natural flotation and aided flotation
Reading time:natural flotation
Although in general we do not speak about “flotation units”, natural flotation is routinely used in all preliminary oil removal systems. This (biphasic) flotation can be preceded by coalescence (ensuring micro droplet agglomeration) in order to achieve a minimum size that encourages separation.
Figure 33 indicates the rising velocities applicable to hydrocarbon droplets of varying dimensions. These figures are used as the basis for calculating static oil separators (see section oil industry).

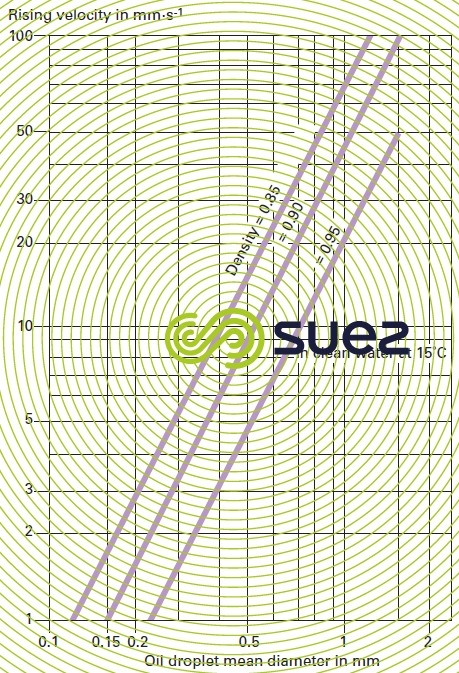

aided flotation (medium or fine bubbles)
air-aided flotation (medium or fine bubbles) without reagents
This is natural flotation promoted by injecting air bubbles into the liquid mass. This process especially applies to the separation of dispersed fats (solid hydrophobic particles whose surface, therefore, easily captures air).
For rough grease separation, air is injected through medium bubble (2 to 4 mm) diffusers, inducing turbulence designed to separate heavy, mineral or organic particles bound together with the fats.
For a more thorough fat separation as part of UWW pre-treatment, a mechanical aerator is used to diffuse fine air bubbles (from a few hundred μm to 1 mm). Thus, we achieve a state of quasi-flotation by accumulating floating matter and keeping it floating on the surface.
Please refer to section grease and oil removal, for a description of the different grease removal systems, including the 2-zone grease remover. The same process also applies in the grease removal zone of the Sedipac 3D, the system used in UWW and IWW treatment (see chapter flocculators – settling tanks – flotation units).
Aided or air induced flotation (medium or fine bubbles) and flotation using reagents and designated “mechanical flotation” or “foaming flotation”
These processes apply to niches that are very different to those of dissolved-air flotation: solid particle size and density, size of bubbles used, mixing conditions. Special reagents are used to alter surface tension. The most classic applications are listed below :
selective flotation used in ore concentration
Ore is crushed down to a size below 0.2 mm in order to release most of the rock’s component minerals. It is then used to form a suspension with water to which are added surfactants (collector, activator or depressor agents); these will adhere selectively to the surface of some minerals, rendering these surfaces more or less hydrophobic and allowing them to be selectively floated when a mechanical stirrer is used to combine the pulp, after being processed in this manner, with fine bubbles. This process uses considerable levels of energy that a hydroxide floc is incapable of withstanding. However, it does allow various minerals to be separated out from the same rock.
processing oil-laden water
When treating oil field water (water withdrawn from an oil well with the hydrocarbons), separating out the oils by mechanical flotation is also designated foaming. This separation is carried out by mixing air (or natural gas) into the water to be treated after it has been processed by adding an organic coagulant and/or a demulsifying agent. Flotation units can have one or more cells in series, with short retention times (3 to 5 minutes).
surfactant separation
Foaming generated simply by injecting air can also be used to separate out surfactants contained in water, or after surfactants have been added in order to draw the foam away, for example ink in wastepaper de-inking units.
Bookmark tool
Click on the bookmark tool, highlight the last read paragraph to continue your reading later
