applied activated carbon principles
Reading time:Activated carbon is available in two forms: powdered activated carbon and granular activated carbon.
activated carbon (PAC)
Powdered activated carbon is often supplied as particles measuring between 10 and 50 mm and is most frequently used in combination with clarification treatments. Injected continuously into water with the flocculation reagents, it penetrates into the floc before being extracted from the water with the floc (sludge).
In order to achieve a good PAC utilisation, we recommend using a sludge recirculation settling tank (Densadeg) or a sludge blanket settling tank (Pulsator, Superpulsator) (see chapter flocculators – settling tanks – flotation units. Both units are used to considerably extend contact time between the water and the carbon and, subsequently, to come closer to saturation capacities at equilibrium. In this way, achieving identical results, we have been able to save 15 to 40% of carbon by using a Pulsator instead of a static settling tank.
Similarly, using powdered activated carbon in the recirculation loop of an ultrafilter will remove dissolved organic matter, supplementing the removal of suspended solids by a membrane, see separation by membranes). This is the Cristal process (see separation by membranes). It should be noted that the carbon used is recovered in the backwash water and that this water can very usefully be returned to the inlet of a sludge recirculation or sludge blanket settling tank (when one is installed upstream from the membrane).
advantages
- powdered activated carbon is approximately 2 to 3 times cheaper than granular activated carbon;
- the amount used can be adjusted according to the pollution level when this is a known factor;
- its utilisation only calls for a limited investment when the treatment only comprises one flocculation-clarification stage (all that is required is an activated carbon dispensing unit) see photo 9 and powdered activated carbon (PAC);
- it has rapid adsorption kinetics because its extensive surface area is directly accessible;
Activated carbon promotes sedimentation by ballasting the floc

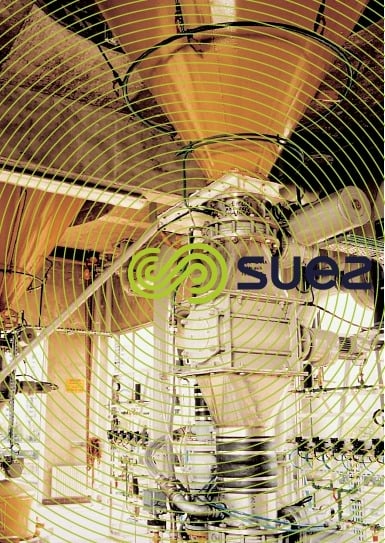

drawbacks
- Activated carbon cannot be regenerated when it is recovered mixed in with sludge;
- it is difficult to eliminate the last traces of impurities without adding excess activated carbon;
- if activated carbon is to be used at peak pollution times, it is absolutely essential to have the means available to detect these peaks;
- therefore, powdered activated bed carbon will mainly be used for intermittent or low dosage dispensing (less than 10 to 25 g · m–3 depending on the case); if not, regenerable granular carbons will have to be used on economic grounds.
granular carbon (CAG)
physical properties of granular carbon
The physical properties of granular carbons will vary widely depending on the product concerned (table 20).
Familiarity with these parameters will be absolutely essential when selecting and using activated carbon as part of a specific application.
useful capacity of carbon
Granular carbon is used as a filter bed through which the water to be treated percolates; the impurities contained in this water will then be methodically extracted; in effect, as the water is gradually cleared of its pollution, it comes into contact with activated carbon fractions that are less and less saturated and, therefore, increasingly active.

