80 g · L–1 if we introduce 10% of magnesium hydroxide and 25-30 g · L–1 when we have 30% Mg(OH)2.
Pure hydroxide sludge behaves only marginally better (case of Fe(OH)3 Cu(OH)2) than excess activated sludge whereas Aℓ(OH)3, Zn(OH)2 behaves almost identically, Mg(OH)2 being the worst.

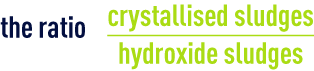
will therefore constitute the basis of any equipment sizing (see also sludge section and chapter liquid sludge treatment).
Bookmark tool
Click on the bookmark tool, highlight the last read paragraph to continue your reading later
