precipating silica
Reading time:This involves adsorbing silica over an Aℓ or Mg hydroxide floc. This co-precipitation can be carried out under hot or cold conditions. It is often carried out at the same time as CaCO3 precipitation for carbonate removal.
silica removal using Mg2+
When magnesium is present in well water and when its pH level is adequate, it will precipitate with some of the silica when carbonates are being removed. Mg can be topped up using MgO powder in cold conditions when MgO will solubilise through carbonation to form MgCO3. We can also add a chloride or sulphate Mg salt.

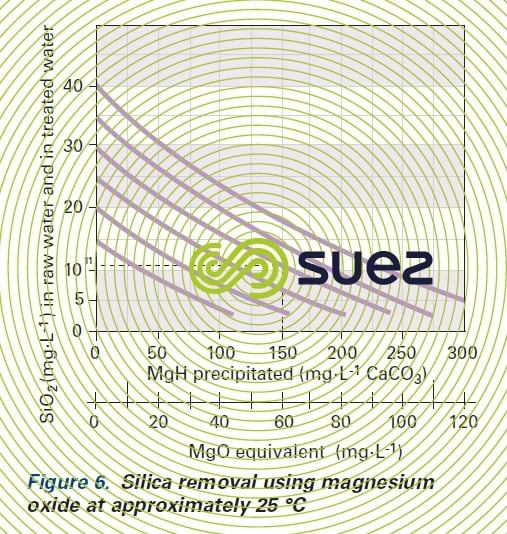

Depending on raw water analysis, target temperature and abatement, graphs can be used to establish the amount of reaction MgO (figure 6) and, by calculating the difference, the amount to be injected.
Under cold conditions, this amount will vary from 3.2 to 1.8 mg of MgO per mg of absobed SiO2 for an initial concentration of 20 to 40 mg.L-1.
E.g :
- 150 mg · L–1 (as CaCO3) or 15 °F of MgH precipitated;
- raw water SiO2 content – 30 mg · L–1;
- treated water SiO2 content – 11mg · L–1;
- and if our target is ≤ 8 mg · L–1 of residual SiO2, we will need to add at least 25 mg · L–1 (as CaCO3) of Mg as reagents.
silica removal using sodium aluminate
This treatment should preferably be carried out cold (figure 7).
Residual levels achieved will be higher than with MgO.
The amount of aluminium, expressed as Aℓ2O3, used in brackish water will be approximately 2 to 2.6 mg per mg of silica coprecipitate.
When using lime and sodium hydroxide to remove carbonates from well water, the residual levels of SiO2 obtained will roughly be as follows for initial levels of 20 to 40 mg·L–1 of silicon (table 7).
The initial level of Mg in water, the cost of reagents and the amounts of sludge produced will be the deciding factors between these two reagents.

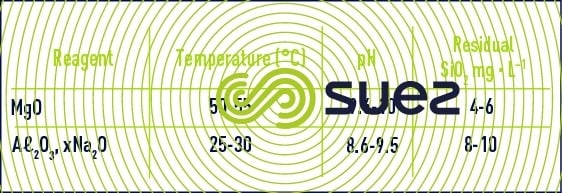

FeCℓ3 utilisation:
FeCℓ3 utilisation combined with the aluminate will enable us to achieve a 0.2 to 0.3 mg · L–1 residual aluminium at pH 8.-9 instead of 3 mg · L–1 with aluminate alone.

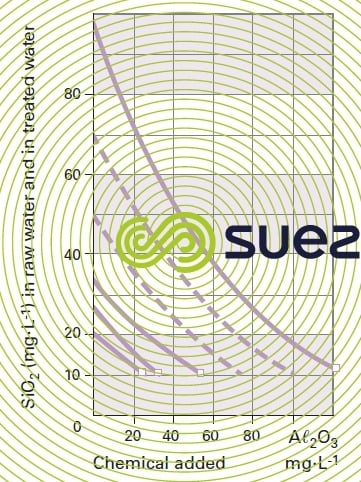

colloidal silica
Although it has a variable chemical nature, colloidal silica often consists of very fine particles (0.2 to 0.005 μm) of clay, occasionally polymerised silica.
Levels of a few hundred mg · L–1 are found in river water in temperate countries and can reach several ten of mg · L–1 in some tropical rivers, acid lixiviates produced by hydrometallurgical industries or oil formation water. This colloidal silica is not ionised and, therefore, is not properly eliminated by traditional systems used in the treatment of boiler water (clarification + ion exchange) (see chapter treatment and conditioning of industrial water) and poses severe problems (scaling, vapor quality…). Consequently, supplementary methods have been developed:
- twin flocculation at 2 different pH levels if possible for low colloidal silica values (< 1 or 2 mg · L–1) in raw water;
- filtering either clarified water or demineralised water through ultrafiltration membranes.
Bookmark tool
Click on the bookmark tool, highlight the last read paragraph to continue your reading later