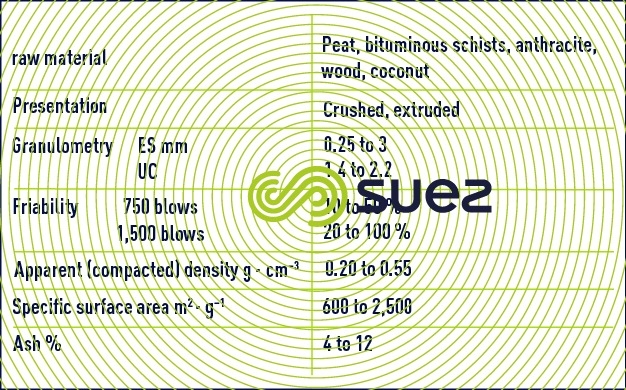

The cost-effectiveness of an activated carbon treatment will mainly depend on the carbon’s useful capacity expressed as g of pollutant (COD-TOC) fixed per kg of activated carbon, which regulates the "carbon consumed" in order to obtain a given effect. However, for a given system (polluted water-carbon), this useful capacity will depend on:
- bed depth: the deeper the bed, the better it will withstand extended adsorption fronts without excessive leakage (concept similar to that of ion exchanges, see section general and illustrated by figure 72) while ensuring total saturation of the upper layer; in practice, we use beds that are between 0.8 and 3 m deep, or even more in the case of concentrated water ( IWW ) ;
- exchange velocity: experience has shown us that we can rarely exceed 3 volumes of water to each volume of carbon and by hour in the case of high pollution levels (IWW). In consumable water treatment, where adsorbable product contents are low, the cost-effective optimum has to allow for the high investment cost weight and we have to accept a lower carbon saturation by using higher bed loads (5 to 10 vol·vol–1·h) ;
- the organic matrix of the water expressed as KMnO4 oxidability or TOC: The organic matrix competes with micropollutants for GAC adsorption sites; the GAC adsorption capacity for these substances will therefore decline as TOC increasese.

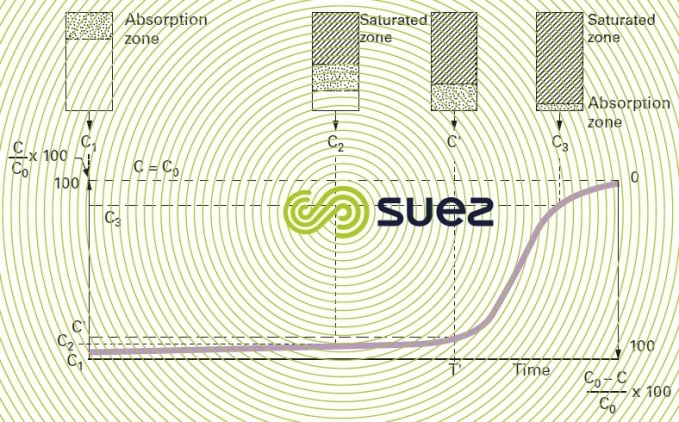

Theory only provides the direction in which these laws vary; therefore it is absolutely essential to seek the advice of a specialist and/or to carry out dynamic tests on sufficiently large columns for extrapolation purposes.
However, there are models that, based on laboratory experiments, can be used to calculate a carbon’s useful capacity (note: these models themselves have to be used by a specialist).
activated carbon bed functions
A compact bed fulfils four functions :
- filtration : As GAC is more friable than sand (if quartz) the washing frequency used should be reduced, thereby avoiding high TSS retention. Therefore GAC should in general be placed in the 2 filtration stage. Furthermore washing tends to make for a uniform layer and if the final reclassification is hardly pronounced, the adsorption head will be dispersed with a possibility of leakage of the pollutant;
- bacteria substrate(also termed activated carbon biological regeneration): this function contributes to purification but can also be dangerous if not wholly controlled (fermentation, odours, bed fouling, development of micro-invertebrates …), especially through careful wash management; this operating mode has sometimes been specially developed for drinking water treatment applications: instead of GAC, we then have BAC (biological activated carbon, see sectionthe BAC (biological activated carbon concept);
- reducing action(as a reminder, see sectionmain adsorbents); consequently, filtration through GAC must always be followed by a disinfection stage if the water is intended for consumption ;
- adsorption : this is the carbon’s main function (see following).
systems that use GAC
There are three possible arrangements :
- single fixed beds : this technique is widely used in potabilisation treatments (see carbazur activated carbon filters GH). As the carbon screens out the micro-pollutants, the adsorption front moves deeper (figure 72) and the spent carbon must be replaced with new carbon when the residual levels of micro-pollutants in the water reaches the alarm threshold C’. Otherwise, this level will rapidly rise to reach the incoming level C3. Spent carbon will either be discharged (in the case of a "non regenerable" grade), or regenerated using a further thermal reactivation treatment in a controlled environment ;
- fixed beds in series :for wastewater treatment, several columns are arranged in series and regenerated by permutation … (figure 73). Thus, a countercurrent extraction system is put in place. The Dual Flow Carbazur filter (see carbazur activated carbon filters GH) en est une variante avec deux cellules ;
- mobile beds : these beds also use the counter-current principle but with one single bed (figure 74). The base of the bed can be fluidised in order to facilitate saturated carbon extraction.

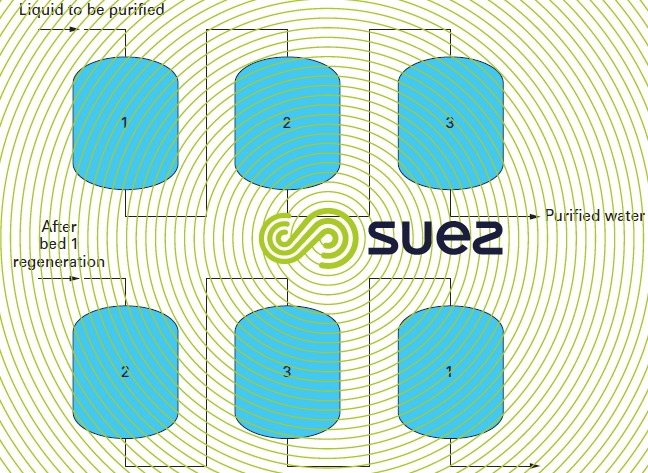


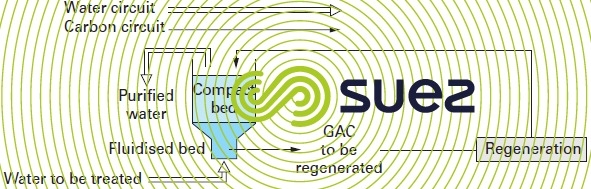

regeneration
(Activated carbon (like artificial adsorbents) is an expensive product. Most of the time, replacing saturated carbon would be prohibitive and that is why there is a need to be able to regenerate it; three regeneration methods have been developed.
vapor regeneration
This method can only be used to regenerate carbon that has only fixed a few highly volatile products (e.g. chlorinated solvents); however, steam can be an interesting option for clearing fouling from the surface of the granules and for sterilising the carbon.
thermal regeneration
Heating carbon to temperatures of approximately 800°C in a controlled atmosphere avoids igniting the carbon and pyrolyses organic matter adsorbed as small molecules that escape from the carbon and are burned in a post-combustion chamber. This is the most widely used method; it will thoroughly regenerate activated carbon but does have two disadvantages:
- this system calls for heavy investment; depending on the case, the system used will be a multiple hearth incinerator, a fluidised bed incinerator or a rotary furnace. This furnace must be fitted with temperature and atmosphere control devices, a dewatering system at its intake and a carbon quenching system at its outlet;
- these systems generate high carbon losses (7 to 10% per regeneration); this means that after 10 to 14 regenerations, statistically, the entire GAC mass will have been replaced.
These losses can be reduced by including electrical heating arrangements (infrared furnace, induction furnace). However, these are expensive techniques and, at present, only used to recover costly metals.
Note: a regeneration furnace can be installed on the operating site (large quantity used or site that is not easily accessible, e.g. photo 10). In most other cases, carbons may be regenerated through a service contract offered by producers.

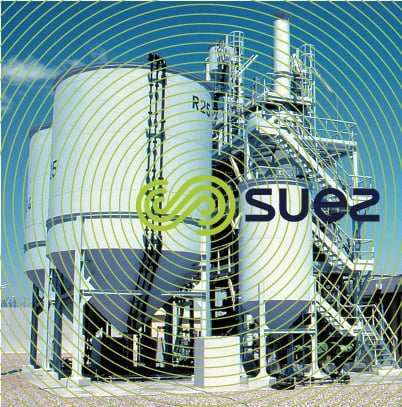

biological «regeneration»
The bacteria biofilm fixed on the GAC will mineralize all or part of the biodegradable fraction of the organic matter adsorbed and this can be regarded as continuous but partial bioregeneration; this system does not necessarily obviate the need for thermal regeneration but does increase useful adsorption capacity with regard to refractory molecules and extends the GAC service life between two heat regenerations.
Bookmark tool
Click on the bookmark tool, highlight the last read paragraph to continue your reading later
